June 21, 2024
Common Types of Hydraulic Pump Pressure Compensators and Their Applications
Hydraulic systems are used for a wide variety of applications in industry, ranging from construction equipment to aerospace. Understanding the functions of hydraulic pump pressure compensators is vital when it comes to ensuring that these systems operate safely and efficiently. To maintain system pressure and flow, these devices play a significant role and can be highly efficient.

hydraulic pump pressure compensator
The objective of this paper is to give an outline of hydraulic pump pressure compensators, their types, purposes as well as use. We shall look at the benefits and drawbacks of various types of hydraulic pump pressure compensators and give recommendations on how to choose the right one for specific applications.
Pressure compensator for hydraulic pumps always aim at keeping a constant pressure within a given hydraulic system regardless of altering a flow rate. It causes the safe and efficient operation within which hydraulic system should work and it may largely affect its performance including efficiency. By simply knowing the principles as well as functions behind these items; facilities will be able to properly select them accordingly into their hydraulic systems.
In subsequent sections, we shall discuss various types of hydraulic pump pressure compensators involving their operating principles, uses or advantages besides providing real examples where they have been applied successfully. Finally, we will sum up important details with emphasis on why proper selection and usage are aspects that industrial companies must bear in mind prior to implementing any manufacturing process using such pumps in question.
Understanding Hydraulic Pump Pressure Compensators
Pressure compensators in hydraulic pumps are apparatuses that maintain hydraulic system’s constant pressure by controlling fluid supply from the pump. They guarantee a safe and efficient performance within set limits while playing a big role in the maintenance of system performance and efficiency.
Some types of hydraulic pump pressure compensator are relief valves, flow control valves and pressure reducing valves. Each type of compensator has different advantages and disadvantages as well as operates on different principles.
Relief valves are examples of such hydraulic pump pressure compensator. To maintain a steady flow rate in the hydraulic system, they channel back superfluous fluids into the reservoir when the internal pressure gets beyond certain limit levels. It ensures safe operating ranges for pneumatic systems, thus preventing systems damage or equipment destruction.
Another classification is made up of Pressure Reducing Valves which are also classified under Hydraulic Pump Pressure Compensator. These devices ensure that the fluid coming from a pump always maintains its constant value of pressure. As a result it allows to operate safely and with optimum energy use as well as cost reduction purposes.
Flow Control Valves form another category of Hydraulic Pump Pressure Compensators; these maintain fixed rates of flow in hydraulic systems through regulation of fluid discharge from pumps. It makes sure that operational parameters remain optimal hence improving on efficiency besides general performance enhancement.
For instance, one should consider individual needs for application as well as advantages and disadvantages for each type when selecting appropriate Hydraulic Pump Pressure Compensator. Relief values can prevent damage within the system, though this may result in low efficiency due to energy loss. Although these can reduce power consumption, there is no guarantee that they will be able to keep up with uniformity throughout all applications of allowing outflow. Even if flow control values improves both performance and overall efficiency, their compatibility level with some applications remains unquestionable since they do not maintain uniform occurrence.
In conclusion, these components play significant roles in terms of maintaining good performance and efficiency of hydraulic systems. However, it is important for facilities to know the working principles as well as functions of different compensators so that they can use them in a right way.
Applications of Hydraulic Pump Pressure Compensators
Industries including construction, agriculture, mining, aerospace and manufacturing utilize hydraulic pump pressure compensators. They are important for the operations of the systems hence their effective use can significantly lead to cost savings in a company.
Different applications have different types of hydraulic pump pressure compensators with advantages and limitations. The lifting equipment and hydraulic presses in hydraulic systems often have relief valves because there is a high risk of overpressure. In injection molding and metal stamping where energy consumption and costs are main concerns, pressure reducing valves are mostly found. Flow control valves are used in machines like conveyor systems and machine tools that require maintaining constant flow rate.
It is vital to take various things into consideration when choosing a particular type of hydraulic pump pressure compensator for an individual application such as system pressure or flow requirements; energy consumption or cost among others; also how dangerous the system is liable to be damaged. These include improved performance and efficiency, lesser energy costs, longer equipment life among others.
