June 21, 2024
Understanding the Different Types of Hydraulic Pumps: A Tutorial
Hydraulic pumps are necessary for many machines and systems in construction, agriculture, manufacturing and other industries. They generate hydraulic pressure required by the system to work properly. It is important to be familiar with different types of hydraulic pumps and how they function so that one can choose the best pump for a particular application which will lead to maximum performance.This guide highlights various kinds of hydraulic pumps, their operations, uses as well as their merits and demerits. Additionally, it also covers tips on what should be considered when selecting a hydraulic pump tutorial together with some routine maintenance practices or troubleshooting methods commonly employed. By the end of this tutorial, one will have a good understanding about hydraulic pump and its use in different areas.

hydraulic pump tutorial
A variety of gear pumps, vane pumps and piston pumps are available under hydraulics. Each type has got specific unique features which make them suitable for different tasks though all have their own advantages as well as disadvantages thus it depends with the kind of work being done or environment where they will be used . Therefore it is necessary that people should know more about these types while selecting the right one for any given purpose.
Moreover, this study session shall also look into why we need to know about Hydraulic Pumps in different applications. Hydraulic power units play an integral role across various sectors; thus choosing correct types can lead to better performance within systems resulting into cost savings and productivity gains too.
In conclusion this quick start guide gives information on how does hydraulic pump works? where do we use them? Understanding Hydraulics is very important because if not chosen correctly might result into poor working condition hence costing much money repairing later on but with proper knowledge one can avoid such mistakes altogether.If you want more details regarding these points kindly refer back here again otherwise thanks.
Gear Pumps
Gear pumps are among the most widely used hydraulic pump types. Positive displacement pumps, they create pressure by pushing liquid through the teeth of interlocking gears. Oppositely spinning gears trap fluid between their teeth and a pump casing as they rotate, creating flow that causes hydraulic pressure.
Application and Benefits of Gear Pumps:
Gear pumps usually find use in low-to-medium-pressure scenarios that involve moderate flow rates. These can include hydraulic power steering systems, machine tools, small construction equipment among other applications where this pump is common. People also love it for mobile applications due to its size and cost-effectiveness.
The straightforwardness of gear pumps’ design makes manufacture easy and maintenance cheap while remaining effective at what it does best – pumping fluids around! They can also self-prime themselves by sucking up liquids without any help from an outside source. Additionally these machines have relatively lower noise levels than other types thus becoming suitable for situations where silence matters most such as during sleep time hours at residential places or hospitals where patients need peace too.
Limitations And Disadvantages Of Gear Pumps:
However there are certain limitations that should be considered when using them; for example since these types work with internal leakage energies could be dissipated at high rates hence making them unsuitable for applications requiring high pressures. Also if you want to handle fluids with particles which could cause damage on gear teeth then it would not work well either because abrasive particles might exist within those materials being moved by gears themselves . It should also be noted that over time wear will occur due to its design thereby leading to decreased performance together with efficiency while another thing is about limits in terms of matching flow rates depending on specific system requirements.
In conclusion, knowing advantages as well disadvantages concerning gear pumps becomes necessary during selection process for an appropriate pump needed in particular application context.
Gear Pumps
The most popular of all hydraulic pumps is the gear pump. These are positive displacement pumps that create hydraulic pressure by pushing fluid through the teeth of meshing gears. The teeth of the gears trap fluid between them and the casing of the pump, which results in a pumping action that creates hydraulic pressure as they rotate in opposite directions.
Uses and Benefits of Gear Pumps:
Gear pumps are frequently employed in cases requiring small to medium flow rates at low pressures; such as power steering systems for machines, tools with built-in hydraulics, and light construction equipment. They are also convenient for mobile applications due to their size and price.
One main advantage is their simple design which allows for easy manufacturing as well as maintenance; another being that they are self-priming hence can draw liquid from a tank without any assistance other than themselves. Additionally, they produce relatively little noise making them suitable where silence matters during operation like hospitals or libraries.
Disadvantages/Limitations:
However there exist certain limitations inherent within gear pump technology thus rendering it inappropriate under specific circumstances. One such limitation may be attributed to its inability to function optimally at high pressures because of internal leakages occasioned by design considerations associated with this type of device.
Furthermore these gadgets cannot handle highly viscous fluids or those with particles that could wear off the teeth easily thereby leading to damage of same over time due to wearing out caused by continuous rubbing against each other during operation. They also have a limited range within which flow rates can vary making it difficult sometimes to match them precisely according system needs.
