June 21, 2024
Designing a 4-Pump Hydraulic Setup for Optimal Performance
Commonly, hydraulic systems are used in various industrial applications like manufacturing, construction and transportation. It is a complex network of interconnected components that work together to create and send power by using pressurized fluids. The 4 pump hydraulic setup is one type.
Defining a 4 pump hydraulic setup and its applications
A 4-pump hydraulic setup refers to a kind of hydraulic system that uses four pumps to cause the flow and control it for the hydraulic fluid. Usually, there would be a main pump, two auxiliary pumps as well as one standby pump. In fact primary pump provides most pressure while auxiliary pumps also add required flow and pressure when needed. Standby Pump can be used in case of failure in other three pumps.
The 4-pump hydraulic setup can find application in various areas including manufacturing machinery, construction equipment, and agricultural vehicles. For instance, within an industry set up, such system could be employed for running of a hydraulic press or even robots arm. Conversely, since they run excavators, bulldozers and cranes this machine can be found on many types of construction equipment.
Explaining the role of each pump in the system
Every single unit within a 4- pump hydrodynamic build has assigned purpose which is generating fluid flow and regulating it inside these systems. The highest powered hydrodynamic element that makes sure the major proportion of brought about pressure into force is known as primary pump (Edwards et al., 2008). Concerning type, typically the main unit is variable displacement piston capable of adjusting flow rate as well as pressure in respect to moving liquid.
By contrast with this device which is less powerful than principal one but possesses higher flow rate utilized first auxiliary gear pump. Second auxiliary vane type discharges itself more efficiently than gear type however providing reduced flow volume.
Depending on the needs at hand one uses emergency small gear drivetrain referred to standby pump.
Discussing the importance of designing an efficient hydraulic setup
Design of an efficient hydraulic setup is important to guarantee optimal performance, reliability, and safety. Inefficient hydraulic systems can decrease productivity, increase energy consumption, and cause system component wear.
In order to design an efficient hydraulic set up there are some considerations that one should take into account such as choosing the right pumps, valves and hoses for a given application; optimizing the arrangement of components within this set up and finally determining flow rate required for best performance.
Meeting these factors into calculations will enable a well-engineered hydrodynamic unit to function at its highest level on which efficiency can be achieved thereby cutting costs that would have been incurred as well as boosting productivity . Moreover, having in mind that an effective hydrodynamic system can also reduce risks associated with accidents or failures thus improving safety in working places.
Identifying the Key Components of a 4-Pump Hydraulic Setup
A 4-pump hydraulics setup is a confusing system that requires various key parts to work properly. These parts comprise pumps, valves, actuators and hoses which are used together to generate and control hydraulic fluid movement.
Key Components of a Hydraulic Setup
Pumps: Pumps form the core of the hydraulic system since they provide the required pressure and flow to drive it. A 4-pump hydraulic system has one main pump, two minor pumps, and a standby pump; each having its own unique role in providing flow rate as well as pressure appropriate for specific use.
Valves: Valves help in regulating flow of hydraulic fluid within the system. The valves can be adjusted to control volume, direction or even pressure of fluid through electrical or mechanical controls. In hydraulic systems, directional control valves, pressure control values and flow control valves are among some types of valves deployed.
Actuator: Actuators convert hydraulic energy into mechanical energy. Mostly these involve driving cylinders by means of oil power in order to operate other machines like motors etc. Hydraulic actuators are preferred over mechanical actuators due to their smoothness, better accuracy as well as greater strength and speed than those offered by mechanical actuation methods.
Hoses: Hoses convey hydraulic fluids from the pumps to the actuators then back into the reservoir tanks. They usually have flexible materials like rubber or plastic that can tolerate high temperatures and pressures developed inside them. Choices for hoses depend on factors such as the application at hand and requirements on its flow rate plus pressure needs.
Different Types of Pumps Used in a Hydraulic Setup and Their Pros and Cons
There exist several types of pumps used in hydraulics with different advantages and disadvantages associated with each type. The major types of pumps employed in a 4-pump hydraulics setup include:
- Piston Pumps: These are mainly applied for most applications within any given hydraulic systems due to their high flows at high pressure. They serve as the major pump in a 4-pump hydraulic setup, though it is worth mentioning that piston pumps are also the most expensive and need regular maintenance to function properly.
