June 21, 2024
Step-by-Step: How to Adjust Hydraulic Valves on Your Equipment
How to adjust hydraulic valves? Adjusting hydraulic valves correctly on machinery is an important aspect for best performance and longevity. Hydraulic valves are responsible for controlling the flow of fluid in a hydraulic system and can affect how well the equipment works if not properly adjusted. This outline will cover different types of hydraulic valves typically used in equipment, tools needed when adjusting them, step by step procedure on valve adjustment, common issues associated with it, overall safety precautions and additional information sources concerning this problem. Therefore, through adherence to these guidelines and proper adjustment of hydraulic valves in your machinery you will be able to avoid breakages and ensure high performance.
Tools and Equipment Needed
Specific tools have been designed for properly adjusting hydraulic valves. Below are some of the tools that may be required to adjust hydraulic valves in equipment:
- Wrenches: These wrenches come in different sizes hence they are always needed when one needs to loosen or tighten valve components during adjustment process.
- Pressure gauges: Pressure gauges assist in taking measurements before and after making adjustments on the valve so as to determine if there was any change.
- Hydraulic fluid: The fluid is used to fill up the whole system after adjusting the valve.
- Clean rags: Excess hydraulics from faulty mechanisms should be wiped off using clean rags during adjustment of this kind of valve.
- Valve adjustment tool: Specific adjustments may require specialized instruments; thus it is essential to check with manufacturer’s instructions for details about such a device.
- Safety equipment like gloves or eye protection should always be worn whenever working on systems involving hydraulics.
The correct tools must be employed depending on which type of valve is being adjusted at any given time. Follow manufacturer’s guidelines as well as regulations governing work within hydraulic systems. Good use of these facilities would aid securing appropriate valve setting while ensuring protected handling practices.
Step-by-Step Valve Adjustment Process
To correctly adjust hydraulic valves on equipment, one must follow a step-by-step process. Here are the steps for adjusting hydraulic valves.
- Locate the valve such that it needs adjustment and refer to the equipment’s manual or the manufacturer’s instructions to find out where the valve is.
- Remove valve cap: Use a wrench to loosen and take off cap of the valve. Safely keep this cap plus other elements in a place where they cannot be misplaced or destroyed.
- Valve Adjustment: Adjusting screw of the valve can be turned using a spanner. To increase pressure turn anti-clockwise while to decrease pressure turn clockwise. The proper amount of adjustment is found in manufacturer’s instructions.
- Test pressure: Check with pressurized gauge before and after changing position of hydraulic valve so as to know if there was any change made in pressure on hydraulic system. It is important to compare readings obtained from these pressures so as to confirm that the valve has been properly adjusted.
- Fill hydraulic system: Fill up the hydraulic system with hydraulic fluid if required. Depending on what machine you have got, use only that type and quantity of fluid for it per manufacturer’s manual.
- Test Valve: After making changes, ensure that this part works fine by performing tests on it. To ascertain its normal operation, switch on machinery and observe how it behaves.
- Replace Valve Cap: Once properly adjusted and checked, put back this valve cover following which secure it tightly using an adjustable wrench.
When adjusting hydraulic valves, it is essential that one adheres strictly to manufacturer’s guidelines together with any applicable safety precautions. Properly set valves would improve performance optimally thereby reducing chances when equipment might fail or have downtime risks because of misalignment or maladjustment.
Troubleshooting Valve Issues
Even with the proper adjustment, there may be a problem with hydraulic valves. These are some of the prevalent problems and their solutions:
- Leakages: After you have adjusted your valve and see a leak around it, you should make sure that its connections are tightened properly. The valve could have been damaged or needs to be changed if the leakage is still there.
- Performance Imbalances: Check system pressure within outlined limits once the equipment does not operate as anticipated after valve adjustment. When pressure is either too high or too low, adjust the valve accordingly.
- Noisy operations: Ensure that even A noisy operation will follow a range of pressure in a hydraulic system. If the pressure is normal, then it means that there could be damage to other parts of this system such as valves.
- Slow or Erratic Operations: Once an operator has made necessary adjustments on control valves and noticed that his machine is now moving sluggishly or erratically, he/she must ensure that the pressure in a hydraulic system will match required limits. Damage to some other parts of this system including valves might cause such conditions like these ones
Should you be unable to troubleshoot these problems, consider contacting a professional for assistance. Hydraulic valves and other components can always be repaired by a specialist who understands how they function exactly A person should always remember about following safety instructions when dealing with hydraulic systems, so manufacturer’s recommendations as well as any applicable health guidelines ought to be taken into account while solving troubleshooting tasks.