In conclusion, people choose gear pumps when dealing with tasks requiring modest levels of pressure and volume flow rate due to their simplicity, smallness alongside being cost-effective while having some demerits since they do not perform well where there is much pressure involved or handling high viscosity liquids containing abrasive materials Understanding both sides helps one select appropriate gear pump for any given situation.
Vane Pumps
Vane pumps are of the positive displacement hydraulic pump category. They create pressure in a fluid by confining them between the vanes and ring. The enclosed fluid is then ejected at high pressure as the vanes rotate.
Review on Vane Pumps and their Operation:
For sliding vane pumps, they have a cylindrical rotor incorporating slots that house vanes which can slide in or out. This rotor lies eccentrically within circular pump housing; hence creating an elliptical cavity between itself and casing while rotating around an axis perpendicular to it so that gravity acts along this line during operation . As these blades move through their corresponding apertures they always come into contact with walls thus forming small compartments which fill with liquid as the device rotates.
Applications and Benefits of Vane Pumps:
Medium pressure applications such as hydraulic power steering systems, lifts for cars or trucks among other industrial equipments represent some common fields where you can find vane type pumps being used frequently. One thing about them is that noise level produced by these machines is relatively low considering what they do but still enough loudness not to be ignored especially if one has been working near them all day long without wearing any hearing protectors . It should also be noted that these gadgets can operate continuously because there will always exist constant flow rate capability irrespective of time factors.
A major advantage associated with this kind of equipment lies on its ability to handle fluids having low viscosity up until medium viscosity ranges comfortably well without experiencing difficulties at all. Additionally another good thing concerning them is how they have been designed in such a manner that allows for wide variety flow rates while still maintaining capacity levels necessary under various situations involving pumping needs across different sectors both locally and internationally alike.
Drawbacks/Cons and Limitations/Applications not Suitable For Vane Pumps:
However there are certain areas where usage may not work best suited like areas requiring higher pressures because inner leakages tend occur due design flaws associated therewith . The other thing which might give problems over time wears out fast causing drop in efficiency hence leading to decreased performance levels achieved initially . Again fluids having high viscosities or particles containing abrasives could cause harm by destroying these blades as well as their casings too.

hydraulic pump tutorial
In conclusion, vane pumps find wide use in medium pressure applications and they can handle low viscosity fluids easily. Nevertheless, they have limitations that make them unsuitable for high pressure applications or those involving heavy duty jobs with thicker liquids containing abrasive materials.Understanding what vane pumps can do best helps one choose right pump for each specific case.
Piston Pumps
Piston pumps are hydraulic pumps that build hydraulic pressure by moving a piston back and forth within a cylinder. The movement of this component creates suction and discharging which gives birth to hydraulic pressure.
Outline of Piston Pumps and Their Functioning:
The main components of a piston pump include a cylinder, piston, inlet valve, and outlet valve. It works when the piston moves forward and backward in the cylinder during each cycle. This draws fluid into the pump on the suction stroke, then forces it out under pressure on the discharge stroke. During the suction stroke, the inlet valve opens so that liquid can enter into the cylinder while during the discharge stroke; this allows fluids to leave from it through an opened outlet valve.
Classification of Piston Pumps:
There are two types of piston pumps namely axial piston pumps and radial piston pumps. In axial type design pistons are arranged in circular pattern reciprocating parallel to axis while in radial type design they reciprocate perpendicular to axis with pistons distributed around.
Applications and Benefits of Use:
These devices find wide applications due to their ability to work at high pressures such as hydraulic presses for heavy machines used in construction industries among others. They can also create substantial flow rates because of the same reason hence being suitable for demanding tasks.
Efficiency is one thing that distinguishes piston pumps from other kinds; thus saving energy will be higher if applied where necessary leading further cuts down on operating expenses over time. Besides longevity being another advantage exhibited by these machines which can withstand exposure even when dealing with fluids having high viscosities or those containing particles likely to cause abrasion.
Demerits Associated With Piston Pumps:
However there exist certain disadvantages associated with them too like any other product would do depending upon its nature as well as purpose served therein. One such disadvantage may lie on cost factor; unfortunately enough sometimes people may find it costly especially if intended use does not require working under low pressure conditions neither does budget allow spending much money on such units.
Furthermore, over time wear might set in thus reducing efficiency levels besides overall performance as reciprocating action is prone to wear and tear. Also cavitation susceptibility poses serious threats since failure may occur due to pump damage caused by cavities formation along with other system components.
