June 21, 2024
Understanding Hydraulic Pumps: How They Work and Their Applications
How does a hydraulic pump work? In heavy machinery, construction devices, and airplane mechanisms among other applications, hydraulic pumps are elemental. They convert mechanical power into hydraulic energy resulting in the flow of fluid and pressure that then drives cylinders, motors and other forms of hydraulic actuators.
The reason for knowing about different hydraulic systems’ pumps is to allow one select the right pump for a particular system thus ensuring that it performs optimally while preventing any potential damage or hazards associated with this system.
Hydraulic pumps accomplish this by converting mechanical power such as from an electric motor, internal combustion engine or hydraulic motor into pressurized fluid stored in the form of hydraulic energy. The latter is used to drive various types of hydraulic actuators like cylinders, motors or valves which generate mechanical work.
Applications where these pumps find use include construction, mining, agriculture, aviation and manufacturing. These are frequently employed in powering linear motion through hydraulic cylinders and rotary motion through hydro-motors. Moreover, they come in handy when performing steering functions in vehicles particularly with regard to automobiles using the power steering systems as well as those having either hydraulic clutches or brakes.
To ensure efficient operation as well as safety of a system at risk from destructive forces due to improper selection considerations must be made on how water pumps function.
Basic Principles of Hydraulic Pump Operation
Hydraulic pumps, based on fluid mechanics and Bernoulli principle that the increase in the speed of a fluid corresponds to a decrease in its pressure, form the basis for their operation. This principle is used in generating fluid flow and pressure in a pump.
The impeller or rotor is responsible for generating fluid flow while the housing or casing contains and directs it. The impeller’s usually composed of rotating blades (or vanes) within a casing that create high as well as low-pressure regions inside the liquid.
Rotating impellers generate centrifugal force which pushes fluids into low-pressure zone at center of an impeller. When the liquid goes from high pressure intake side to low pressure outlet side, it passes through these vanes which causes acceleration and consequently leads to creation of fluid pressures hence are commonly called runners. Therefore, this casing indicates how pressurized fluids get distributed out from it towards preferred outlets where they can drive hydraulic actuators.
Size of pump, design of impeller and rotational speed determine its desired flow rate and specific pressure created. Flow rate and pressure produced by pumps must meet requirements by hydraulic actuators such as cylinders or motors in them for proper functioning.
Thus, understanding basic principles underpinned by hydraulic pump operations including Bernoulli’s principle and components associated with any hydraulic pumps such as one has could be instrumental in selecting suitable pump for particular purpose, attaining optimum performance out of such pumps plus realizing related safety aspects capable of damaging the system.
Types of Hydraulic Pumps
Three primary types of hydraulic pumps exist: gear pumps, vane pumps, and piston pumps. Understanding these differences is thereby important because each type has its own advantages, disadvantages and applications.
- Gear Pumps: Gear pumps are the most straightforward and most widely used kind of hydraulic pumps. They comprise two gears that mesh together with fluid being enclosed in between them and the pump housing. Vacuum is thus created by the rotating gears on their inlet side drawing in fluid while creating positive pressure on their outlet side pumping out fluid. Gear pumps are relatively cheap to buy, easy to maintain and can run at high speeds that make them suitable for low-pressure applications such as lubrication and cooling systems.
- Vane Pumps: Vane pumps have a rotor with vanes that slide in and out of slots in it. When the rotor turns, a positive pressure is created on the outlet side by trapping fluids between the rotor and pump casing through sliding motion of vanes. Vane pumps offer better efficiencies than gear ones and run at higher pressures which makes them good for medium-pressure uses like power steering or braking systems.
- Piston Pumps: Positive pressure is produced by piston or plunger moving back-and-forth within cylinder in case of Piston Pumps. Piston operated devices usually function at very high pressures hence they are commonly used on high-pressure machines including hydraulic presses as well as heavy duty machinery. Two main classes of piston pumps exist namely axial piston ones where pistons move parallel to pump shaft axially and radial piston ones where pistons move radially toward pump shaft.
The types of hydraulic pumps mentioned above include peristaltic screw diaphragm among others which are not common among people. These other kinds of hydraulic pumps do not find wide application except in specialized sectors such as chemical processing or food production.
To select an efficient pump system, avoid dangerous situations or damage to your system you must understand how different hydraulic types work, what they do best, their advantages and when to avoid them.
