June 21, 2024
Understanding the Key Components of a Hydraulic Main Pump and Their Functions
Hydraulic main pumps serve as the heart of hydraulic systems, giving them enough power to move fluid around the system and drive various components like cylinders, motors and valves. These types of pumps are used in a range of applications including construction equipment, industrial machinery and agricultural machinery.
The role of a hydraulic main pump is to convert mechanical energy into hydraulic energy, which in turn is used to create flow and pressure within the hydraulic system. Flow and pressure generated by the pump are very significant to the performance of a hydraulic system because they define how fast or powerful it must perform.
Several different types of hydraulic main pumps have been identified that possess their own unique set of characteristics and applications. Some common forms include gear pumps, vane pumps and piston pumps among others.
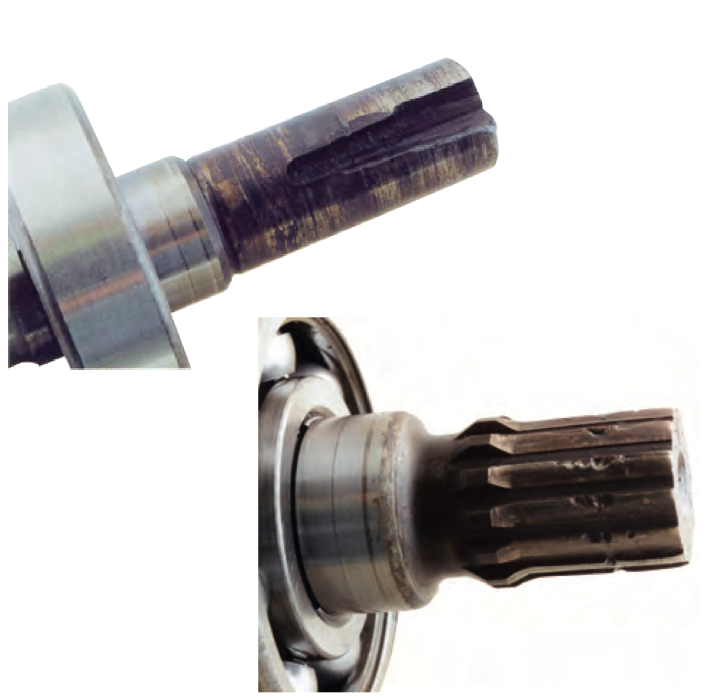
hydraulic main pump
Gear pumps are simple in design because they consist solely of two gears – one driving gear which drives another gear rotating in opposite direction. As gears rotate, they create a vacuum at the inlet port so that fluid can be drawn into the pump. The liquid then gets carried between teeth and as it goes through discharge port.
Vane pumps make use of sliding vanes moving back-and-forth in slots bored inside the housing for this purpose creating flow and pressure. They form chambers both filled with and emptied out fluids when these vanes withdraw or extend thus leading to required flow as well as pressure.
Piston pumps have piston pistons reciprocating inside them in order for flow and pressure creation processes to take place by this way . Piston movement sucks fluid by drawing it from pump while pushing it through discharge outlet . Though more complex than other types of hydraulic main pump; pistons retain their status due to their high efficiency as well as dependability but also expensive.
To sum up, hydraulic main pumps play a crucial role in hydraulic systems whereby they generate sufficient power required for directing fluid motion in addition to operating such components making up these systems. To select an appropriate pump for a specific hydraulic system, it is important to understand the various types of hydraulic main pumps and their applications.
Components of Hydraulic Main Pumps
When it comes to of hydraulic main pumps, much like any other type of pump, they are typically made up of different parts that combine forces together in order to ensure proper functioning. For the hydraulic pump to operate properly, it is important that one grasps what each component does. Hydraulic main pumps have several parts including the relief valve, impeller and pressure switch.
The casing is a protective outer layer that encloses all the components inside the pump. Normally made from cast iron or aluminium, the casing is designed to be able to bear high pressures and flow rates. The suction and discharge ports are found in the casing as well.
