June 21, 2024
The Advantages and Applications of a 3-Pump Hydraulic Setup
A 3 pump hydraulic setup is a hydraulic system that uses three pumps to power different components or functions. The arrangement comprises of three separate pumps which work together towards the efficient running of the hydraulic system through provision of enough power and pressure. It usually consists of a primary pump, a secondary one and an auxiliary pump.
The main pump is responsible for supplying the hydraulic system with the most important form of energy. Ordinarily, it has the highest flow rate and designed to handle most tasks. A secondary pump is deployed in driving specific parts or functions within the system which demand more power than what can be given by the primary one. In size, the auxiliary pump is the smallest among all three pumps that make up this arrangement; thereby used at low pressures or as backups incase one fails.
Some benefits associated with using a 3 pump hydraulic setup include increased efficiency, higher performance levels as well as being able to work under heavy loads. This means that when dealing with three pumps, there will be no straining any single pump since work can now be shared among them leading to longer lifespan overall for this type of hydraulics. Moreover, such kind enables someone use many functions at once thus elevating productivity in certain applications.
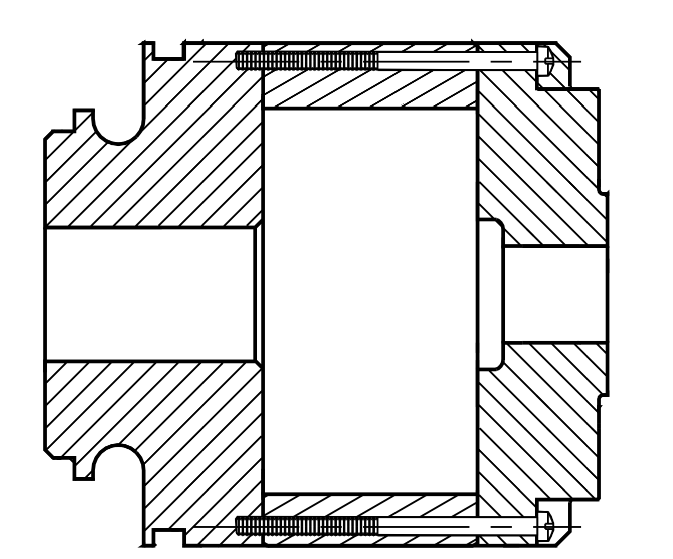
3-pump hydraulic setup
In conclusion, a 3 pump hydraulic setup remains powerful and efficient method for powering various hydraulic systems where additional power or performance compared against alternative configurations may be required.
Components of a 3-Pump Hydraulic Setup
For a hydraulic system to function with the necessary power and performance, it must consist of a three-pump setup. A number of components included in this setup work together. Besides pumps, valves and other auxiliary components are also required for proper operation.
Among all components that make up a three-pump hydraulic setup, the most significant are the pumps themselves. They generate pressure and flow needed to operate the system. Generally, these machines may be driven by an electric motor or internal combustion engine; therefore, they can either be classified as gear pumps, vane pumps or piston pumps depending on their design or functionality.
Flow control through any hydraulic circuit is managed by different types of valves present within it but particularly those forming part of three-pump systems where each one plays a unique role. Primarily used for controlling fluid directionality while check valves help in maintaining pressure levels during non-operation periods such as when equipment stops moving due to external forces acting against it like gravity force pulling down on load being lifted up which would otherwise cause sudden drop leading into cavitation resulting into rapid deterioration followed by catastrophic failure if not corrected promptly; then pressure relief valve starts working only when there’s excessive pressure build-up which opens up momentarily allowing some fluid bypass until normal level is restored again.
Filters, accumulators and pressure gauges can also be regarded as some of the additional parts that might comprise a 3 pump hydraulics set-up. Filters serve to get rid of any contaminants or impurities from within hydraulic fluids while accumulators store energy under compression form for future use during peak demand periods thus preventing frequent starting/stopping cycles on power units thereby extending their service life; on top of that pressure gauge act as indicator showing how much force exerted against an object by another so as not exceed its limits beyond what it was designed for thus avoiding accidents caused due overloading sensitive structures/materials unnecessarily.
