June 21, 2024
Belt Conversion Size: Understanding the Differences Between Belts and Applications
Belts are an important part of industrial machinery as they help in power transmission and efficiency. Size is a key aspect that determines how well a belt will function. Belt conversion size refers to changing one belt with another of different dimensions or type so as to enhance effectiveness and performance of the machine. Proper belt conversion size selection cannot be overemphasized because it can lead to optimal utilization, reduced down time and minimum maintenance costs. This paper provides an overview on belt conversion size in relation to industrial machinery.
Choosing the right size of belt is very essential if you want your machine to work at its best. When a wrong sized belt is used power transmission decreases which results into low productivity and inefficiency. Undersized belts wear out quickly while oversized ones make machines slip hence increasing rate at which they wear off.
In subsequent parts we will discuss various kinds of belts with their applications, why correct choice matters most, what belt conversion size means plus dos and don’ts when dealing with this process. Additionally common problems associated with wrong sizing during conversion will be highlighted before concluding by reiterating significance proper selection for belt conversion sizes.
Understanding Belts and Applications
In many machines and systems, industrial belts are important for transmitting power or motion between components. V-belts, flat belts and synchronous belts are the most common types used in industry. Because of their ability to transfer huge amounts of torque, V-belts are the most commonly used type. Synchronous belts, on the other hand, offer exact and consistent control over motion while flat belts are used where little power needs to be transmitted or materials need to be conveyed.
Each belt type can be applied in different situations depending on factors such as load, speed and operating conditions. For example; v-belts work well with high-torque applications like conveyors systems in industries or even large motors in factories while synchronous ones are preferred when precision is required like in robotics manufacturing industry among others then again lightweight tasks for packing materials handling would call for flat belt drives too.
It is vital that one chooses the appropriate kind of belt for an application so as not only achieve good results but also enhance efficiency and longevity. If a wrong selection is made there may occur pre-mature wearing out of parts involved ,losses in generated power which could lead into increased maintenance expenses . Hence before settling on any specific unit several aspects such as load capacity; speed; temperature range during operation; environmental conditions around working area among many others have to be taken into account during this process.
Choosing belts correctly together with their applications will result into reliable performance reduction of costs incurred due frequent breakdowns thus extending life span equipment’s.
Belt Conversion Size
Belt conversion size is the process of altering a belt’s size in an industrial machine. There are many reasons why this might be necessary including power transmission enhancement, alteration of machine dimensions or setup and availability of more fitting belt sizes. It cannot be overemphasized how important it is to get the correct belt conversion size since it affects directly on the efficiency and performance of machines.
Right sizing ensures that there is no loss of power or performance at any point while running such equipment thereby enabling them to work on their fullest potential continuously which leads into higher productivity levels achieved within shorter periods alongside reduced downtimes as well as decreased overall maintenance costs. A belt which has been sized correctly also lowers down chances for getting machine damaged hence extending its lifetime.
There are several considerations that must not be overlooked whenever one is thinking about converting belts sizes and these include; power demands required by the device being used, pulley speeds as well as sizes involved during operation along with material composition among other aspects relating to types used for making belts. Therefore, it becomes vital that individuals consult professionals or manufacturers so as to know what kind of belt would fit best for a given application based on such factors.
The smooth working nature of machines in industries mainly depends on proper conversions done regarding belts’ sizes. When an individual follows standard conversion sizes closely then industrial equipment functions optimally thus maximizing output gains while ensuring profitability too.

belt conversion size
Types of Belt Conversion Size
It is essential to ensure that the replacement belts for industrial machines are of the right size; therefore, belt conversion size must be considered. Belt conversion size is when one replaces belts with different dimensions from those which were there before. This can be done if there has been a change in machinery being used, processing materials or it’s meant to enhance performance of the machine. The correct belt conversion size is important because it ensures that the equipment runs efficiently thus minimizing downtimes and maintenance costs while lengthening its lifespan.
The factors that should be put into account when converting belt size are; conditions under which machine operates, type and material of belts used, pulley speed as well as diameter plus required power transmission among others. It should also check whether new belt matches up with existing pulley or not and adjust tensioning force accordingly together with alignment too. If one fails to do so correctly then this may result into reduced effectiveness and productivity levels in addition to higher servicing expenses or even causing harm on equipments.