The rotating part of the pump which creates pressure by transforming mechanical energy into hydraulic energy is called an impeller. This component usually contains steel or bronze materials as well as specifications on how much pressure and flow rate it ought to make. It will then force fluid through the pump at a very high speed via its rotation causing fluid outflow through discharge port.
The inlet port serves as an entry point for fluids from reservoirs, whereas outlet port acts as an exit point for fluids discharged from pumps towards hydraulic systems. These ports can withstand high flow rates and pressures on opposite sides of them adjacent sides within their housing.
A relieve valve can be found beside to outlet port in most cases serving as a safety device for maintaining hydraulic system’s pressure levels. When pressures get too high it opens allowing some oil out so that no damage occurs on both pump and other components.
Additionally there is always another safety mechanism referred to as a pressure switch used for monitoring pressure in hydraulics systems often located near outlets ports hence when threshold level exceeds this switch disconnects power supply directly from such pumps preventing damages on them as well as other components making sure that all these activities occur safely.
Functions of Hydraulic Main Pump Components
Hydraulic main pumps consist of different components which work together to produce fluid pressure and pump the fluid through a hydraulic system. Understanding what each component does is vital for the proper operation of the pump. In this section, we will explain the various functions of key components of hydraulic main pump.
- Pump housing: The outer shell of a hydraulic main pump is called the pump housing and it contains other parts. It is usually made from cast iron or aluminum materials that are very strong so as to resist the high pressures and temperatures found inside the pump. The design also ensures that fluids can flow easily without any interruption or depletion in pressure.
- Impeller: This is one part that moves liquid from inlet to outlet ports in a rotating manner. Impellers are well built to force water into the unit and then out again. Often, they are made using strong materials like stainless steel since they may experience wear and tear due to rotation.
- Inlet and outlet ports: Fluid enters into the pump through an inlet port which is an opening on its body while leaving it via an outlet port which serves as its hydraulic system’s entry point. These openings lie opposite each other on either side of the pump casing, with connections being established through tubes or hoses running between them.
- Relief valve: Within the pump there is a relief valve, which keeps hydraulic pressure within safe limits. When excessive pressure threatens vital parts like pumps themselves, relief valves act by relieving it hence saving from unnecessary damages.
- Shaft seal: A sealing device installed at one end of a shaft where it exits allows no medium flow out from the machine; it’s called shaft seal. Typically, this material comprises soft rubbers such as silicon rubber or thinnest synthetic rubbers so as not to leak oil all over.
- Bearings: Bearings are needed by impellers that rotate in these pumps as well as their shafts for support throughout motion process. These bearings are usually metallic e.g. steel or even non-metallic (ceramic) and they are designed to bear the tortuous rotations of the materials in question.
In summary, the main components of hydraulic main pumps work together to create fluid pressure and pump the fluid through a hydraulic system. Understanding what each part does is essential for proper operations of the pump as well as efficiency of the entire hydraulic system.
Types of Hydraulic Main Pump Control
Hydraulic main pumps may be controlled in various ways including manual control, remote control or electronic control. Each method has its own advantages and disadvantages with the appropriate control method depending on the specific hydraulic system and its requirements.
Manual control is the simplest way of controlling a hydraulic main pump; it involves using mechanical levers or knobs to adjust the flow rate and pressure of the pump. Manual control is simple, dependable but not appropriate for complex hydraulic systems that require accurate dynamic controls.
Remote control allows an operator to use hydraulic signals or electrical signals to remotely operate a hydraulic main pump. This method is particularly useful when dealing with applications where access to the pump is difficult or when an operator must be located elsewhere from the hydraulics system. Depending on how complicated your hydraulic system is, remote control can either be manual or electronic.
Electronic Control System: this is one of the most advanced as well as precise ways through which you can manage a hydraulic main pump. It uses sensors together with electronic controllers in order to monitor as well as adjust flow rates and pressures within the pump. Electronic controllers provide opportunity for precise dynamic controls over your hydraulics, hence enhance efficiency as well as performance. However, there are higher expertise levels needed in maintaining these kinds of devices and also they are relatively expensive compared to other controlling methods.