Knowing what each component does in a three-pump hydraulic setup ensures correct functioning of the whole system. Inspection and regular maintenance should not be overlooked if reliability is to be achieved with such systems in place for long periods without failure occurring due to negligence or improper care being taken.
Applications of a 3-Pump Hydraulic Setup
A 3-pump hydraulic setup could be used in various applications which need high power output and exact control over the performance of the hydraulic system. Among the most common applications is heavy machinery and industrial equipment like cranes, loaders, or excavators. For example; these machines require great amounts of power to lift or move heavy objects from one place to another thus a three pumps hydraulic setup can provide such kind of power.
The aerospace industry also uses this kind of setup where precision as well reliability are critical aspects that cannot be compromised with at any given time. In aircrafts; hydraulic systems are used for landing gear extension/retraction, flap control up/down movement among others while still maintaining thrust reverser actuation etcetera so here even one small mistake may lead into serious accidents hence everything must work perfectly always even during emergencies.
Apart from that; automotive industry equally applies three pump hydraulics setups in various areas including but not limited to power steering/transmission control module (PCM) design as well brake systems management units too because all these require accurate, consistent controls over their performances at different times depending on what is happening around them so without such provisions being made then nothing good will ever come out from such components whatsoever.
In general terms a 3 pump hydraulic setup is suitable for use in applications requiring high levels of power output combined with precision control and reliability throughout operation regardless of location or sector involved.
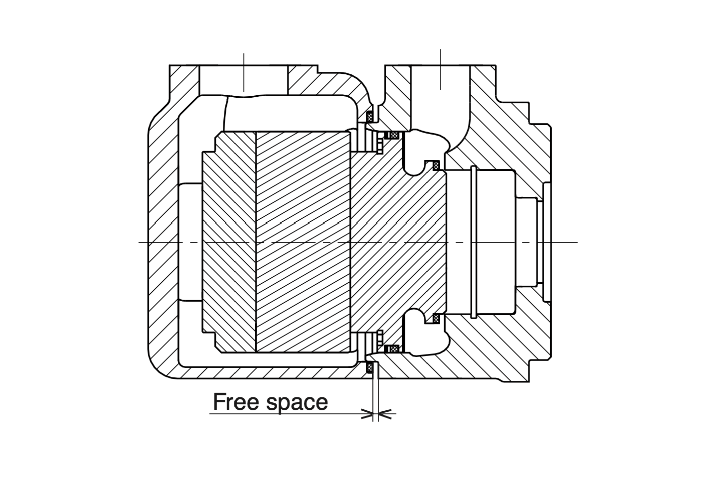
3-pump hydraulic setup
Comparison with Other Hydraulic Setup Configurations
Even though there are many benefits to a 3-pump hydraulic setup, we still need to think about how it compares with other types of hydraulic set ups. Two other common configurations are the 2-pump setup and single-pump setup.
A 2-pump setup consists of two pumps that work together in order for them to give power to the hydraulic system. The first pump is usually high pressure while the second one is low pressure. This kind of configuration is used where a lot of force is required within a short time.
On the contrary, a single pump setup only has one pump which provides hydraulic power to the whole system. It is mainly used in applications that need constant level of hydraulic power.
When compared against either 2 or single pump setups, 3 pump hydraulics provides more flexibility and control over hydraulic powers. With three separate pumps, different sections can be optimized for various pressures as well as flow rates requirements hence making operation much precise and efficient.
Besides being redundant by design another advantage offered by three pumps is redundancy; if one fails others will continue running thereby cutting down on downtimes and reducing chances for failures within systems themselves.
However not all hydraulic system applications may require or have room for three pumped ones . For lower powered systems one could use single pumped setups while high powered systems operating within short durations can use two pumped setups too.
