June 21, 2024
The Basics of Setting Up a One Pump Hydraulic System
A hydraulic system with one pump is called a 1 pump hydraulic setup. To make sure that it will work well and last long, you need to set up the 1 pump hydraulic system correctly. We will discuss the following points: components of a one pump hydraulic system, importance of planning and preparation before installation, installation process, configuration and testing, troubleshooting common issues , safety considerations , additional resources for information.
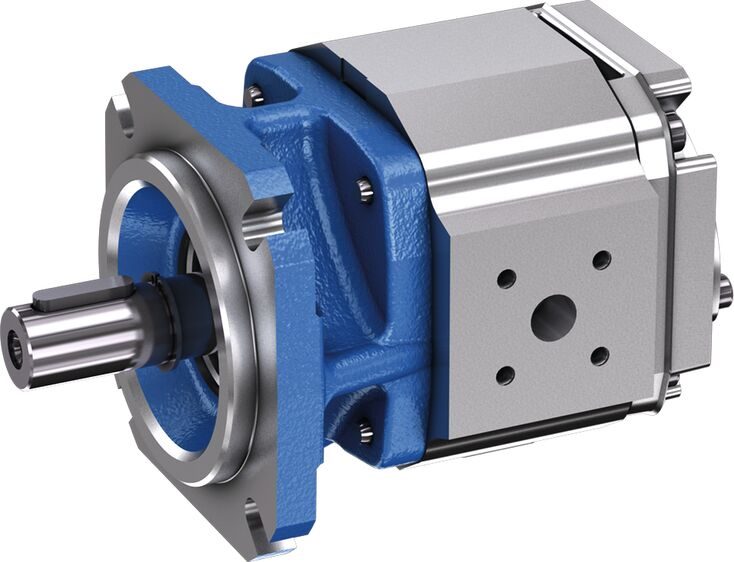
1 pump hydraulic setup
Components of a One Pump Hydraulic System
Several parts of a machine work together to enable it function as required. Here are the main components of a 1 pump hydraulic setup:
- Hydraulic Pump: This is considered the heart or soul of any hydraulics hence being responsible for creating power; pressure within a given range that drives an actuator such as cylinder or motor etcetera. There are different types namely gear pumps which have more mechanical contact resulting into higher efficiency even at low speed but also produce more noise due to continuous meshing; vane pumps having fixed displacement with only few moving parts thus less frictional loses while piston pumps offer better efficiency over wide range by varying number strokes per minute (SPM) among other advantages/disadvantages too.
- Reservoir: It refers to tank where fluid used in hydraulic systems is stored temporarily. In addition, this container acts not only as supply but also helps in cooling down oils when they get heated up during operation thereby dissipating excessive heat from surroundings.
- Valves: Valves control flow directionality of fluids throughout various paths within one pump hydraulics and its most important feature being ability to direct these liquids according their needs as well shut off completely when necessary so that no further damage occurs due lack or excessiveness thereof; relief valves normally open at high pressures relieving overloads on actuators , check valves allows unidirectional flow preventing backflow while directional control valves permits switching between different circuits depending upon functionality required etcetera
- Hoses: Hoses are flexible tubes designed carry fluids especially under high pressure. They can be made from synthetic rubber or plastic reinforced with braided wire for strength and durability reasons. Different types include suction hose , delivery hose , return line among others depending on their use within given system.
- Fittings: Fittings join various parts together thus creating a connection where needed most either permanently as well temporarily during servicing purposes only; they may consist male/female threads or even flanged ends which are tightened using nuts so that leakage does not occur at joints if correctly done.
Each of these components plays an integral role in the operation of any single pump hydraulic system. Therefore, understanding how each works will enable one choose suitable equipments for his/her specific machine needs based on performance levels required
Planning and Preparation
Planning and preparing are a must before setting up a one pump hydraulic system. Below are some things worth noting:
- Choosing the right components: Choosing suitable components for your machine is very important. This involves selecting the correct size as well as type of hydraulic pump and reservoir, hoses and fittings.
- Tools and Equipment: You will need proper tools and equipment to install the hydraulic system correctly. Some may include wrenches, pliers, torque wrenches and pressure gauges.
- Hose Routing: Plan hose routing before installing them. Ensure there’s sufficient clearance for hoses with fittings; also avoid sharp bends or kinks in hose lines.
- System Alignment: Proper alignment of systems is essential for their best performance levels; therefore make sure that both hydraulic pumps together with their reservoirs are well aligned horizontally.
- Proper Fluid Selection: Always pick an appropriate type of hydraulic fluid for your machinery depending on its specifications such as heat resistance etc., consult manufacturer’s recommendation while choosing hydraulic fluids.