Hydraulic pump pressure compensators have another advantage as mentioned before in which they maintain constant system pressures irrespective of changes in flow rate. This could entail better safety standards as it will reduce possible damages on the system due to under or over-pressurization. But care must be taken during their selection process so that there isn’t any case under or overpressure.
In general terms therefore, these pieces form important parts utilized by different industries within their hydraulics’ systems. By knowing what each kind does best or worst managers can better facilitate both safe operation and meaningful work done by such processes at their companies.
Proportional Pressure Compensators
Proportional pressure compensators, which are hydraulic pumps that adjust the pressure in a hydraulics system in proportion to current flow rates, are commonly used in systems that require highly precise control of pressure and flow rate such as aerospace and automotive applications.
The proportional pressure compensator operates by changing the flow of fluid from the pump in line with desirable level of pressure using a control signal like hydraulic or electric signals. This allows for precision control over both pressure and mass flow rates enabling enhanced system performance as well as efficiency in most cases.
One advantage of proportional pressure compensators is their quick response to variations in system demands. They have the capability to adjust the pressure and flow rate continuously thus maintaining safety limits within the working parameters.
Another classification for these compensators is based on direct-acting ones that do not need any pilot valve but instead use a direct-acting valve to change fluid flow from pump based on whether it should be increased or reduced. Pilot-operated types are those whose operation involves making use of a pilot valve facilitating better accuracy as well as regulation.
Aerospace and automobile industries highly employ this device because they depend on accurate management of pressures and flows. Industries involved in manufacturing and processing, would also implement them for enhancing efficiency, reducing wastage by managing pressures under strict limits.
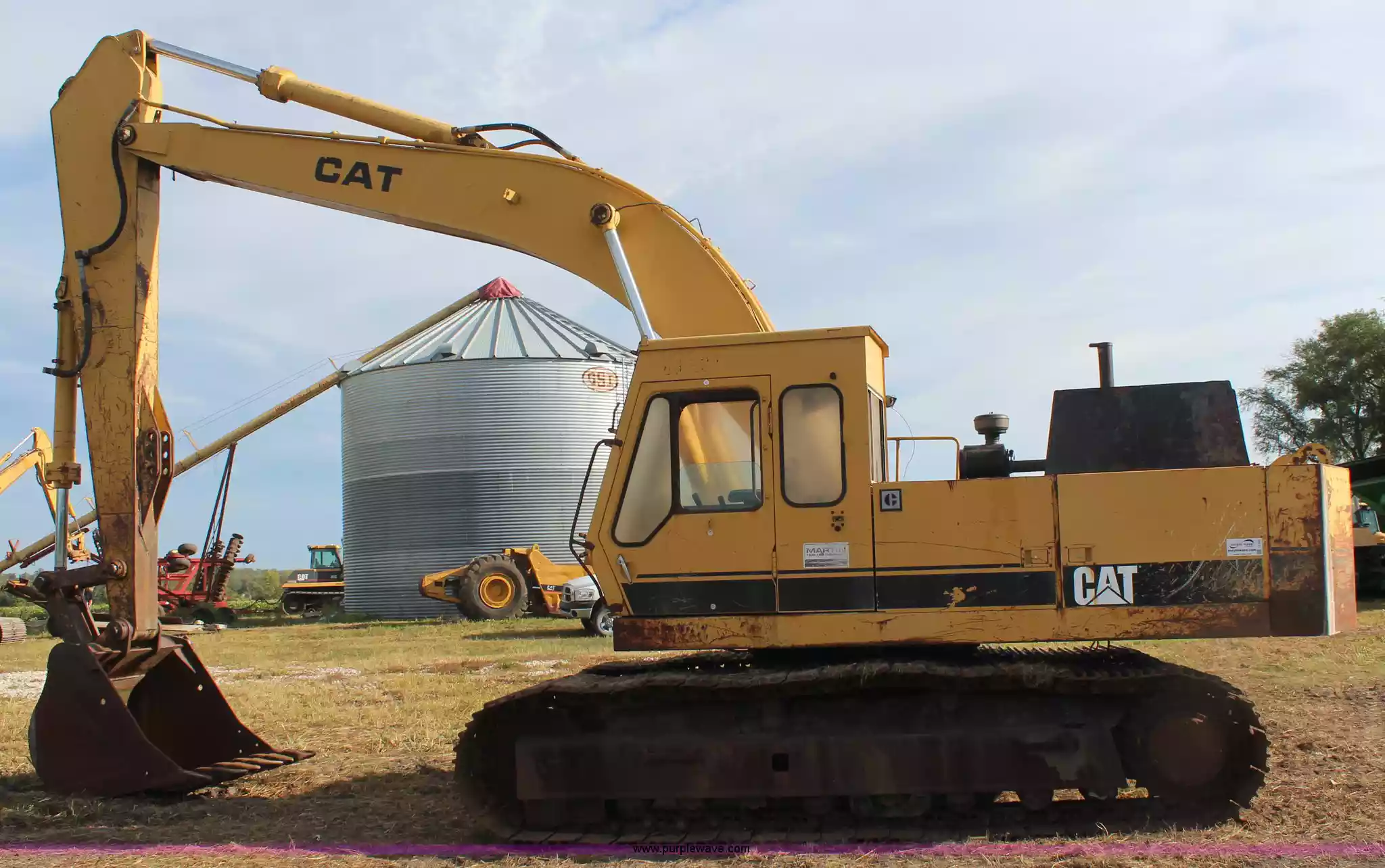
hydraulic pump pressure compensator
In summary, this paper has shown how proportional pressure compensators act as powerful tools for controlling hydraulic systems’ pressures while flowing liquids through them. In order to meet real time needs of systems, they offer precise controls hence improving system efficiency ,lowering costs leading to lesser energy consumption hence reducing costs incurred.