In summary it depends upon specific needs depending on application type chosen among various options available based upon this analysis alone.
Maintenance and Troubleshooting
For a 3-pump hydraulic setup to work properly and last longer, it must be maintained accordingly. System failure can be prevented by regular maintenance and this also reduces the need for costly repairs. Similarly, troubleshooting should be done in accordance with the laid down procedures so that any arising issues can be identified and rectified.
One important thing when it comes to maintenance is checking the system often for signs of damage or wear. This involves visually inspecting pumps valves among other components for leaks cracks or any other forms of visible harm. In order to promote correct fluid flow within such a facility contaminants must not be allowed entry hence filters and strainers should also be cleaned after being inspected.
Calibration is another very crucial part of maintaining a three pump hydraulics set up calibration ensures that these parts work at right pressures as well as flow rates which are necessary for good performance levels. Those items found out of tune need adjustment or replacement depending on what fits best.
When dealing with problems linked to three pump hydraulics systems you should first establish where such problems are originating from. Common areas where issues may arise include areas where there are leakages reduced flow rate through the system abnormal noise etcetera; By knowing exactly why something has gone wrong one can take appropriate action towards fixing it.
Leakages could result due to several things including damaged seals or gaskets loose connections worn out parts among others therefore while trying to figure out what might have caused leakage inspect affected section(s) until source(s) becomes apparent then repair/replace damaged item(s).
Flow rate may reduce if filters get clogged up too much so always check them regularly likewise strainers need frequent clean up otherwise they will hinder optimal operation besides this situation could also arise because of pump wear and tear valve malfunctioning which calls for closer examination since some components might have become weak over time thus causing more friction thereby reducing their efficiency
There can be abnormal noises produced by air being trapped within the system loose parts or even bearing failures. Therefore during noise diagnosis locate where it originates from within the facility then apply necessary remedy accordingly.
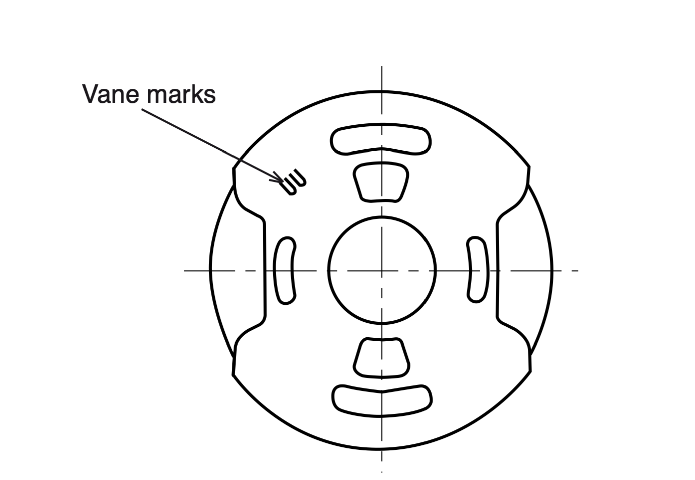
3-pump hydraulic setup
Industry Standards and Regulations
To make certain safety and dependability when using a 3 pump hydraulic setup, it is necessary to follow industry standards as well as regulations. These put in place rules not only for the benefit of workers but also for the environment which must be adhered to.
For this reason, Occupational Safety and Health Administration (OSHA) standards concerning hydraulic fluid power systems need to be considered too. Such regulations describe what should be done on hydraulic systems so that they can become safe and reliable where applicable such as those relating with hydraulic fluids, piping & hoses; pumps & motors; control systems among others.
Additionally, Environmental Protection Agency (EPA) has its own set of rules regarding this type of equipment. Their main aim is preventing pollution caused by hydraulics hence specifying disposal methods for hydraulic fluids used besides encouraging usage eco-friendly ones as well as components thereof if possible.
It is necessary that you engage an experienced engineer specialized in hydraulics who knows these laws so that he can ensure design plus installation comply with them. Falling short of meeting industry standards or statutory requirements might lead to severe safety hazards together with legal liabilities.