By planning properly and making necessary preparations prior to setting up one pump hydraulics; you will acquire all required parts/tools for installation besides ensuring its proper positioning which can save a lot in terms of failure/downtime prevention thus leading into longer life-expectancy coupled with better functioning capabilities throughout this kind of systems
Installation Process
Appropriate establishment of a one pump hydraulic system is necessary for its best performance and durability. The following are the steps to properly install a single pump hydraulic system:
- Mounting the hydraulic pump and reservoir: Fix the hydraulic pump and reservoir in a safe place, ensuring that they are rightly aligned as well as level.
- Connect the hoses: Link up the hoses with hydraulic pump, valves and reservoir using appropriate fittings which should also be tightened accordingly.
- Valves installation: Put valves on their right places making sure they are well oriented then tighten them firmly enough but not too tight so that they do not break easily when operated or adjusted later on.
- System filling with fluid: Use an approved type of hydraulic fluid recommended by manufacturer only then fill up tank until it reaches recommended level provided by manufacturer. It is important to follow all safety rules concerning handling such dangerous substances like this one too.
- Air bleeding from system: Watch pressure gauge while watching where you should open required valve(s) to release some air trapped inside; after that close valve(s).
- System testing: Check if everything works fine or not during this test period after which leaks if any found shall be repaired otherwise necessary actuations done towards achieving desired functionality may include changing settings in valves or hose routing among others.
By doing so, one would be able to achieve greatest efficiency from their machines thereby reducing chances of breakdowns due to poor workmanship as well as down times caused by equipment failures resulting into losses. Always consult manufacturer’s guide plus relevant safety regulations throughout installation process of hydraulics since it has potential dangers associated with wrong handling procedures.
Configuration and Testing
Proper establishment and experimentation of a one pump hydraulic system is important for perfect actions. Below are various steps to configure and experiment with the one pump hydraulic system:
- Adjustment of Pressure Setting: Keep an eye on the pressure using a gauge while adjusting it wherever necessary according to manufacturers recommendations for correct pressure setting.
- Adjustment of Flow rate: Modify flow rate through use of right valves following manufactures instruction on how to do so.
- Setting Relief Valve: Adjust relief valve to ensure shielding against over pressurization in the system.
- Testing the system: Carry out tests on its functionality; check if there is any leakage or modify valve settings as well as hose routes where needed.
- Monitoring systems performance: Continuously monitor its operation by checking level of hydraulic fluid regularly coupled with carrying out routine inspections aimed at detecting any potential problems early enough.
You can achieve maximum efficiency with minimum downtime or failure risk by properly configuring this 1 pump hydraulics setup. It should be noted that all these procedures must strictly adhere to what is indicated by manufacturer’s guidelines plus other safety regulations applicable during configuration and testing stages of hydraulics.
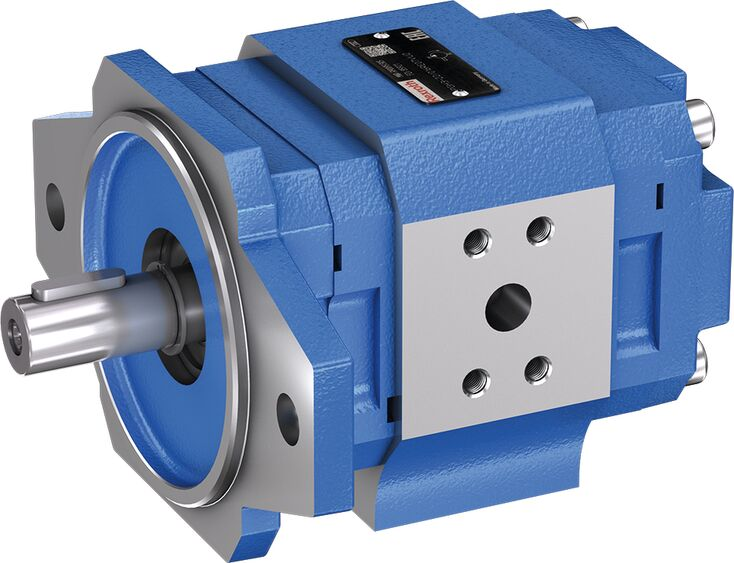
1 pump hydraulic setup
Troubleshooting
A one pump hydraulic system may experience problems even with good planning, preparation, installation, configuration and testing. Below are common problems and their troubleshooting procedures:
- Leaks: Ensure that there are no leakages from the pipes, connections or valves. Replace any damaged parts or tighten loose fittings.
- Wrong performance: If the system is not functioning as it should be, check pressure settings, flow rates and relief valve. Adjust accordingly if necessary.
- Overheating: Overheating can be caused by; inadequate cooling method employed; using dirty hydraulic oil or wrong pressure / flow setting. Verify cooling system being used is adequate enough for this job, cleanliness of hydraulic oil and also ensure pressure/flow settings are correct then make adjustments where necessary.
- Unusual noise: Strange sounds could mean cavitations or air entrapped within the system. Rectify these anomalies accordingly.
