June 21, 2024
How to Properly Install and Configure Your Hydraulic Pump System ?
In numerous manufacturing facilities and industries, hydraulic pump set ups are necessary. They operate by transferring mechanical energy into hydraulic energy that is used to run different kinds of machines or devices. Therefore, proper installation and configuration of a hydraulic pump system is very important for optimum performance and safety. In this guide we will give a summary on the factors to consider before installing, installation process, configuration and maintenance, troubleshooting, safety guidelines as well as other sources that can provide additional information related to any of these aspects. By following these guidelines you can make sure that you have properly installed, configured and maintained your hydraulic pump system so that it works at its best and prevents injury.

hydraulic pump set up
Factors to Consider Before Installation
Before installing a hydraulic pump system, it is important to consider a number of factors so that you select the right pump for your own specific needs. Factors to consider are discussed below:
- Flow rate: The flow rate of the pump is one of the most crucial things when choosing a hydraulic pump system. It is vital to get a pump that will deliver the desired flow rate for your application. This is usually measured in gallons per minute (GPM) or liters per minute (LPM).
- Pressure: Another very important factor to keep in mind is pressure required for your application. Pressure is measured in pounds per square inch (PSI) or bars. Choose a pump that can deliver enough pressure.
- Environmental factors: Important environmental aspects include temperature, pressure and noise levels. The fluid temperature must stay within the recommended range for the pump. Also change in temperature may affect pressure levels as well. Lastly, it is also important to think about how noisy the pump will be, and how this will affect its surrounding environment.
- Type of pumps: There are several types of hydraulic pumps such as gear pumps, vane pumps and piston pumps among others. Each type has its own advantages and disadvantages; therefore, it is essential to go for what suits your application best.
- Size: Size should also be looked at regarding which size of the pump you need. The selection process should take into account whether the applicant has chosen an appropriately sized device. If too small then it might not have enough power while if too large then it could result in energy wastage inefficiency.
These considerations will assist you choose an appropriate hydraulic pumping system before installation according with your individual requirements
Installation Process
Once you have selected the right hydraulic pump system, it is necessary to give it a proper installation to enhance its performance and safety purposes. Here are the steps:
- Choose its location: find a place that suits the pump system. It should be well-aired, not near any form of heat or humidity plus ample room for fitting and servicing.
- Mount the pump: The pump needs to be mounted onto an even surface. To securely attach the pump on a mounting surface, use bolts or other similar fasteners. Fixing the pump in such a way as to minimize vibration and make it become stable
- Connect pipes: Connect each pipe leading from the pumps making sure they are held properly. Always ensure that you employ correct hoses type rated for pressure and temperature of hydraulic fluid used.
- Install filters: Put appropriate filters into your hydraulic systems in order to keep fluid clean and free from contaminants. Filters must be easily accessible for servicing as well as changing them.
- Fill with hydraulic fluid: Fill up your system with an appropriate hydraulic fluid. In case of your specific pump system, always go by recommended type plus grade of fluid required. Ensure that filling process aligns with manufacturers guidelines including keeping required levels of fluids.
- Bleed the system: Bleeding out air in your hydraulic system is important especially when there is fullness of hydraulic fluids. This involves turning on the unit while opening relevant valves so that air can escape.
- Test The System: Ensure that your machine is working correctly through testing before you commence using it again. Therefore, check for leaking points, abnormal noise among others defects which may need rectification before starting operations.
If you follow these steps, you will install your hydraulic set-up correctly so that it starts working promptly without experiencing any glitches later ones due to poor fixation measures.It should be noted that during installation one has to refer always back to the manufacturer’s instructions as well any other safety requirements which may apply.
Configuration and Maintenance
For optimal performance and longevity, you must properly configure and maintain your hydraulic pump system. Some of the important factors to consider are:
- Optimize settings: Ensure that the pressure path and relief valve setting are correctly done for our specific use. Additionally, follow the manufacturer’s instructions to adjust these settings in their recommended range.
- Monitor Fluid Levels: Keep checking on fluid levels regularly in your hydraulic system and top up when necessary. You should always ensure that you use a proper type and grade of fluid, which is clean and free of contamination. Insufficient or dirty fluids can cause damage to the pump with resultant poor performance.
- Undertake Periodic Inspection: Regularly check the pump for any signs wear as well as damaged hoses. Also, look for leaks, cracks or other problems that may hinder its integrity. In case any component is destroyed, it should be replaced immediately so as to prevent further damage from occurring.
- Maintain right temperature: The hydraulic fluid should not exceed recommended heat levels at all times. Excessive temperatures may lead to damages on pumps thereby reducing their efficiency if not productivity. Consider installing additional cooling systems if necessary.
- Ensure cleanliness within the system: The area around the pump should be kept debris-free through cleaning procedures suitable for this purpose but avoid methods that would harm it.
- Timetabling usual repair work: This includes following a recommended maintenance schedule by manufacturers specific to your particular pumping system which could involve activities such as replacing filters or changing fluids among others. By doing this regularly, you will increase its life expectancy without having to spend much money on repairs.
Properly configuring and maintaining your hydraulic pump system guarantees optimum operation as well as eliminates expensive repairs or downtime issues associated with its breakdowns . Making reference to configuration and maintenance guidelines given by manufacturers plus observing safety standards when working on them is also paramount throughout such procedures like regulations too.
Troubleshooting
Despite being put in place properly, configured and maintained well the hydraulic pump set up may sometimes have problems. Here are some common issues that may arise and how to troubleshoot them:
- Leaks: Hydraulic system leaks come from damaged hoses, fittings or seals. Leaks should be checked for visually and hoses and fittings inspected to see if they show any sign of damage. Replace those which have damages.