In conclusion, piston pumps operate best when applied in areas which demand high pressures and also have fluids that possess high viscosity as well as abrasive properties. Nevertheless they prove ineffective if subjected to low-pressure conditions or where financial resources are limited but this does not mean they cannot be utilized at all; every application needs careful consideration based on pros cons involved.
Other Types of Hydraulic Pumps
Another hydraulic pump, with unique characteristics as well as applications that are not so common is piston and gear pumps.
- Screw Pumps: These positive displacement pumps work by trapping a fluid between two rotors that have screw-like threads. They are used in situations where the flow rates must be high but the pressure should remain low to moderate.
- Peristaltic Pumps: This kind of positive displacement pump compresses a flexible tube by means of several rollers; this action generates hydraulic pressure for pumping. They are known for gentle fluid handling and can be found in pharmaceutical and food industries among others.
- Diaphragm Pumps: A flexible diaphragm is employed as part of its mechanism to create positive displacement or hydraulic head. These pumps may be used for handling abrasive or corrosive fluids, also they are great where high level contamination control is needed.
- Gerotor Pumps: These generate their power through the trapping of fluid between a rotor and stator which creates pressure differentials that move it along with some other parts such as gears. They have low-medium pressure requirements and find use in automotive industry among others.
Comparison against More Common Types:
Advantages, disadvantages – all types possess certain features best suited towards particular tasks while being less effective elsewhere; so understanding how each type operates will greatly help one choose.
In conclusion, even though vane pumps, piston pumps and gear pumps continue to dominate this industry; there exist other equally important varieties too. Knowing what works where saves time.
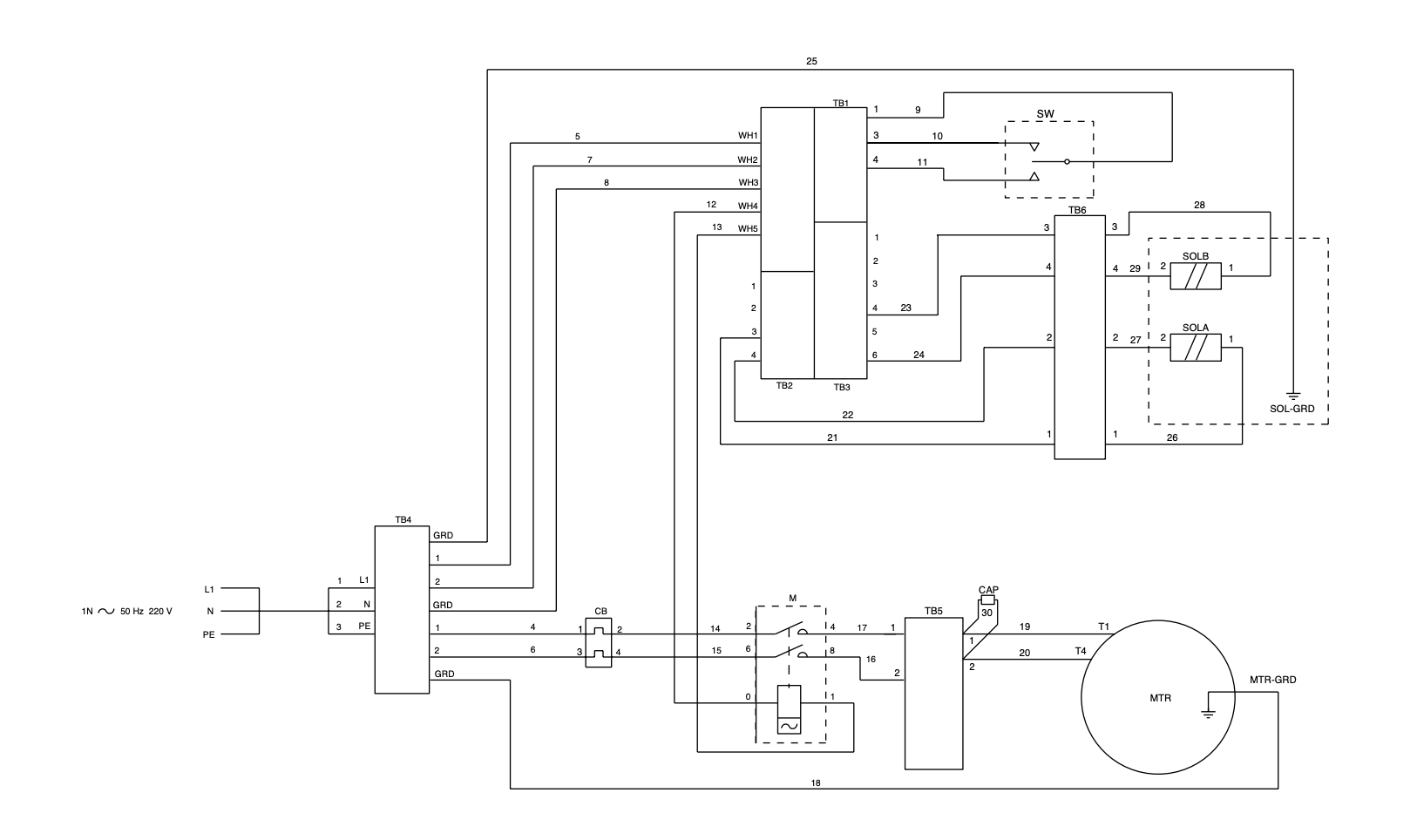
hydraulic pump tutorial
Factors to Consider When Selecting a Hydraulic Pump
There are many things that need to be considered when picking out a hydraulic pump for a particular application. These factors can impact the performance of pumps, their efficiency and whether they are suitable for use in an application.