- Gear Pumps: Gear pumps have less power than piston pumps but offer more flow rate. As auxiliary pumps in a 4-pump hydraulic setup, these gear types will be used. Gear pumps are simple, reliable and cheap but with less efficiency compared to piston type of pumping and therefore they cannot support systems under high pressure.
- Vane Pumps: These ones have higher efficiency compared to gear pumps plus their flow rates exceed those of similar gear types. For example, within a 4-pump hydraulics setup, vane pumps work as the second minor pump. Whilst also being expensive than gears, vane pumps are both efficient and dependable.
- Radial Piston Pumps: Radial pistons resemble ordinary pistons yet they give rise to more pressure together with improved efficiencies. Generally, they find use in cases where very high pressures are expected such as aerospace and defense industry. It is however important to note that radial piston pumps cost much and should be serviced regularly.
The generation and control of flow of hydraulic fluid to make it possible for machine to work is a critical function that each component in a hydraulic system performs. Generating pressure and flowing required for the system are the pumps, while valves are used for regulating flow rate as well as fluid pressure. Mechanical energy is produced from hydraulic energy by the actuators while hoses are responsible for conveying fluid from one actuator to another via pumps and back to storage.
The main pump gives most of the hydraulic pressure while there are other auxiliary pumps that provide additional flow when required.
Calculating the Required Flow Rate and Pressure for Optimal Performance
To ensure that the best performance is obtained, it is important to calculate flow rate and pressure requirements for a 4 pump hydraulic set up. The flow rate and pressure requirements will vary depending on the specific application as well as type of actuators used. This means that calculation of flow rate and pressure requirements takes into account several factors which include size of actuators as well as length of hoses.
How to compute the flow rate and pressure demands for a 4 pump hydraulic set-up
The first step in calculating the required force or torque output, which has to be generated by an actuator, is determining this. To do so, one must consider the load that has to be moved by an actuator plus how far away it should move such load.
When required force or torque output is known, we can now compute the flow rate and pressure using these formulas:
Flow rate = (required force or torque output) / (actuator area x actuator speed)
Pressure = (required force or torque output) / (actuator area)
Actuators’ area is determined by multiplying the bore diameter with π/4. Actuator’s speed may then be derived from either cycle time required or desired speed of actuating cylinder.
Factors affecting flowrate and pressure such as size of actuators and hose lengths
Several things come into play when determining what should be considered when designing a hydraulic system requiring varying volumes at different pressures. These things are among others: size of actuators; length of hoses; fluid viscosity; frictional losses within system.
Size of actuators stands out amongst them in this case since they determine both flowrate and pressure requirement. That means bigger cylinders will require more volumetric capacity than smaller ones.
Similarly, hose lengths cause significant variation in hydraulic fluids’ movement speeds resulting in different flows rates and pressures respectively too. Consequently there may arise need for bigger pumps due to losses experienced from friction.
What exactly defines the optimum flow rate and pressure for a given application
The optimal flow rate and pressure of a 4-pump hydraulic setup will depend on the specific application as well as type of actuators used. Generally, the minimum flow rate and the pressure required to move the load are set so as to minimize energy consumption while reducing wear on system components.
Another thing that is important is how human safety needs affect flow rate setting and pressure during this kind of operation. The system should be designed in such a way it can operate safely within the limits of its component pressures and flow rates.
Some other factors worth considering when determining flowrate and pressure requirements are fluid viscosity, temperature as well as presence of impurities in oil. These have an impact on both the performance characteristic of a hydraulic system and its longevity therefore have to be constantly controlled or watched.
Designing the Layout of the Hydraulic Setup
An essential part of the system design is the layout of a 4-pump hydraulic setup. The efficiency, safety and ease of maintenance can be improved by a well-designed layout for a hydraulic system. Many factors should be considered in designing the layout of a hydraulic setup such as location of pumps; valves and actuators; space constraints and ease of maintenance.
Discussing the layout of a 4 pump hydraulic setup, including the location of pumps, valves, and actuators
The exact application and space limitations may dictate variations in the layout for a 4 pump hydraulic setup. However, there are several general principles that should be followed when designing the layout.
