June 21, 2024
Achieving Optimal Efficiency with Proper Adjustment of Two-Stage Hydraulic Pumps
Two-stage hydraulic pumps are a type of two step hydraulic pump adaptation that is usually utilized in different kinds of hydraulic systems. They are programmed to ensure the system is under high pressure and flow rates while at the same time reducing the energy consumed. Hence, two stage hydraulic pumps were developed in order to increase the effectiveness and performance of hydraulic systems which will then result into lower costs of operation and enhanced productivity.
There are two main types of two-stage hydraulic pumps: gear pumps and vane pumps. Gear pumps normally handle high-pressure applications with low flow rates whereas vane pumps cater for low pressure with high flow rate applications. These types of pumps have their own characteristics as well as advantages thereby making them usable for different applications related to hydraulic systems.
Two-stage hydraulic pumps can be used in various types of hydraulic systems ranging from industrial machinery, mobile equipment through to agricultural machinery. Common applications include construction equipment, material handling devices, power generation plants etc.,
The following section will explain why proper adjustment of two-stage hydraulic pumps is significant for optimal efficiency and performance in system terms.

two stage hydraulic pump adjustment
Importance of Proper Adjustment
To achieve an optimum system efficacy and performance, it is important to properly adjust two-stage hydraulic pumps. Inefficient operation and reduced performance can result from a two stage hydraulic pump adjustment that is not properly adjusted which further leads to higher operating costs as well as lower productivity levels. Furthermore, such an improper adjustment may cause damage to system components or even pose potential safety hazards.
The pressure setting is one of the most significant factors that should be considered when adjusting a two stage hydraulic pump adjustment . This setting specifies the maximum pressure that the pump can deliver to the system. When the pressure setting is too low, thus making it difficult for the system to perform optimally, while a high pressure setting will spoil system components.
Another factor to consider is flow rate. This determines how much fluid can be delivered by the pump into the system. The flow rate being so low may mean that the system cannot perform its desired operations while excessive wear on parts of the system would result from flow rates that are too high.
Moreover, proper adjustment of two stage hydraulic pump adjustment entails ensuring that it operates with maximum efficiency. It involves adjusting displacement which regulates how much fluid each revolution of this machine delivers. Failure to properly adjust a pump’s displacement may lead to poor performance and inefficiency.
In addition, proper adjustment of two-stage hydraulic pumps comprises other considerations besides optimal pressure, flow rate and efficiency like viscosity of pumped fluid, size of hydraulic systems or load type applied on them.
All in all, proper adjustments need to be made on two stage hydraulic pumps if optimal efficiency and performance in a given system has got to be achieved. We shall look at steps for fine tuning these devices in greater detail in subsequent section.
Understanding Two-Stage Pump Adjustment
Based on the requirements of the hydraulic system, two-stage hydraulic pumps are intended to operate at varying pressure levels. Pressure settings and flow rates must be adjusted for the pump to match with what is required by the system.
When adjusting two stage hydraulic pumps, usually there are two primary steps involved: setting low-pressure relief valve and high-pressure relief valve. During the first stage, low-pressure relief valve regulates output pressure of the pump while during second stage it is done by high pressure relief valve.
Firstly, a two-stage hydraulic pump needs its low-pressure relief valve set. This will determine the highest amount of pressure that a pump can produce in its first stage. In determining this value several other factors such as load, efficiency within the system should be considered basing on minimum system’s pressure needs.
The next step after this adjustment is adjusting high-pressure relief value. The latter determines how much maximum force can be exerted by a pump as it works during its second phase. For instance, with consideration of load and whole efficiency of the system it should take into account maximum pressures needed in line with the systems’ needs.
Flow rate of a pump should also be regulated so that it corresponds to what is required by a given system apart from managing pressure settings. It may involve changing displacement of an adjustable pump or installing flow control valves in systems.
To appropriately adjust a two-stage hydraulic pump requires knowledge on both needs of hydraulic systems and capability of the pumps themselves. Safety and efficiency issues should take precedence when making adjustments therefore manufacturers’ specifications and recommendations ought to be looked up for guidance.
Testing and Validation
After the pump has been properly adjusted in two stages, it is essential to evaluate its performance by testing and validating it in order to make sure that it is performing at its level best. The test and validation steps include verifying that the pump is supplying the required flow rate as well as pressure output under various load conditions. In this case, a flow meter and a pressure gauge are used to detect changes in the hydraulic system and determine the pump’s efficiency.
In close monitoring of the system during tests carried out, you must see to it as an engineer or technologist that the manufactures recommended parameters for pumps operations have not been altered. If these parameters are not adhered to during operation periods, then there could be trouble with associated problems on hydraulic pumps or other components. In instances where there are faults observed during examination stage, it is necessary for corrective measures to be taken right way so as to avoid any damage being caused on either pumps or other machines.