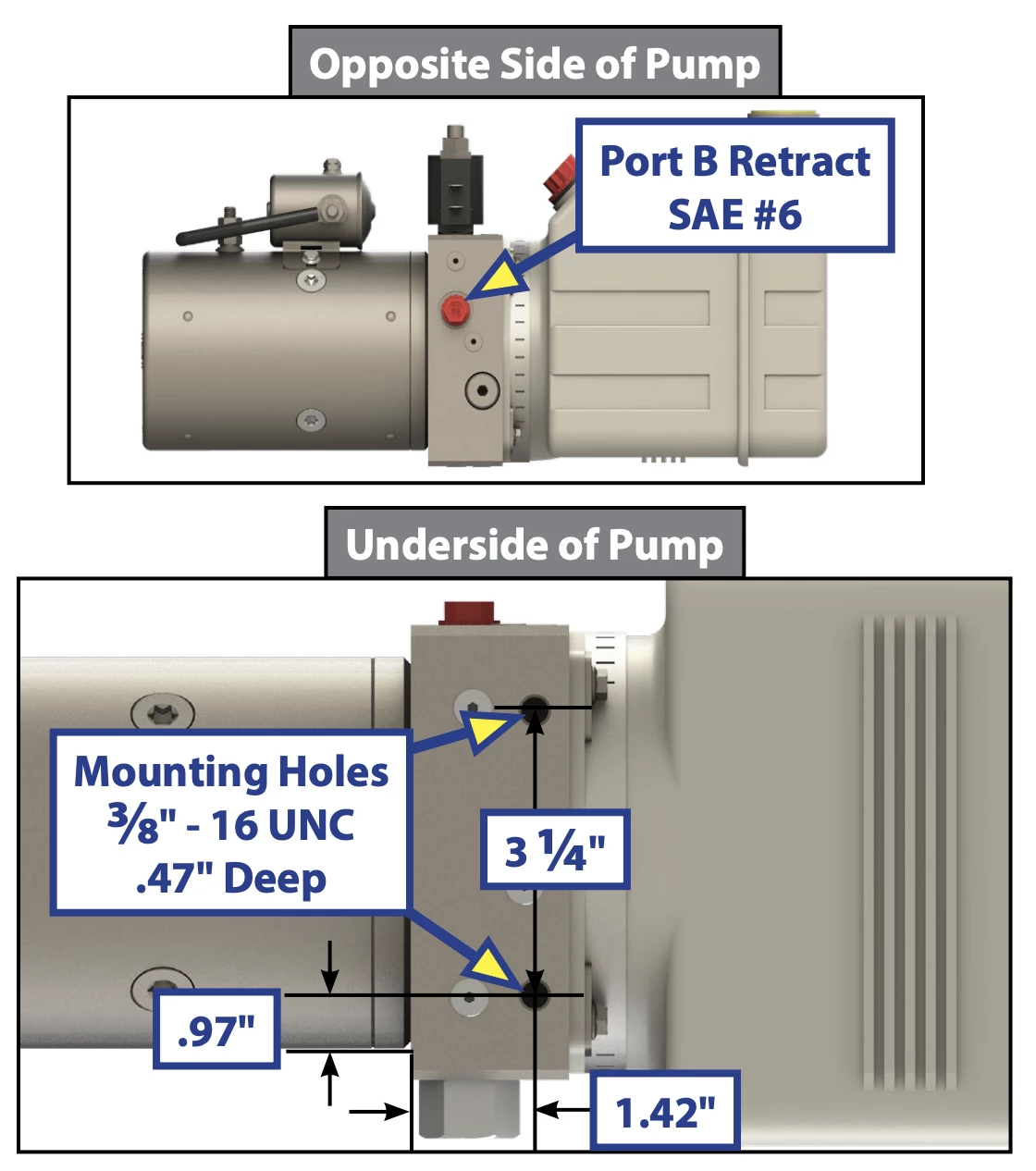
hydraulic pump how it works
Factors Affecting Hydraulic Pump Performance
Factors that can influence the performance of a hydraulic pump are several:
- Flow rate: Flow rate or the volume of fluid per unit time passing through the pump is a key factor in determining hydraulic pump performance. The flow rate should be adequate to meet system requirements and not above the capability of the pump causing cavitation or overheating.
- Pressure: Hydraulic pumps should be able to move fluid in the system by generating enough pressure against resistance exerted by loads. Pressure is typically measured in pounds per square inch (psi) or bar, and pressure ratings differ depending on models of pumps.
- Viscosity: Pump performance is affected by the viscosity of pumped fluids as it increase resistance whilst reducing flow rate. Pumps are manufactured to handle different viscosity ranges hence choosing the right one for a given liquid is fundamental.
- Temperature: If fluid temperature exceeds its range, hydraulic pumps can overheat. High temperatures also promote breakdown of fluids leading to component wear and subsequent failure of systems.