Hydraulic fluid reservoirs near which pumps ought to be located because this will reduce the length of suction lines minimizing cavitation risks. The primary pump should be placed closest to the reservoir followed by auxiliary ones and standby one.
Actuators’ valves should be situated by them as close as possible because it will shorten pressure line lengths reducing pressure losses. Valves should also be positioned in such manner that they can easily be accessed during maintenance or repair works.
After all these precautions have been taken into account, their positions are chosen so that they move load efficiently. At times, it may require multiple actuators to move loads. Moreover, position selection for actuator’s placement should consider minimizing length of pressure lines thereby reducing pressure losses as well.
Providing examples of different layouts and their advantages and disadvantages
Different layouts exist that can be adopted in a 4-pump hydraulic setup, each having its own advantages and disadvantages. Some common layouts include:
- Inline layout: In an inline layout, the pumps, valves, and actuators are arranged linearly. This layout is simple and easy to maintain, but it may result in longer pressure lines and higher pressure losses.
- Parallel layout: In a parallel layout, the pumps, valves, and actuators are arranged alongside each other. Although this allows better control of the flow and pressure as well as lower pressure losses; it is more difficult to maintain.
- Radial layout: Pumps are located at the center of the system with valves arranged in a circular pattern around them in a radial layout. The design is more efficient and gives better control over the pressure as well as flow however designing and maintaining this arrangement might be more challenging.
Also considering space constraints when designing the layout
When coming up with a layout for a 4-pump hydraulic setup one should take into account space constraints together with ease of maintenance. Therefore, even though it should not take much space for its operation to be effective or maintained correctly.
Therefore for maximum use of space, components must be placed closely together using smart methods. On top of that ease accessibility is critical when it comes to maintenance or repair so that anyone can access them easily. Alternatively by utilization of modular components one could minimize space required while also simplifying maintenance needs.
Maintenance simplicity is also another important factor when coming up with a hydraulic system’s structure. The goal here therefore will be how minimum maintenance time and effort can be incurred in keeping this equipment running smoothly. For instance quick release fittings among them modular valves such as those which need occasional service or adjustment purposes could help reduce complexities linked with these aspects.
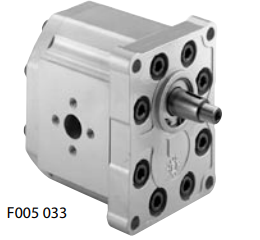
4 pump hydraulic setup
Safety considerations are equally important besides space limitations and ease of maintenance when planning where everything will go. This means that there has to be something done about any possibility of leaking and other safety hazards in the system. Additionally adequate spaces must be made around these equipments so that they can be used appropriately without endangering any individual’s life or even posing risks during maintenance tasks.
Selecting the Right Pumps, Valves, and Hoses
Choosing the right pumps, valves and hoses is vital to ensure the performance and longevity of a four-pump hydraulic set up. When selecting components, several factors should be considered, including cost, performance, durability, and compatibility with other components in the system.
Discussing criterion for choosing the appropriate pumps, valves and hoses suitable for a 4-pump hydraulic setup.
- Pumps: Flow rate, pressure and efficiency requirements of a system are supposed to be considered when one is selecting pumps for a four pump hydraulic setting. Pumps must generate necessary flow and pressure but consume little energy. These include dependability, maintenance needs as well as compatibility with other parts of the system.
- Valves: Valves are used to control fluid flow and pressure inside the system. On selection of valves it’s important to know which valve type is needed e.g. directional control valve, pressure control valve or flow control valve? Moreover you need to consider maximum flow rate as well as maximum pressure of any given valve. Other factors include reliability, maintenance requirements and compatibility with other components in the system.
- Hoses: Hoses are used in transporting fluid from pumps to actuators and back into reservoirs. Lengths diameter or materials that make up hose pipes must be taken into accounts before they are selected. Hoses should be chosen based on flow rates required by the systems such as pressures together with temperature viscosity of oil. Other things may involve wear resistance bending apart from being compatible with other componentries.
Pointing out advantages as well as disadvantages of different types/ brands/models/ makes of Pumps , Valves and Hoses.