- Properties of Fluid: Among other things such as viscosity or chemical composition, properties like temperature may affect how well a pump can generate hydraulic pressure as well as its lifespan. Therefore, it is vital to select those which are compatible with pumped fluids viscosities and temperature ranges required.
- Rate of Flow: The rate at which fluid flows through any given system will depend on what is needed by that system; thus one should choose pumps capable of meeting required flow rates. Also it’s necessary to take into account pressure drops due to friction along flow paths within systems.
- Pressure: Pressure requirements vary depending on applications ranging from low up high powers therefore while choosing a pump ensure that it does not wear too much or have internal leakages under the pressure being produced.
- Efficiency: Efficiency affects how long systems last and cost them. That is why selecting highly efficient pumps reduce maintenance expenses besides cutting down energy consumption levels.
- Size and Weight: This pertains to design considerations where space might be limited especially in mobile units; hence always go for lightweight compact designs during such instances since this saves both labour during installation processes together with money spent on buying larger – more expensive ones later
- Noise Level: Noise levels around working environments need consideration too– particularly those places requiring silence e.g., hospitals etc.. Thus always try finding pumps having lower noise levels than others for these types of worksites.
-
Costs: Some budgets may not accommodate all available options but going for cheaper alternatives might mean frequent breakdowns whereas expensive ones could squander funds without necessarily delivering better services. So choose wisely basing cost against performance among different brands/models available according individual needs/Tastes so far identified
Tips and guidelines for choosing the right hydraulic pump
- Seek advice from experts: This can be either done by consulting with individuals who work as system designers or manufacturers themselves since they possess vast knowledge regarding this field hence their suggestions might prove quite useful during decision making process towards finding suitable pumps needed in given applications.
- Think long-term: Another thing worth considering involves taking into account future requirements plus likely alterations which may occur over time so as not only look at present situation alone but also think about what will happen years down line thus ensuring selection of those pumps that remain relevant overtime.
- Buy from reputable sources: Always buy products manufactured reputable companies because such firms usually adhere strict standards while producing goods therefore clients assured getting reliable items capable fulfilling diverse needs appropriately under various conditions without experiencing any failures or breakdowns within short periods after purchase date hence reducing chances falling prey unscrupulous dealers selling fake counterfeit imitations posing great risk lives properties involved among others things associated with use these devices.
- Know the entire system: When looking for a specific type of equipment, it’s important to understand how different components work together. Therefore, when choosing a hydraulic pump, you need to know other parts like valves, reservoirs and actuators among others since failure do so might lead buying wrong item which cannot function properly within intended setup thereby wasting both time resources while compromising effectiveness overall performance achieved eventually leading dissatisfaction end user besides causing financial losses due incorrect investments made earlier thus limiting success potentiality achieving desired outcomes within shortest time possible.
In conclusion, there are many things that need consideration before settling on appropriate hydraulic pumps for particular tasks. The above mentioned factors include fluid properties such as viscosity and chemical composition, flow rate pressure efficiency size and weight noise level cost tips and guidelines
Maintenance and Troubleshooting of Hydraulic Pumps
To keep them efficient, effective and with long lives; hydraulic pumps have to be maintained well through proper repair and troubleshooting. Neglecting the repairs may cause the system not to perform optimally besides increasing operating costs or even complete breakdown of equipment. In this regard, I will discuss some maintenance procedures as well as problem solving techniques for hydraulics pumps.