In general, selecting an appropriate control method for a hydraulic main pump largely depends on factors such as required flow rate/pressure level, complexity of the system involved and hence operator’s proficiency level among others specific considerations for each particular case under consideration in this work piece. These factors should be taken into account carefully while choosing a method for controlling a Hydraulic Main Pump.
Maintenance and Troubleshooting
Hydraulic main pumps are an important part of hydraulic systems and play a crucial part in the performance of the system. Proper maintenance and troubleshooting of these pumps are essential to their peak condition and reduce pump failure downtime.
Regular checking, cleansing, and adjusting are required for having properly functioning hydraulic main pumps. It is necessary to adhere to the manufacturer’s suggested maintenance schedule as well as procedures. These include examining for leaks, worn out or damaged parts, and appropriate greasing.
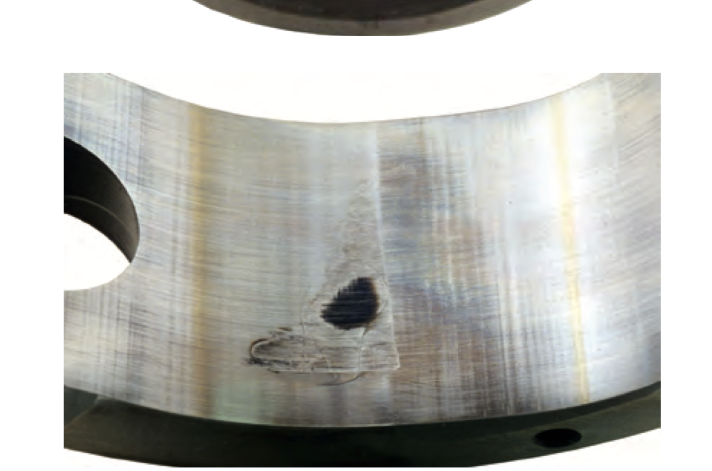
hydraulic main pump
Besides regular servicing, it is necessary also to diagnose problems that could come up with hydraulic main pumps. Some typical issues involve noisy pump operation, inadequate pressure or temperature increases among others. In such cases some factors can be attributed like broken down parts due to wear and tear, poor fixing or wrong fluid thickness respectively.
To do this requires that you identify the problem from where it originates so that you can take action in response. This may entail replacing worn or damaged parts, adjusting fluid levels or viscosity, or repositioning the pump for optimal flow.
Proper maintenance and troubleshooting of hydraulic main pumps can help ensure their reliable and efficient operation, leading to increased productivity and reduced downtime. To ensure effective functioning of hydrokinetic systems during these activities they should be carried out by a skilled professional who has other technicians assisting him/her here.
Industry Standards and Regulations
Hydraulic pumps are a major part of hydraulic systems and they must be designed to adhere to regulations and standards within the industry. There are numerous requirements, both in form of standards and regulations that have to be observed when using hydraulic main pumps in hydraulic systems.
One of the essential standards is ISO 9001that was developed by International Organization for Standardization (ISO). This standard specifies the conditions for quality management system, thereby ensuring that products and services consistently meet customer requirements and regulatory requirements.
Moreover, a variety of safety criteria including US Occupational Safety and Health Administration (OSHA) rules as well as European Machinery Directive must be complied with by hydromain-pumps. These directives ensure that hydromain-pumps satisfy safety conditions hence preventing accidents or injuries.
Another important regulation is environmental compliance. Such regulations include but not limited to the Environmental Protection Agency (EPA) in USA for instance and then RoHS Directive being one amongst others from Europe. Such compliance ensures that these hydromain-pumps do not pollute the environment but rather they will be sustainable.
It should be borne in mind that compliance with industry standards and regulations is not only mandatory but it is also necessary so as to ensure safe operation of hydromain pumps. Disregard of these standards can lead to severe consequences such as equipment destruction, injury or even death.