- Pumps: They differ in terms of their pros and cons. Piston pumps offer high pressures , flows plus efficiencies but they are also expensive than all others . Gear pumps , however ,are simple—reliable—cheap although less effective not suitable for higher Pressures . Vane pumps are more efficient than gear pumps yet they are more expensive and can handle higher pressures.
- Valves: Different types of valves have their own good and bad sides. Directional control valves are used to control the direction of fluid flow, as opposed to pressure control valves which regulate pressure in the system. Flow control valves are used to vary the rate of flow. Consequently, the advantages or disadvantages for each valve type will depend on its specific application – use case scenario (environment) and system requirements.
- Hoses: There are numerous hose types that exist for hydraulic systems each with pros and cons. Rubber hoses are flexible and long lasting but may cost more than others. Thermoplastic hoses are cheap and lightweight but sometimes not fit for high temperatures. Also Teflon hoses do not corrode or get affected by heat but they can be stiff comparing with other hose materials available today.
When selecting components, it is important to consider cost, performance and durability. While the costs should not be overlooked; it should rather be expensive or otherwise. The only key factor under consideration is the cost of workmanship, but this is not a correct perception as some expensive materials could have an advantage in terms of quality and strength that will make them have a longer life span and result in lower maintenance on hydraulic systems.
Moreover, another thing that we must take into account is the performance of our selected components. In order to minimize the consumption of both energy and wear on system, these constituents should produce the expected flow rate as well as pressure. It will also affect the reliability and safety levels of the system.
Implementing Safety Measures in the Hydraulic Setup
Safety standards have to be observed otherwise hydraulic systems can pose as a danger. Furthermore, the high pressure and force involved in the operation of the system can cause serious injuries or even death. It is important to take into consideration safety measures when protecting workers and preventing damage to the hydraulic system.
Discussing the potential hazards associated with a 4-pump hydraulic setup, such as leaks and overpressure.
Among them include
- Leaks: Hydraulic fluid leaks can be a dangerous safety hazard. The liquid is under very high pressure and it results in serious burns if it comes into contact with skin or eye. Also, these leaks may create damage for hydraulic component as well as decrease its lifetime.
- Overpressure: Overpressure in the hydraulic system could result in component damage and pose a safety threat. There are two causes of overpressure – failures of one of components or incorrect operation of entire system.
- Explosions: In extreme cases, if enough pressure builds up within them, then hydraulic systems could explode leading to severe injuries or even death.
Providing examples of safety measures that can be implemented, such as pressure relief valves and regular maintenance checks
- Pressure relief valves serve to release excessive pressure build-up from the hydraulics. These devices work by opening at an already set amount of pressure so that surplus fluid can escape. Pressure relief valves should be placed at specific positions within the structure for protection purposes against harm on man-force aspects within it.
- Regular maintenance checks carried out will help identify hazards that might result into major safety risks. Maintenance checks must check for signs of wear or damage on components, level or quality of fluid as well as test system’s flow rate & pressure too.
- Training: Proper training helps ensure safe operations during use of this hydraulic equipment/ Tools require user manuals that guide their operations together with providing information about residual dangers involved in their usage by human beings.
Discussing the importance of adhering to safety standards and regulations
Adhering to safety standards and regulations is necessary for the hydraulic system’s safe operation. Such as, the Occupational Safety and Health Administration (OSHA) regulations or National Fire Protection Association (NFPA) standards are among some of the safety standards and regulations that apply to hydraulic systems.
These laws and guidelines include specifications for designing, installing and operating hydraulic systems as well as the accompanying safety measures. By abiding by these regulations, accidents will be minimized while the protection of both workers and the hydraulic system is ensured.
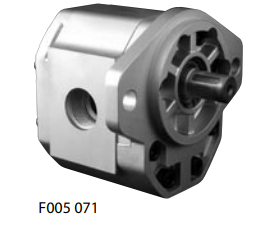
4 pump hydraulic setup
Testing and Tuning the Hydraulic Setup for Optimal Performance
To make sure that the 4-pump hydraulic setup is at its optimal performance, it has to be tested and adjusted. Testing enables the identification of potential system problems which can be improved accordingly. Tuning allows optimization of this system for a specific application such that it will be running at its maximum.