Maintenance Practices:
- Regular Inspection: Carrying out regular inspections on both the pump itself and the entire system can help in early identification of potential problems before they become severe ones. Such checks should involve looking for leaks, checking on wearing parts or contaminants among others.
- Fluid Quality: The life span as well as efficiency of any given pump greatly depends on how clean its fluids are kept; thus maintaining appropriate fluid quality is paramount. This means that one must always check them up frequently by changing where necessary while ensuring that such liquids used match with material composition used in making these machines plus being specific about their applications too.
- Filter Maintenance: Filters should never be underrated because apart from playing significant roles like removing unwanted particles from systems; they also contribute greatly towards achieving desired results when it comes to flow rates etc. Therefore, it is very crucial for persons concerned about such matters to undertake regular filter servicing which involves cleaning then replacing worn-out ones so as not only ensure correct filtration but also promote better performance throughout hydraulic systems.
- Lubrication: Lubricating oils are known for reducing friction between moving parts thereby enhancing efficiency levels within a given setup e.g., pump assembly line etc.; hence why greasing should be done properly if at all we want our pumps run smoothly without any hitches along way caused by wear or tear related issues. It follows therefore that right types of lubricants must always be utilized together with frequency amounts recommended by manufacturers during each instance stipulated by them.
Troubleshooting Methods:
- Leakage: This occurs when there is failure sealing off various joints around seals resulting into some fluid escaping out thereby causing poor performance within affected sections e.g., piston not moving as expected etc.; therefore it becomes necessary to find out where exactly such leaks are originating from followed by rectification measures towards maintaining desired levels of efficiency for hydraulic pumps.
- Excessive Noise: Unusual sounds produced by machines during their operation could indicate that certain parts have become worn out due continuous rubbing against each other thus calling for replacement otherwise further damages might occur leading complete breakdowns later on if action is not taken immediately. Therefore, all sources noise need be identified then necessary adjustments made order prevent additional faults while still keeping good working condition machines involved.
- Loss Pressure: Several factors can contribute this problem including internal leakages contamination among others however main cause usually lies with worn components like seals or gaskets; therefore it would be advisable check those areas first before thinking about anything else because failure do so may result into more serious difficulties being experienced later on when least expected. Consequently, once we discover what part has been damaged or worn out should replace them accordingly until everything returns normalcy again concerning pumping systems.
-
Overheating: There are many reasons why overheating occurs in hydraulics such as low levels fluids inadequate cooling measures being taken place lack proper ventilation due high pressure environments among others thus one needs take extra caution while dealing with these issues since failure could lead total system break down. Therefore, if at all possible try find out exact cause overheat then fix problem as soon possible otherwise things might go wrong beyond repairs; especially knowing very well that pumps cannot withstand excessive temperatures for long periods without getting damaged permanently .
Importance of Proper Maintenance:
To maintain efficiency, performance and life of hydraulic pumps, one must ensure proper maintenance. If care is not taken with this step; there could be an increase in operating costs, reduced system performance as well as failure of the equipment itself. For these reasons regular inspection should be carried out alongside fluid quality control measures such as filter changes and lubrication points among others that can help promote good pump performance for long periods too.
Therefore, correct troubleshooting on hydraulic machines is important because it ensures their effectiveness throughout service life by identifying areas where attention is needed so that they function optimally all times without any problem occurring at them whatsoever. It also involves detecting common faults like leaks or overheating which may lead to loss of pressure while causing much noise in the process.
Conclusion
Choosing the right pump and keeping it efficient, powerful and long-lasting depends on understanding hydraulic pumps. Each of these, namely gear pumps, vane pumps and piston pumps have their own features as well as advantages and disadvantages among other types such as screw pumps, peristaltic pumps, diaphragm pumps or gerotor pumps which may also be used in some specific cases.
Some of the things that should be taken into account when choosing a hydraulic pump are fluid properties; flow rate; pressure; efficiency; size/weight ratio; noise level and cost. The following are tips for selecting the right pump that can help ensure success with this system. And so too must we troubleshoot them correctly if they’re going to work properly – this means undertaking regular checks on things like filters’ condition or lubricant levels but also monitoring how often inspections occur alongside maintaining good quality fluids throughout.