- Efficiency: Efficiency of a hydraulic pump represents output power divided by input power which determines how well it functions within an entire system. A more efficient pump will require less power input lowering operating costs with positive environmental implications.
- Pump size: When dealing with an application, selection of a proper size for a particular type of pump plays a vital role in optimizing its performance. An undersized pump may fail to deliver at desired flow rates or pressures while an oversized one might needlessly consume energy thereby complicating systems.
For choosing appropriate types, ensuring best possible operation and preventing any damages or danger reason, people must recognize these factors which affects to hydraulic pump performance exactly
Maintenance and Troubleshooting of Hydraulic Pumps
Maintenance and troubleshooting of hydraulic pumps are significant in order to achieve best performance and durability of the system. Some common maintenance practices and troubleshooting techniques are described below.
- Regular maintenance: The first step is regular maintenance, without it any other action will be wasteful. This comprises checking fluid levels, changing filters, inspecting hoses and connections and testing pump performance.
- Fluid contamination control: Also contaminants present in the hydraulic fluid can cause damage to pumps and other components of a system that may result in its failure. These can be dirt, water or metal particles among others that find their way into the system. Pump failure is avoided by managing fluid contamination.
- Seal replacement: Seals are critical parts of hydraulic pumps as their breakdown leads to leakage and reduced performance. Regular seal inspection as well as replacement is essential for sustained pump performance hence prevention of system damage results from this.
- Troubleshooting: When a hydraulic pump malfunctions, it becomes necessary for one to troubleshoot so as to establish the root cause of the problem and consequently select an appropriate solution. Common problems include low flow rate, low pressure, overheating, noise etc. Visual inspection pressure/flow test component replacement could be employed during troubleshooting exercise.
- Repair and replacement: In case a hydraulic pump gets damaged beyond repair then there should be need for its replacement so that normal function can resume within the system again. Replacement pumps must however be selected with care such that they are compatible with the system while at the same time ensuring adequate performance is achieved.
Proper maintenance and troubleshooting of hydraulic pumps can help extend their lifespan and prevent costly downtime and repairs.It’s important to follow manufacturer instructions or guidelines together with seeking professional help when necessary.
Applications of Hydraulic Pumps
Hydraulic pumps are used widely in various industrial applications. Here are several instances of their use:
- Construction: In construction, hydraulic pumps are commonly utilized to power up hydraulic cylinders and motors for machinery such as excavators, backhoes, and cranes. Hydraulic pumps have high efficiency and power, which is ideal for heavy-duty tasks.
- Agriculture: Hydraulic pumps are also employed in farming machines like tractors and combines to provide force needed in the operation of hydraulically controlled implements/attachments. For instance, high pressure is required for efficient operations.
- Manufacturing: To provide the necessary force and motion, hydraulic pumps are used during manufacturing processes such as stamping, bending, pressing etcetera. Machines therefore become able to move using hydraulic cylinders and motors.
- Mining: Hydraulic pumps also drive drilling rigs and excavators among other mining equipment that utilize hydraulic motors & cylinders. This makes it possible for them to be used under harsh mining conditions since they have higher efficiency together with power.
- Automotive: For example, hydraulic pump systems supply necessary pressure into automotive components like the brake or steering systems. Therefore, these systems will respond precisely when you apply brakes making your car more secure and performance better.
- Aerospace: Aircraft landing gear among other mechanisms rely upon hydrostatic pressure facilitated by the application of hydraulic fluids pumped by a system that utilizes a centrifugal pump because of its reliability as well as high power available with this type of pump which is propelled by a turbine.