Before settling for any kind of belt conversion sizing method, individuals need to familiarize themselves with different types offered numerically, nominally or through cross-referencing charts among others. Each method comes along with its own merits but accuracy rates; simplicity during usage processes and availability might also count greatly in determining what suits best for a given situation.
In summary, proper belt conversion sizing plays a key role towards ensuring smooth running of industries’ machineries. Therefore, manufacturers’ instructions must be followed strictly while installing or maintaining such devices using appropriate tools and equipment as well.Businesses can achieve maximum efficiency within their organizations by following these steps.
Dos of Belt Conversion Size
Getting the size of a belt is simple as long as you measure the pulley and belt properly. The following are some of the key things to do when converting belt sizes:
- Right measurement: Both old and new belts should be measured rightly so that they acquire right sizes and fits too. Failure to measure them well may lead to great problems in how machines work.
- Choose appropriate material for belts: You should always select a belt whose material is suitable for what it does after being resized. This could differ depending on where the equipment operates from.
- Alignment adjustment, tension setting: For efficient working of any machine correct alignment as well tensioning are very important. While changing sizes ensure you have aligned them well with each other plus added necessary tension for their optimal performance during operations.
- Use proper tools and equipment: Accurate completion of tasks while changing sizes of belts can only be achieved if one uses proper tools together with equipment designed for this purpose alone; such error-free processes reduce accidents rates within organizations.
-
Maintenance should be done regularly and inspection also carried out often: Once you have changed size of your belts, make sure that there is regular maintenance done on them so that they remain effective throughout usage in different machines. This involves checking among others factors like wear among others.
These dos will ensure successful conversion as well continued efficiency in operation of machines.
Don’ts of Belt Conversion Size
There are some things you should do and at the same time there are certain things that you should not do also as far as belt conversion size is concerned. These “don’ts” will help to ensure that you do not make any errors which may negatively impact on the performance of the equipment or the safety of your workers.
- Incorrect measurement and installation of belt and pulley – A common mistake made by many people when it comes to belt conversion size is measuring and installing new belts or pulleys wrongly. This may cause a belt not to fit properly or withstand stress during machinery operation.
- Use of wrong material or type of belt – Another error that can affect the performance of your machines is using an inappropriate kind of material or type of belt. Different applications require different types of belts hence it is important for one to ensure that they use the right type.
- Proper tensioning and alignment – Properly tensioning and aligning the belts are very crucial aspects for machine efficiency. If this fails then there could be slippage, wear & tear among other problems associated with misalignment.
- Use low quality tools/equipments – Using low standard tools/equipment may make accurate measurement/installation difficult for a new pulley system; such mistakes can affect its functionality adversely.
- Neglect regular maintenance/inspection – Failure to regularly maintain /inspect after doing everything correctly about belt conversion size could still lead into future issues. Always check frequently whether all parts are functioning well so as to avoid costly repairs in addition to unnecessary downtimes at work place.
If you can avoid these mistakes commonly done by many people then chances are high that your belt conversion size will be successful hence making machines work at optimum levels.
Common Issues with Belt Conversion Size
Despite the fact that there’s a lot of advantages to the correct belt conversion size, there are some common problems that occur within this process. Here are some issues and their possible causes:
- Belt slippage – when the belt slips on the pulley leading to lower power transmission and reduced efficiency; it could be caused by wrong tension, worn out belts or pulleys, or incorrect alignment.
- Belt wear and tear – belts can eventually wear out through friction and heat thereby reducing their performance as well as efficiency; this may arise from many things such as wrong tension, misalignment, inadequate lubrication among others.
- Pulley Misalignment – if not aligned properly, the pulleys won’t let the belt run straight which in turn increases its wear & tear while also decreasing its efficiency; different factors like improper installation, damaged bearing/worn out bearings, damages on either side (pulley/belts) can cause this problem.
- Over-tensioning/Under-tensioning of Belt – over tightening results into more rapid wearing off hence making it less efficient and shortening its life span whereas insufficient tightening leads to slipping decreased power transmission thus reducing overall effectiveness.
- Inadequate Lubrication – right lubricant application is necessary for lowering down levels of friction plus heat generation that wears out belts together with pulleys; failure to do so will increase wear & tear rates, reduce efficiency rates and shorten lifespans.
It is important not only follow dos and don’ts about belt conversions sizes but also consult experts where need be during this process. Additionally carrying out regular maintenance coupled with frequent inspections helps one identify any potential issue before they become bigger problems.