Load Sensing Pressure Compensators
Load sensing pressure compensators are one type of hydraulic pump pressure compensator that regulates the pressure in the hydraulic system depending on the load demand, a feature that makes them common in areas where loads vary such as construction equipment and material handling systems.
By sensing the load demand, load sensing pressure compensators adjust fluid pressure and flow rate from pump. This enables precise control of both flow rate and pressure hence improved performance and efficiency within the system.
One advantage of load sensing pressure compensators is their real-time response to changes in load demand. They can adjust the pressure and flow rate to serve the given load thus keeping it safe and efficient.
These load sensing compensators can be divided into open center and closed center types. The former uses an open center valve to direct fluid from a pump based on what is being hauled. Conversely, closed center models have a closed valve at their centers; hence higher level of accuracy when controlling movement of fluid from pump.
The use of such devices extends to constructions, material handling systems among others which experience variations in loading demands. Furthermore, they may be applied within manufacturing and processing plants where proper regulation of pressures or rates increases productivity while minimizing wastage.
In summary, there is no other more important device than this for controlling pressures along with rates in hydraulic systems with fluctuating loads. When demands change immediately like it happens here we need an exact response whereby these systems will help us save energy costs as well as increase efficiency thereby prolonging life expectancy of machines.
Pressure-Flow Compensators
Hydraulic pump pressure compensator is a type of pressure-flow compensators that controls how much fluid leaves the pump, as well as the amount of pressure. For instance it is commonly used in machine tools and injection moulding since they maintain a constant pressure and flow rate.
Through feedback loops, pressure-flow compensators can adjust the pressure and flow rate of fluid from the pump to meet system requirements. This feature enables one to have better control over flow rates and pressures; hence leading to an increased efficiency and performance of systems.
There are several advantages associated with using these types of pumps including constant high or low-pressure flow rates regardless of demand change. Safety will be enhanced as well as reduced risks in cases where there are system malfunctions.