- Improper performance: Other factors such as low fluid levels, blocked filters or spoiled components can make a pump not to give the required pressure or flow rate. Fluid levels and filters should be checked while inspecting the pump and hoses for spoilage.
- Unusual noises: Whining, grinding or clunking sounds are evidence of a malfunctioning pump or components around it. A visual inspection of the pump and hoses for damages will suffice.
- Overheating: High atmospheric temperatures, low fluid level or clogged filters could lead to overheating of hydraulic fluids. Fluid levels should be checked together with filters while considering the installation of a cooling system where necessary.
- Cavitation: During cavitation air or other gases become trapped in the hydraulic system making bubbles form then collapse. It has an effect on both performance decline and the wear of the pumps. Cavitation should be detected by strange noise or worsened boom and one must remove any air from it.
Your hydraulic pump set up may need professional help if you cannot diagnose nor solve its problem; besides punctual repair is essential so as not to experience further loss due to down time while regular maintenance coupled with check-ups can reduce some problems before having them at all.
Safety Considerations
When you install, configure and maintain a hydraulic pump set up system, you should always observe proper safety protocols. Here are some important safety considerations to bear in mind:
- High pressure: Operating at high pressures, hydraulic systems can be extremely dangerous if not handled properly. Whenever working around the hydraulic system, follow instructions from manufacturers and all relevant safety standards.
- Electrical shock: The operation of many hydraulic systems requires electrical power supply. One must observe all the necessary electrical safety measures such as switching off the power before touching any parts of the system and putting on protective clothing.
- Personal protective equipment (PPE): When dealing with a hydraulic system, it is crucial to put on appropriate PPE like gloves, goggles or masks. This helps reduce risks such as flying objects that can cause injuries.
- Proper lifting techniques: The hydraulic pump set up and its components may however be heavy and difficult to lift. Make use of correct lifting tools and procedures to avoid straining your back muscles or otherwise injuring yourself.
- Fire safety: In case fluids are mishandled by an individual during operation of a hydraulic system, there is possibility for fire outbreak in them Hydraulic systems require various fire precautions such as no open flames or sparks close to the hydraulic system
- Lockout/tagout: Prior to carrying out any maintenance or repairs on your hydraulic device ensure that you have followed the lockout/tagout procedures hence shutting it down completely and isolating it from electricity supplies.
To minimize chances of getting injured or property damage when installing, configuring and maintaining a hydraulics pump set up; it is vital that you follow proper safety protocols throughout the process. Always refer back to manufacturer’s instructions plus other applicable regulations on safety while doing so.
Resources and Additional Information
For more information on hydraulic pump systems, you can find a lot of resources. The following is a list of some useful resources:
- Manufacturer’s Manuals and Technical Specifications: Your specific hydraulic pump system manufacturer will provide you with detailed instructions and technical specifications for installation, configuration and maintenance.
- Industry Associations: Industry associations such as National Fluid Power Association (NFPA) have resources about hydraulic pump set-up and best practices.
- Online Forums: Fluid Power Forum is an example of online forums where tips are given by experts in the industry and other people who use them.
- Instructional Videos: There are many different instructional videos available on various websites showing how to install, configure and maintain a hydraulic pump system step-by-step.
- Professional Training: It may be worthwhile to consider attending professional training courses or workshops to learn more about hydraulic pump systems as well as best practices that apply.
To properly install, configure, and maintain a Hydraulic Pump System there is need to keep up with industry best practices as well as regulations so as to ensure it operates optimally and safely.
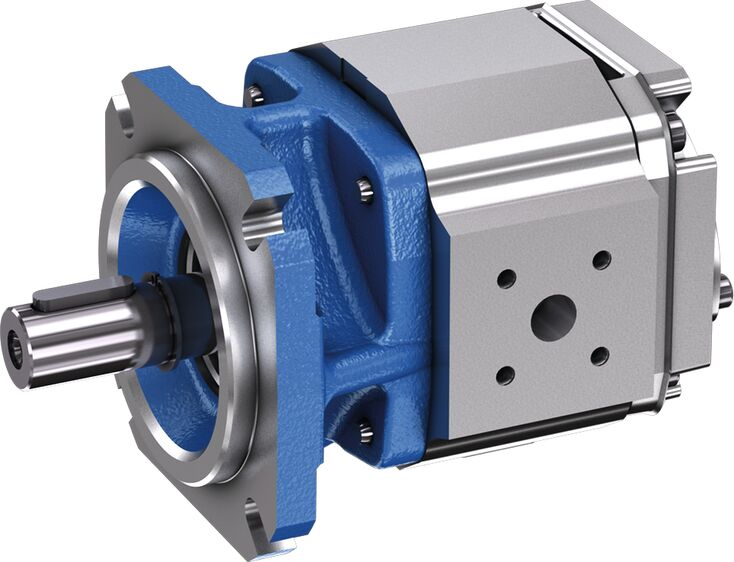
hydraulic pump set up
Conclusion
For optimal performance and safety, a hydraulic pump system must be properly installed, configured and maintained. By taking into consideration flow rate, pressure, environmental conditions, type of pump used etc., before starting the installation process one can select the right type of pump required for their needs. Following the correct installation procedure; proper configuration of the system for optimum performance; routine maintenance should be done so that you avoid any issues occurring which could shorten its lifespan. In case problems come up they should be dealt with promptly in order not to cause further damage or downtime. There are standard safety procedures that must always be followed when working with the hydraulic system. Keeping updated on current industry standards and guidelines will facilitate proper installation, configuration, and maintenance of your hydraulic pump system for optimum performance level safety.