At the same time, there should be routine checks carried out on the three-pump system according to these guidelines for it to stay within such regulations always. Through inspections being done frequently by qualified staff will help guarantee safe operation while maximizing efficiency thus preventing any potential failure or even accidents from happening.
Environmental Impact of a 3-Pump Hydraulic Setup
When examining how a 3 pump hydraulic setup affects the environment, it is crucial to take into account possible spills and leaks of hydraulic fluid. Hydraulic fluid, which is potentially dangerous and harmful if not dealt with appropriately, can also be referred to as a spillage or leakage. Moreover, the energy needed for running all three pumps in such a system can cause greenhouse gas emissions that contribute to climate change.
To minimize environmental degradation brought about by this kind of arrangement, there should be regular inspection coupled with proper maintenance procedures aimed at reducing risks associated with spills or leakages; hence using environmentally friendly fluids that are safe for use in case they accidentally come into contact with nature’s surroundings. Further efforts could be made towards lowering power consumption through employing energy saving devices like efficient motors among other components used alongside pumps during operation.
Also, some manufacturers have started taking measures towards minimizing negative impacts on the environment caused by their products; for instance designing renewable powered hydraulic machines such as solar driven water heaters which can be used instead heating oil tanks during sunny periods. Other companies are coming up with more efficient models that produce less carbon monoxide gas emissions while still being able perform required tasks effectively.
Therefore it is important for enterprises involved in manufacturing different types of hydraulics equipment considering its lifecycle assessment analysis so as not only reduce but also offset any related pollution outputs.
Conclusion
A three-pump hydraulic setup has more benefits compared to other configurations of a hydraulic setup but whether it suits a particular hydraulic system application depends on a variety of things such as the equipment type and its required performance specifications.
In simple terms, a 3 pump hydraulic setup is a configuration of a hydraulic system that uses three pumps to run various functions of a machine or system. There are many advantages associated with this kind of set up which include higher efficiency, increased performance and greater flexibility. However, it also calls for more maintenance work as well as being complex than other types like single pump or two pumps configurations.
When determining if one should use 3 pumps in their specific hydraulics application; they need to look at factors like what is needed by way of performance specification, what kind of equipment will be used and availability skilled maintenance personnel among others. Furthermore, industry standards and regulations must be complied with so as not compromise safety and reliability levels within any given hydraulic system.
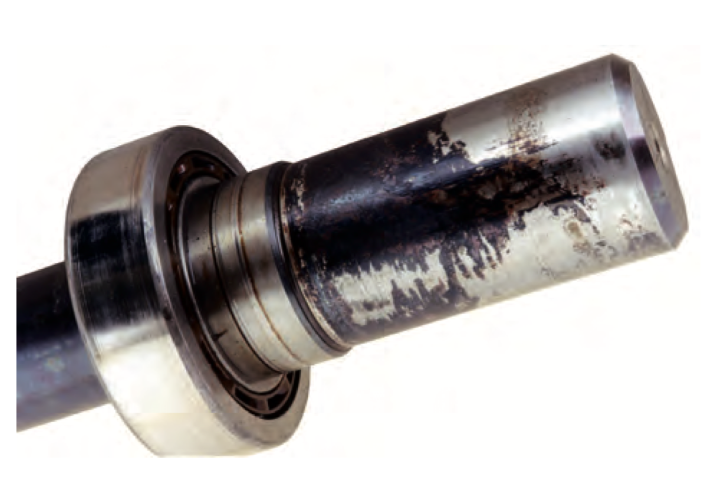
3-pump hydraulic setup
To sum everything up even though there might be several positive aspects brought about by three pump hydraulics setups over other forms; still it’s vital that people evaluate all their requirements against various setups configurations before concluding which among them will be most suitable for their needs. Optimum performance, reliability as well efficiency can only be achieved when one takes into account these aspects hence selecting the right design.