Mechanical types are further divided into two namely mechanical and electrohydraulic.The mechanical types use mechanical feedback while adjusting the fluid flows between the hydraulic pumps.Using electrical signals to adjust fluid flows between hydraulic pumps makes electrohydraulic types more precise because they afford greater specificity for changing rates.
For example in applications such as machine tools, where maintaining a uniform pressure-flow is crucial, there has been a widespread utilization of pressure-flow compensators. This approach can also be utilized within manufacturing processes which need accurate control over fluids’ volumes and their pressures so that wastages could be minimized thus improving process efficiency.
A tool with great influence on controlling pressures and flows in hydraulics can be referred to as Pressure-Flow Compensators. They respond promptly to any changes within systems by making adjustments; this marks both improved functionality and efficiency, less power requirements, minimum costs incurred through energy spending as well as higher life cycle span for equipments.
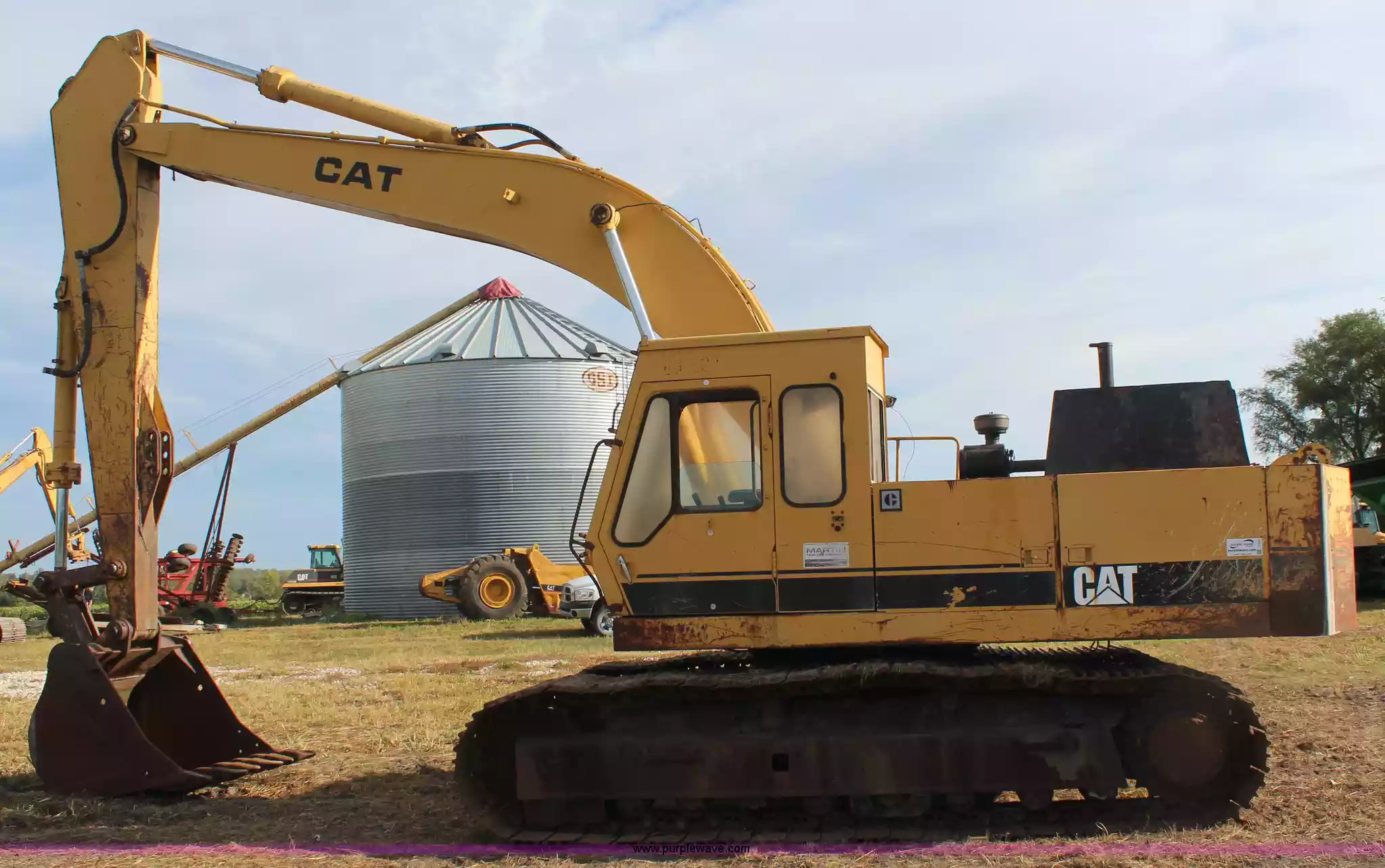
hydraulic pump pressure compensator
Case Studies
There are lots of instances where pressure compensators for hydraulic pumps in many industries have been successful. Below are a few case studies that demonstrate the importance of correct selection and use of hydraulic pump pressure compensators.