Discuss the importance of testing and tuning a 4-pump hydraulic setup to ensure optimal performance
The need for testing and adjusting a four pump hydraulic set up in attaining peak level performance
Therefore, without running test on the above mentioned hazards may result in the situation where you do not even know what is going on inside your workplace.
Provide examples of testing methods such as flow testing and pressure testing
- Flow Testing: This entails measuring how fast hydraulic fluid flows through the entire system. The average time taken by a fluid with known volume passing through any piece of equipment within the system can also measure this flow rate. If there are restrictions or leaks within the circuit, flow tests can identify them or confirm correct flow rates.
- Pressure Testing: Pressure Testing determines at which different points within the hydraulic system pressure is measured. Depending on some pressure gauges or sensors, measurements can be taken. It identifies leaks or overpressure in the circuit as well as ensures that internal pressure meets standards.
Discuss why it’s important to monitor and adjust setup as needed
Monitoring and adjusting for optimum performance of a 4-pump hydraulic setting is necessary. Frequent checkups may help detect probable glitches before they get severe. Adjustments can be made towards making it match its particular use hence optimizing its functionality.
Regular monitoring might involve checking for visual instantiations of parts, level plus quality assessment for fluids besides assessing pressure together with stream quantities inside this network while adjustments could take place in terms of replacing worn out components, changing pressures together with flow levels while reconfiguring layout among others.
By doing these actions you are able to identify possible problems earlier thus saving you a lot of time and money in the process. This means that it will be running at its top performance and efficiency, in addition to being safe and reliable.
Maintenance and Troubleshooting of the Hydraulic Setup
Maintenance and troubleshooting of a 4-pump hydraulic setup will help in ensuring that the system is able to live for longer periods and operate optimally. Proper maintenance also helps to avoid problems that may occur as well as prolonging the life of components. Troubleshooting, on the other hand, helps to identify and fix issues that arise.
Discussing the importance of regular maintenance and troubleshooting of a 4-pump hydraulic setup
Regular maintenance and troubleshooting of a four-pump hydraulic setup are key in ensuring that the unit runs most efficiently. Appropriate maintenance can help prevent possible problems such as leaks, clogs or component failure. In case there are issues, it is necessary to carry out trouble shooting.
Proper maintenance could mean regularly carrying out inspections for these parts; replacing worn out/broken parts, monitoring fluid levels including quality among others. This can involve identifying damaged components and replacing them, clearing any blockages or adjusting flow rate or pressure.
Doing regular servicing such as maintaining with repairs would help curb potential issues before they become big problems hence having sustainability in component’s lifetime and increase productivity in terms of performance.
Identifying common issues and their causes such as leaks and clogs
- Leaks: Worn-out hoses or seals, insecure fittings or connections, overpressure are some factors responsible for Hydraulic fluids leakage. Leaks can cause danger while affecting the functioning of various elements within .
- Clogs: Contaminated fluid or foreign objects within hoses or other hydraulic circuitry parts constitute clogging in hydraulics systems.For example They lower efficiency and performance as well as affect different structures present thereby leading to its damage if not handled properly.
Providing examples of maintenance tasks and troubleshooting techniques for different components of the hydraulic setup
- Pumps: Pump check up should include monitoring levels & quality along with changing old seals/bearings then inspecting pump wear/damage signs whenever necessary.Meanwhile pumping it into another hat measures like replacing broken items can be employed; otherwise, the flow rate might have to be reviewed.
- Valves: For Valve on the other hand, we may need to clean or replace the spool/cartridge of the valve as well as check it for proper operation and look into its condition. As a result, replacing components that were damaged is also among alternatives that may be used in troubleshooting aspects such as adjusting pressure or flow rate in this case it has either clogged valve inlet or outlet
- Hoses: When it comes to hoses, tasks like checking them for wear/damage and replacing those ones are done while ensuring that they are correctly routed and connected. Identify damaged hoses and replace them, clear hose clogs or adjust for length changes by increasing pressure or decreasing flow rates.

4 pump hydraulic setup
By performing regular maintenance tasks and troubleshooting techniques potential issues with the hydraulic system can be identified and addressed hence ensuring that the system continues to operate effectively and efficiently.