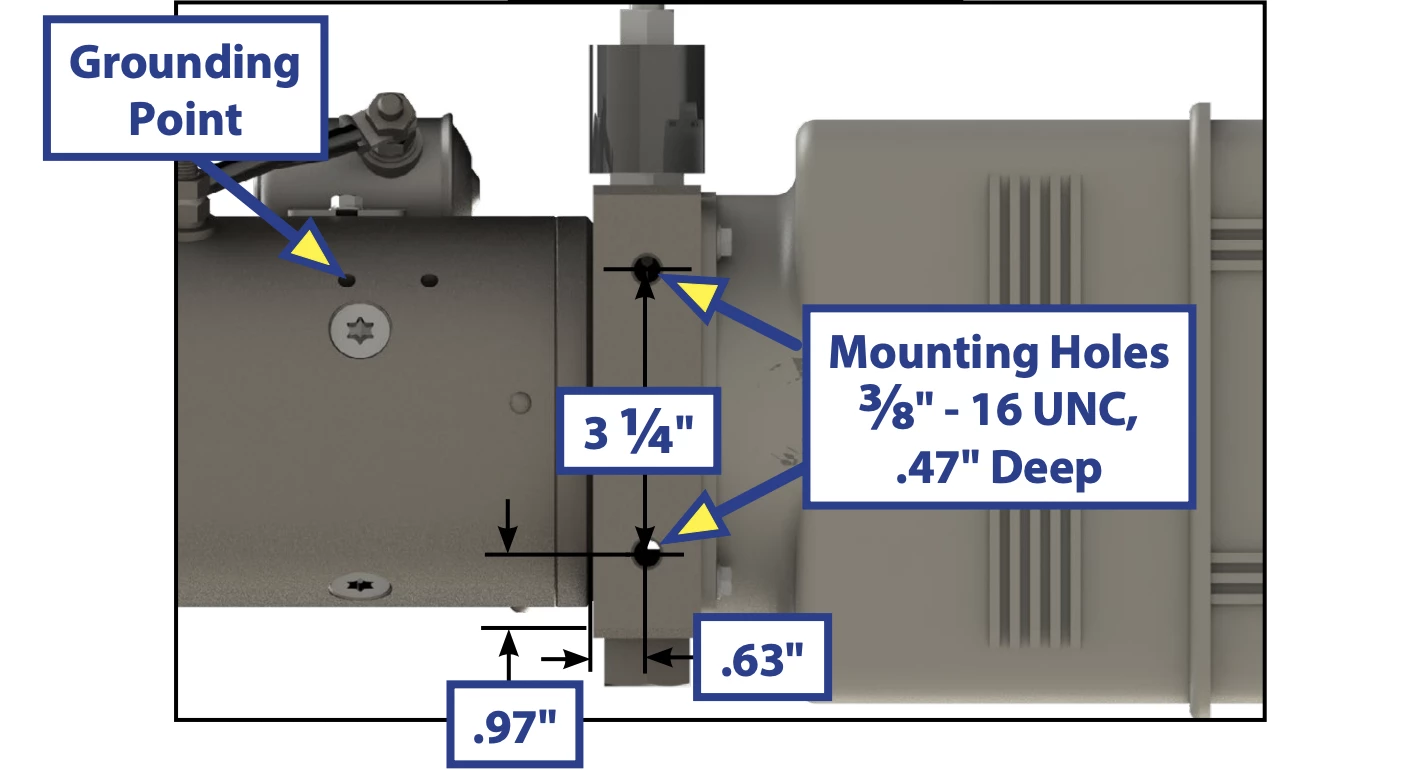
hydraulic pump how it works
Hydraulic pump’s versatility allows it to be used in many different applications that require high power with efficiency. Hence, one is expected to choose the appropriate type of a pump during purchase while proper maintenance troubleshooting procedures must be adhered to guarantee better performances over long periods of time for all reasons mentioned above.
Frequently Asked Questions (FAQs) About Hydraulic Pumps
- What is a hydraulic pump? A hydraulic pump is a mechanical gizmo that converts mechanical forces into flowing energy and pressure so as to power a machine.
- What are the different types of hydraulic pumps? Hydraulic pumps come in three categories: gear, vane, and piston. Each type has its own strengths and weaknesses and suits various applications depending on their needs.
- How do I select the right hydraulic pump for my application? Factors to take into account when selecting a hydraulic pump include flow rate, pressure, viscosity, temperature, and compatibility with hydraulic fluid. It is necessary to consult an expert in this field to make sure that the right selection is made.
- How do I maintain my hydraulic pump? To keep your hydraulic pump working properly you need to ensure it has enough fluid, inspect components for damages or wear and tear as well as clean and replace filters. Regular maintenance is key to optimum performance and long life of the device. What are common issues with hydraulic pumps?
- Hydraulic pumps often have such problems as fluid leakage, low pressure generation; poor performance along with excessive noise or vibration. Proper troubleshooting methods plus maintenance techniques can help solve these issues.
- Can hydraulic pumps be repaired? If the extent of damage done on them is not so severe like in other cases then they can be repaired unlike what most people think. This nevertheless calls for professional advice from an expert on what next step should be taken once one experiences such problems.
- How often should I replace my hydraulic pump? The life span of any given machine will be determined by how it’s used, maintained or even operational conditions among others. There are certain things which one must know regarding his/her particular kind of motor so that he/she gets good results out of it before replacing.
-
Where can I find more information about Hydraulic Pumps? Some useful resources where further information about Hydraulic Pumps can be obtained include industry publications; manufacturers dealing with these devices; along with experts or consultants on such pumps.