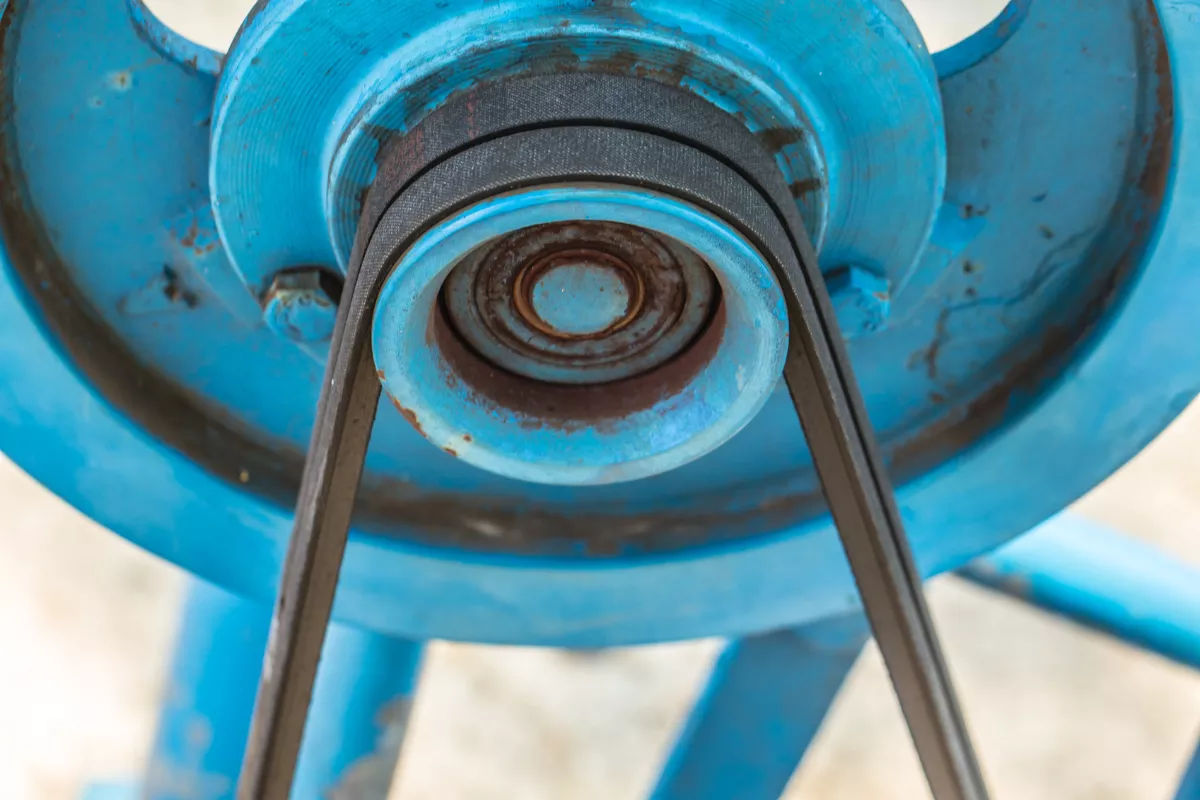
belt conversion size
Ultimately, the correct belts should be chosen and installed in order to run industrial machines smoothly and safely. It is possible to increase performance levels with right type of belt; this can also enhance efficiency thereby reducing downtime or maintenance costs while extending lifespan for the machinery. The guide for converting sizes of belts, taking measurements correctly together with calculations involving pulley systems as well as knowing what should not be done then doing it right through constant checking by experts and manufacturers forms part of these essential steps.
There are many things that need to be considered when selecting a belt such as operating conditions, materials used in making them, types available among others like speed ratios between different sized pulleys required for power transmission or even how often lubricating points should be serviced during routine checks up etcetera all depending on where they are applied. What one needs to do is choose appropriately according to these factors hence preventing cases where belts slip off their wheels; tear apart due to being weakly joined together; get misaligned because some were tightened too much while others weren’t enough etcetera which usually result into poor performance.
In conclusion, it is important that we select our belts well so that they do what they were meant for without causing any problems along the way. Choosing wrong specifications may lead not only underperformance but also serious accidents especially if heavy loads are involved thus putting at risk lives of people nearby who might be crushed by falling objects like big machines which move on such devices. The best thing anyone can therefore always take into account whenever dealing with this issue is safety first before anything else because once someone dies there won’t have another opportunity given again unlike other errors made during installation process.