Case Study 1: Construction Equipment
An overpressure issue due to frequent hydraulic system failures on its excavators meant that a building company had to find solutions. Putting relief valves in their systems to regulate pressure led to less efficiency and energy wastage. After seeking advice from experts, these were replaced with load sensing pressure compensators. These load sensing pressure compensators regulated system’s constant pressure regardless of fluctuation in demand thus increasing efficiency and machines lifespan.
Case Study 2: Material Handling
A manufacturing plant was experiencing high energy consumption and costs within their material handling system. Underpressure and reduced performance were realized as they put flow control valves into the system to control flow rate. The flow control valves were subsequently replaced with proportional pressure compensators through consultation with a hydraulics expert. Proportional pressure compensators provided precise control over both the pressures as well as flow rates resulting in lower energy usage, reduced costs as well as better working systems.
Case Study 3: Injection Molding
Frequent overpressure-linked hydraulic system breakdowns occurred in the injection molding machines at a plastics manufacturing facility. They tried regulating fluid pressure by installing relief valves to no avail; this only caused significant loss of power across other parts of the machine’s operation. Professionals specialized in hydraulic machinery advised them on how to substitute these relief values with others known as press-flow compensators which maintained constant rate alongside streaming motion thereby making it efficient and longer lasting.
These case studies demonstrate why choosing the right hydraulic pump pressure compensator is important for different industries. By selecting proper applications for specific situations, putting good installation methods and ensuring that equipments are set up properly plants can improve efficiency, increase cost savings through reduced energy use and prolonged life spans of machinery used within their operations.
Conclusion
To sum up, hydraulic pump pressure compensators are a must-have in hydraulic systems across industries. They are essential for system performance and efficiency, and their correct use can greatly influence operational costs as well as productivity.
Various types of hydraulic pump pressure compensators have advantages and disadvantages in various applications. In high-risk hydraulic systems like lifting equipment and hydraulic presses, relief valves are commonly used to prevent overpressure. Pressure reducing valves are frequently employed in energy-intensive applications such as injection moulding and metal stamping. Flow control valves are necessary when maintaining constant flow rates is crucial, as with conveyer belts or machine tools.
Proportional pressure compensators allow precise control of pressure and flow rate in critical hydraulic systems like aerospace and automotive ones. Load sensing pressure compensators can efficiently control the change of both pressure and flow rate within hydraulic systems that experience varying load demands such as construction machinery as well as material handling systems. Pressure-flow compensators assist in controlling both the pressures as well as flow rates of fluids so that they can be maintained at constant values in machine tools.
By recognizing what each type of a hydraulic pump pressure compensator is good for (and not) along with applying it to many different situations, facilities could ensure the safety and efficient operation of their own hydraulics. Such practices may lead to better system performance & efficiency, decreased energy consumption & its cost implications plus longer lifespan for the machineries.
Finally, it should be noted that proper selection and usage of Hydraulic Pump Pressure Compensators is very important for industry activities. Facilities should adopt best practices in selecting and using these compensators while carrying out regular maintenance checks on them so that they continue functioning securely without any hitches at all times.