Conclusion
In conclusion, hydraulic pumps are important parts of hydraulic systems used in different industries for a variety of purposes. To select the most suitable hydraulic pump for particular application, to keep its working efficiency at the optimal level and be capable of solving any problem that occurs; one must understand how it works, its categories and factors that influence its effectiveness.
Regular maintenance and troubleshooting are essential in ensuring long lasting use and optimum performance of hydraulic pumps. It is necessary to involve an expert on hydraulic pumps in order to choose, maintain and trouble shoot effectively.
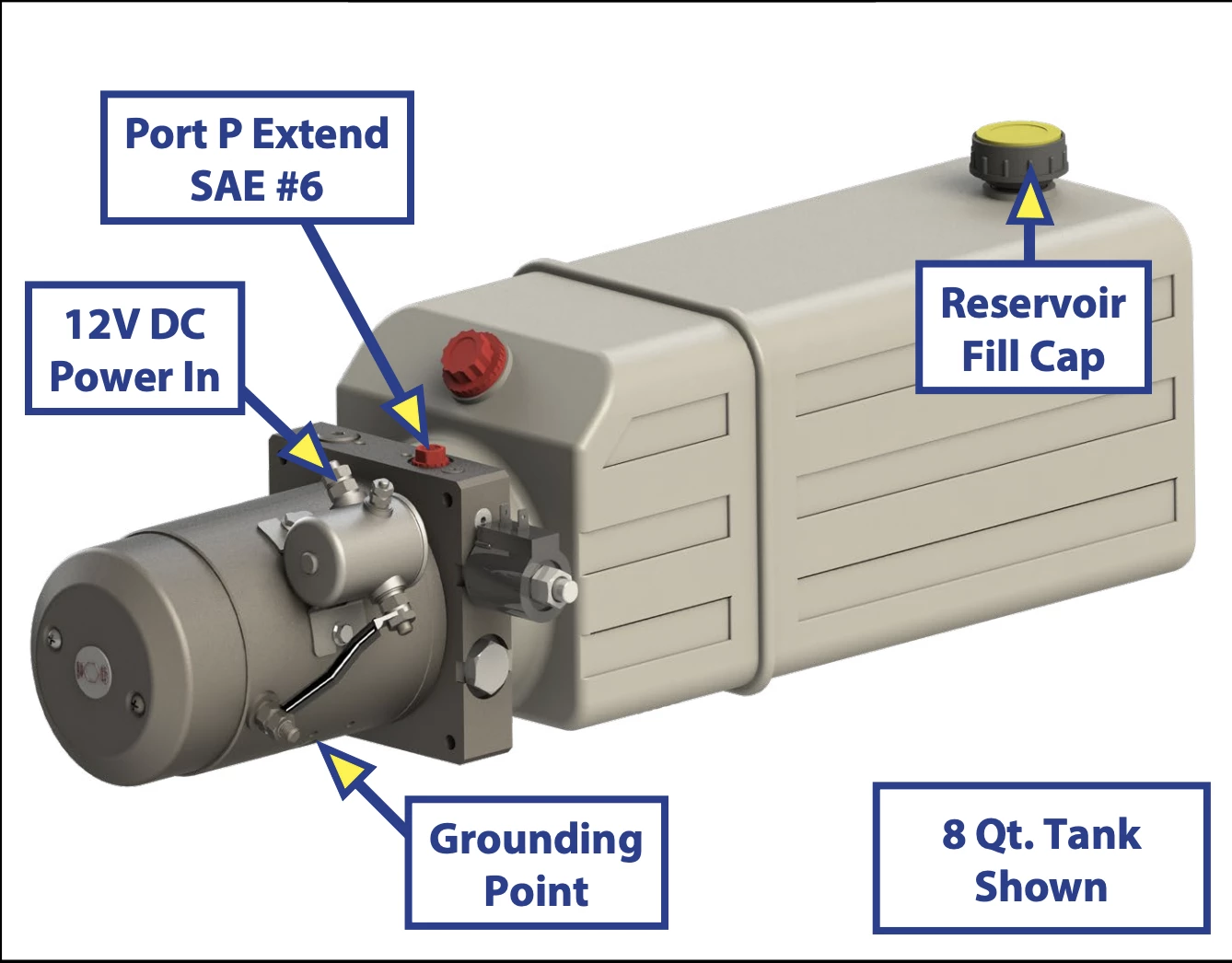
hydraulic pump how it works
By adhering to correct procedures regarding selection, maintaining, or troubleshooting a hydraulic pump, companies can reduce costs incurred as well as boost productivity thereby avoiding expensive downtimes. The prosperity of many businesses depends on their capability to gain access to excellent condition and operating well system of pumping fluid which necessitates awareness regarding this subject as well as proper care for these tools.