The procedures employed in validation ensure that the pump operates within specified ranges of flow rates and pressure outputs established by manufacturers of this product. The comparison between measured flow rate and pressure output with those recommended by manufacturers is one of ways through which this can be done. If such values fall within acceptable limits, then we validate our findings thus making pumps ready for use.
It should be noted that testing and validation should be done regularly even after installation process has been completed. Regular testing and validation will help identify any changes or abnormalities that may have occurred over time while maintaining efficient running of a pump throughout its entire useful life span. It also helps prevent system failures thereby avoiding downtime since maintenance costs due to damages can also go up significantly.
Troubleshooting and Maintenance
Regular maintenance is necessary for optimal performance of two-stage hydraulic pumps. It is important to replace worn out seals, valves, and pistons in the pump’s components with time because of wear and tear. To avoid these problems, the pump must be maintained properly.
Leakage remains a common problem with two-stage hydraulic pumps. Leaks can happen when seals become worn out or damaged, there are loose fittings or components that are damaged. You need to act immediately if you find fluid on the ground or if there is little fluid in the reservoir.
There are also other frequent problems that may occur with two-stage hydraulic pumps such as overheating. This could result from factors like insufficient levels of fluids in them, blocked filters, clogged filters or malfunctioning pressure relief valves among others. For this reason, it would be wise to check whether fluid levels are proper, clean the filter once in a while for a replacement when damaged and ensure that pressure relief valve functions accordingly so as to reduce chances of heat.
The manufacturer’s recommended maintenance schedule and procedures should be followed so that you can have proper maintenance practices for your two-stage hydraulic pumps by inspecting, cleaning and lubricating the parts regularly. Maximum performance should always be ensured at all costs hence it advisable for everyone to use manufactures’ prescribed ways of service instead not doing so might cost one more than he/she would have used during initial purchase.
It is crucial to address any problems with your two-stage hydraulic pump right away. In order to identify where exactly things went wrong one may need to test certain features like pressure relief valve among others. Once it is known what caused the problem either repair or replace an affected part.
Apart from regular maintenance and troubleshooting measures; however; storage and transportation aspects should never be overlooked in relation to two stage Hydraulic Pumps. This process involves emptying the fluid contents within it after which its various components should then be cleaned up before packaging adequately against any possible damage during storage or transportation.
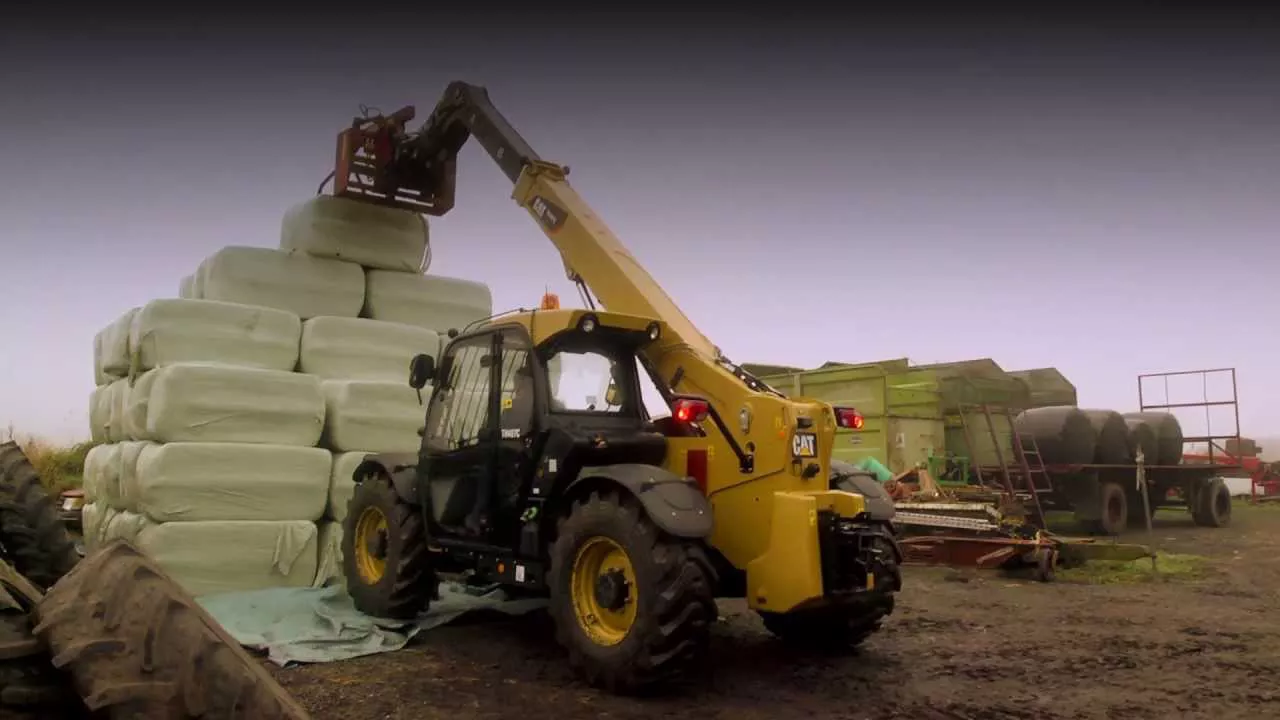
two stage hydraulic pump adjustment
By performing proper maintenance exercises coupled with troubleshooting techniques, Two stage hydraulic pumps can last many years without failure whilst maintaining efficiency consistently throughout their useful lifespan.