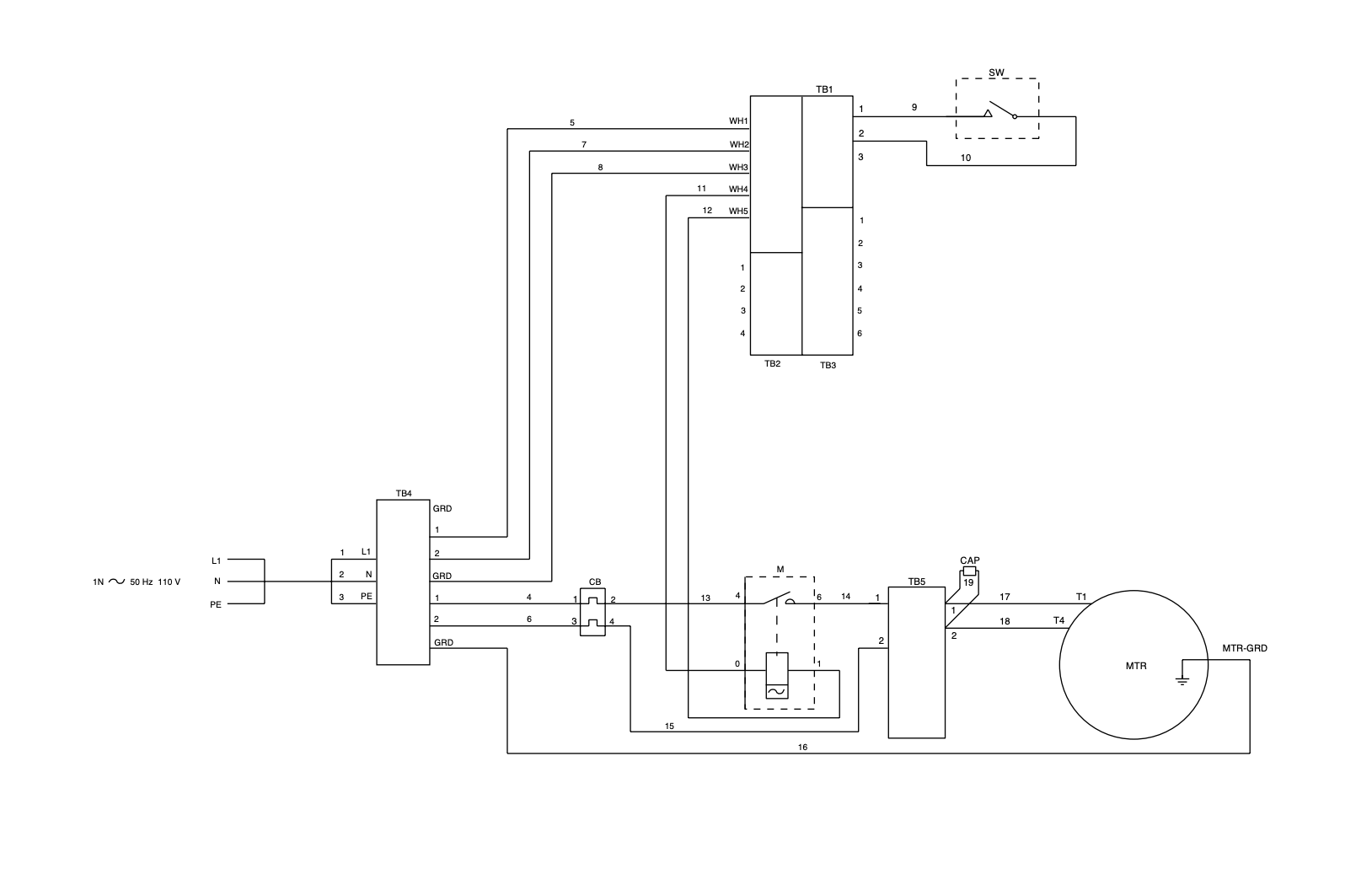
hydraulic pump tutorial
To summarize one’s knowledge about different types of hydraulic machines along with what factors need considering during their selection process and methods used for maintaining them in good working order is paramount when striving towards success within any given setup involving hydraulics . It’s all about finding the best match between a machine’s capabilities (strength) and what needs doing (workload). Good practice will lead us towards higher efficiency which ultimately leads us closer to cheaper running costs while at the same time increasing overall performance thus making sure everything works out fine over time so don’t forget about those three important steps – choose wisely, look after well and fix quickly!