Therefore, it is vital to select hydraulic main pumps which meet the industry’s codes as well as are properly installed maintained, used according to manufacturer’s instructions.
Comparison with Other Hydraulic Pump Types
There are numerous sorts of hydraulic pumps, for instance hydraulic main pumps. When choosing a pump, it is necessary to assess its appropriateness in answering the needs of the hydraulic system in question. This article will discuss how well hydraulic main pumps perform compared to other kinds of hydraulic pumps.
- Gear Pumps: Gear pumps are positive displacement type ones which use intermeshing gears to pump fluid. Normally this implies they aren’t as good as other types of hydraulic main pumps because their flow becomes unsteady and causes vibration and noise in a hydraulic system. Nevertheless, gear pumps have an uncomplicated design and are commonly not as expensive when compared with hydraulic main pump systems.
- Vane Pumps: Vane pumps are another type of positive displacement that rely on blades to push liquid forward. Conversely, these are more efficient than the gear ones but their flow can be pulsatile at times. However, they possess more complications regarding design unlike the gear ones and hence their cost might be on higher side.
- Piston Pumps: Piston pumps are positive displacement kind that make use of pistons to move fluid from one place to another. They operate at high efficiency but require large investments due to their complexity and costs. They find wide application where there is need for relatively higher pressures.
Hydraulic main pumps generally are more efficient than gear pumps and provide similar flow patterns, unlike vane units which may have higher power outputs or pistons that offer greater dynamic head difference. Thus choice depends on specific needs and requirements imposed by a particular hydro system design.
Conclusion
To make the system move, hydraulic systems require an appropriate amount of pressure that is supplied by the hydraulic main pumps. It is important to know the functions of each unit of a hydraulic main pump in order to effectively apply and maintain it.
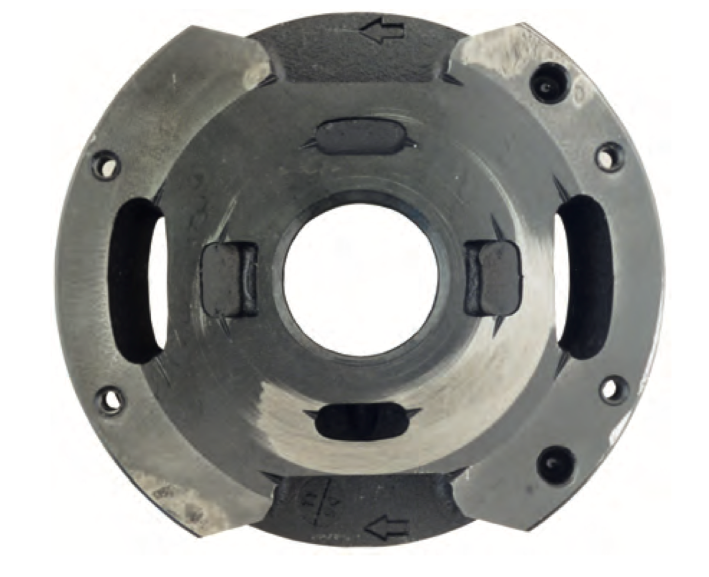
hydraulic main pump
For instance, such operations as checking if everything is alright, cleaning all parts and calibration are necessary and enable proper functioning of any system as well as eliminating any other mishaps that might have resulted into its destruction. Similarly, preventing downtime and avoiding breaking down the system can be done through solving normal problems like cavitation and even leakage.
The choice of a specific pump for a given application should depend on its suitability to the task at hand. The efficiency and performance attributes differ among various types but so do their disadvantages and advantages; thus it is imperative to select a perfect one.
Therefore, maintaining them appropriately when they break down or choosing another type for your application are some of the most important things you need to consider in order to get maximum performance from your hydraulic main pumps. If they follow this advice, people who own hydraulic systems can be sure that their equipment will remain highly efficient and dependable at all times.