Industry Standards and Regulations
Effective adjustment of a two-stage hydraulic pump is vital not only for optimum performance and efficiency but also for the purpose of observing industry regulations and standards. Hydraulic systems are subjected to numerous controls and protection typically concerned with safety, reliability, and environmental responsibility. Therefore, operators should familiarize themselves with these requirements so as to make sure that their hydraulic systems meet them.
Amongst these are Occupational Safety and Health Administration (OSHA) regulations. OSHA expects employers to ensure safe and healthy working conditions including adhering to rules concerning hydraulic systems. These regulations include proper system design, installation, maintenance, operation etc.
Hydraulic systems also need to meet other industry standards besides those set by OSHA. Among the most widely recognized standards in this regard is ISO 4413:2010 Hydraulic fluid power — General rules and safety requirements for systems and their components. This standard sets out general design criteria as well as safety recommendations applicable to hydraulic systems comprising pumps valves hoses etc. Adherence to ISO 4413 means that such hydraulics are made or installed or maintained safely.
On the other hand, NFPA which stands for National Fire Protection Association, ASME which means American Society of Mechanical Engineers and SAE which represents Society of Automotive Engineers may also be among the many industry standards relevant in the field of hydraulics. They cover diverse issues like; system design, materials of construction installation/maintenance etc.
However it is essential to comply with the industry guidelines and laws in order to maintain a secure functioning hydraulic system. During operations it is important therefore that personnel have adequate knowledge about relevant statutes/rules/regulation regarding designing/ installing / maintaining hydraulic systems according to prevailing codes/. Breaching such principles can lead up; not just endangering lives at stake but may ultimately result into faulty operation or even litigation.
Comparison with Other Hydraulic Pump Types
There are various types of hydraulic pumps apart from the two-stage hydraulic pumps that are used in different applications in a hydraulic system. The other types include vane and piston pumps, as well as gear pumps. We will compare these other types of hydraulic pumps to two-stage hydraulic pumps based on performance and efficiency.
Gear pumps are among the most popular type of hydraulic pumps. This is done by creating a vacuum which sucks fluid into the pump using gears’ rotation; when gears interlock, they pressurize fluid hence pushing it out of the pump. Gear pumping mechanism is characterized by simplicity, low cost and reliability but they are not efficient at high pressure conditions and can be very noisy.
However, on the other hand, vane pump, use a rotating vane which slides in and out of a rotor for creating vacuum and pressure respectively. At higher pressures they function better than gear pumps although more expensive than them due to their short life span.
The functioning principle behind piston pumps is reciprocating pistons that draw in and pressurize fluid. They are a kind of machine known for being highly effective with ability to produce high pressures acting against large flows while still being expensive machines demanding strict manufacturing standards.
Two-stage hydraulic pumps strike a balance between efficiency, cost and performance better than any other type of hydraulic pump discussed here. While they last longer compared to vane ones their efficiency at high pressures exceeds that of gear ones though it might not be as good as in piston ones; however making them simpler to manufacture/maintain and cheaper.
Ultimately, the decision on the type of hydraulic pump to choose depends on the specific requirements or needs of your system. Two stage hydraulic pump would be appropriate for many applications but should not be chosen before considering all options available.
Conclusion
Summing up, two-step hydraulic pumps are an essential aspect in many hydraulic systems and proper adjustment is critical to obtaining the best operating and performance. Understanding the purpose and function of two-stage pumps as well as the different types and their applications in hydraulic systems is necessary.
This means that care has to be taken when undertaking the process so that any mistakes might not occur which may lead to failure of the system. Additionally, testing along with validation procedures need to be followed for confirmation whether or not the pump was properly adjusted.
To avoid common issues with two-staged pumps maintenance practices have also been put in place. By this token, troubleshooting approaches will help in identification and resolution of any problems which may crop up. Furthermore, adherence to industry standards and regulations is important so as to ensure safety and dependability.
Comparison with other types of hydrologic machines reveals that there are limitations and advantages concerning efficiency together with performance for two-stage pump which should be considered when choosing a particular pump for use in a given application.
In conclusion, achieving optimal efficiency with two-stage hydraulic pumps requires proper adjustment, testing, and maintenance procedures, as well as compliance with industry standards and regulations. Higher levels of productivity within less time can be achieved if these guidelines are adhered by hydraulic systems leading to improved efficiency and high performance thereby minimizing downtimes.