- Electrical: If power is not reaching the machine look into power source and electrical connections.
If all else fails contact an expert in this field otherwise it might be dangerous to continue on your own without proper knowledge about what you are dealing with here which is a one pump only hydraulic setup.
Safety Considerations
One pump hydraulic systems require proper safety protocols during their set up and use. These are some important safety considerations:
- Adhere to the manufacturer’s instructions: Always follow the maker’s instructions while setting up or using hydraulic system.
- Wear suitable personal protective equipment (PPE): Put on PPE like gloves, safety goggles and protective clothing when handling hydraulic fluid or working with a hydraulic system.
- Handle hydraulic fluid carefully: If mishandled, hydraulic fluids can be very dangerous. Ensure that all relevant safety regulations concerning its handling are observed and also dispose off used fluid in an appropriate manner.
- Watch out for high pressure levels: Hydraulic machines work under high pressures which can be hazardous if not handled correctly. Take necessary steps such as using pressure gauges so that you may know when there is need for relief valves in order to ensure safe operation of the system.
- Avoid electric shock risks: Take note of any electrical hazards associated with working on hydraulics; make sure all electrical connections are grounded properly as well as insulated against them.
- Be careful around moving parts: Moving parts within hydraulics could cause harm if mishandled thus one should be cautious enough whenever dealing with such areas by following necessary precautions towards working safely around them.
Following these safety considerations and taking appropriate precautions will help reduce accidents or damage during setup/use of a single pump hydraulic system.
Resources and Additional Information
Here are some more resources you can use to set up and operate a hydraulic system with one pump:
- Manufacturer’s instructions: Adhere to the manufacturer’s instructions for the particular type of hydraulic system you have.
- Standards and regulations: Keep yourself updated on industry standards and regulations pertinent to hydraulic systems. These standards and regulations may differ from one industry or location to another.
- Technical specifications: Check whether the technical specifications of your hydraulic components – pumps, valves, etc. – match those of your particular make of hydraulic system.
- Instructional videos: For individuals who learn better by watching than reading, instructional videos can be extremely helpful as they show how hydraulic systems should be installed and used.
- Training programs: There are training programs that are designed for advanced knowledge in hydraulic systems such as technicians or designers involved in setting them up.
- Online forums and communities: Participating in online communities where people share information about their experiences could help solve problems encountered during installation or usage phases of any given model/type of hydraulics system as well as provide tips based on shared hands-on expertise.
Compliance with industry standards, regular checking through manufacturer’s guidelines plus technical specifications adherence while also considering best practices could lead to maximum output levels being achieved through this single pump hydraulic system setup.
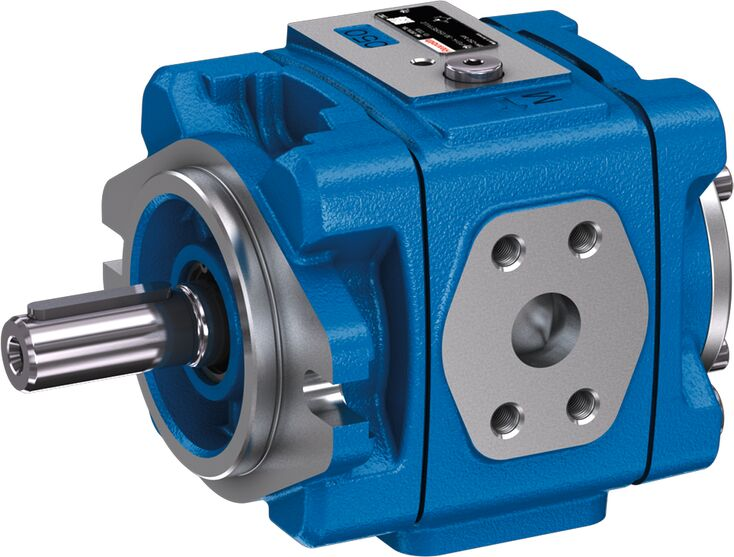
1 pump hydraulic setup
Conclusion
To achieve the best performance and safety possible, one must set up an ad correctly using a one-pump hydraulic system. You can guarantee that it works well and reduces the chances of breakdown or accidents by understanding system components, planning and preparation, installation process, proper configuration and testing, troubleshooting common problems as well as following necessary safety measures.
Therefore, while setting up a single pump hydraulic system ensure that you follow manufacturer’s instructions; industry standards such as technical specifications among others should also be taken into account during this process. This means referring to them whenever necessary so that everything goes smoothly without any hitches along the way. Keep yourself updated about what is happening in the industries related to your job description by sticking to relevant guidelines which are regularly reviewed for effectiveness since failing may lead to disastrous outcomes ranging from injuries sustained due to equipments malfunctioning through lack of information concerning their correct usage protocols.