Safety Considerations
How can hydraulic valves be adjusted? If care is not taken, adjusting hydraulic valves on equipment can be dangerous. The following are important safety issues to consider while working with hydraulics:
- Wear personal protective equipment: Always put on suitable personal protective equipment like gloves and eye protection.
- Depressurize: To minimize the risk of injury, depressurize the system before repairing any hydraulic system.
- Use the right tools and equipment: When adjusting a specific valve, use the correct tools and equipment. Observe all safety regulations set by the manufacturer and other applicable bodies when dealing with such systems.
- Keep work area clean: Keeping work areas clutter free reduces risks associated with tripping or falling
- Avoid electrical hazards: Electrical hazards must be guarded against in hydraulic system operations. Do not operate from close proximity electrical equipments or cables unless they are properly grounded.
- Proper lifting techniques: Use proper lifting techniques whenever heavy machinery or components are being moved so as to prevent straining and injuries.
- Seek professional assistance: In case you do not understand anything about hydraulic systems, or if you have any doubts when it comes to adjusting a valve correctly, you should seek assistance from an experienced hydraulic technician.
By following proper safety protocols, you can minimize the risk of injury when working with hydraulic systems. It is important always refer back to manufacturer’s instructions and applicable safety regulations when dealing with hydraulic valves as well as other components.
Resources and Additional Information
For additional information concerning hydraulic valves and systems, there are a number of resources available. They include the following:
- Manufacturer’s manuals and technical specifications: Specific equipment manufacturers will give you elaborate instructions on how to adjust hydraulic valves.
- Industry associations: Hydraulic systems and best practices can be understood through industry bodies such as National Fluid Power Association (NFPA).
- Online forums: For example, Fluid Power Forum is a good source of advice from industry professionals or other users.
- Instructional videos: There are numerous online instructional videos that give directions in changing hydraulic valve.
- Professional training: One can also consider going for professional training courses or workshops to have more knowledge about hydraulic systems and best practices.
To ensure that your hydraulic system is properly adjusted and maintained for optimal performance and safety, staying up-to-date with industry best practices and regulations is important. Thus, by using these resources as well as adhering to the manufacturer’s instructions plus any applicable safety regulations, this enables proper adjustment of your hydraulic system which then functions at its optimum level.
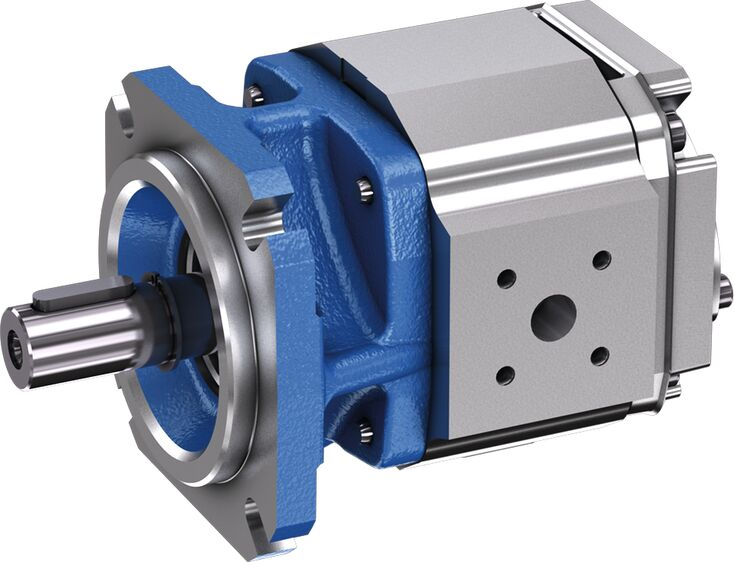
how to adjust hydraulic valves
Conclusion
How to adjust hydraulic valves. You need to tune up your hydraulic valves properly in order for them to work effectively and last longer. I will discuss the main types of hydraulic valves normally found on equipment, tools and devices that are required for their adjustment, a systematic approach to tuning these valves as well as how to troubleshoot common problems related with this subject, safety rules and additional sources of information. By following these guidelines exactly and adjusting the hydraulic valves on your machine well, you will achieve high performance levels while at the same time reducing the chances of breakdowns.
You must always follow the manufacturer’s instructions and relevant safety precautions when working with hydraulic systems. It is important to adhere to industry codes of practice and standards that aim at ensuring proper configuration and maintenance thus guaranteeing maximum performance and safety in a hydraulic system.