June 21, 2024
Upgrading Your Hydraulic System to Achieve Higher Pump Pressure
How to increase pump pressure ? Hydraulic system pump pressure is an important parameter in hydraulic systems. Pump pressure refers to the force produced by a hydraulic pump that is needed to drive hydraulic machinery and equipment. The flow of pressurized fluid is driven by pressure generated by the pump forcing it through the system, thus making cylinders, motors and other components work.
Several factors determine the pressure created by this pumping unit such as fluid flow rate, resistance in the system components, and efficiency of the pump itself. Fluid flow rate depends on hose diameter, pipe diameter and velocity of the fluid in motion. This can cause loss of pressure which affects how fast water can be pushed up from a well using a suction or centrifugal pump. Lastly, effectiveness of pumps depends on elements like design of pumps and viscosity of hydraulic oils.
Having knowledge about hydraulic system pump pressures will help maximize performance within these systems while ensuring that machines are running at optimal levels. By keeping track of their pumps’ pressures and making necessary modifications whenever required, people managing hydraulics may continue experiencing efficient operation from them.
Evaluating Your Current Hydraulic System
To attain more pump pressure in a hydraulic system, one should first access the current system to find out areas that need improvements. This is done through an intensive study of the system’s parts that include hydraulic pump, valves and others.
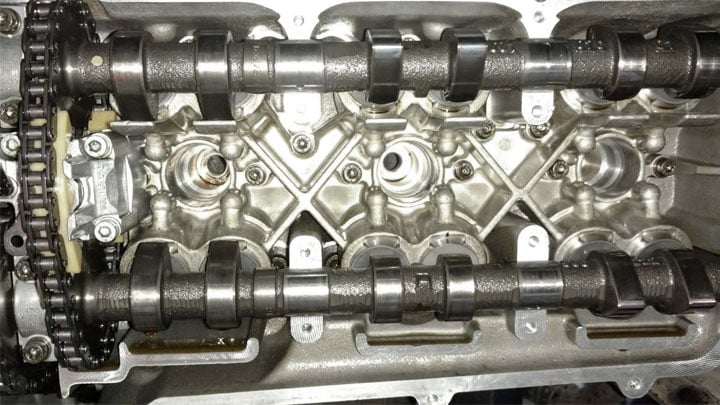
How to increase pump pressure ?
The heart of a hydraulic system is its pump, which plays a vital role in generating pump pressure. The pump must undergo thorough evaluation for it to bring about possible problems or inefficiencies leading to pump pressure. Pump’s state with its design, capacity are looked into before making a decision on whether it suits the area concerned.
As they control flow and pressure of hydraulic fluid, valves also form an integral part of hydraulic systems. Valve problems like leakages or malfunctions can reduce pump pressure. Thus their state is checked to ensure whether they work normal.
Other components within the hydraulic system such as hoses, fittings and filters must be assessed for their condition and efficiency. Any leaks or blockage can affect pump pressure hence reducing total performance of the entire system.
Once this analysis has been conducted on the hydraulic systems, there may be need for upgrading some components or replacing them so as to achieve high pumping pressures. In this way, operators are able to optimize their systems towards peak levels of performance and efficiency by focusing on areas requiring improvements.
Upgrading Hydraulic System Components
To reach higher pump pressures and optimize system performance, it is often necessary to upgrade hydraulic system components. Upgrades can be done on several parts including the pumps, valves and hoses.
One way of increasing pump pressure is through upgrading the hydraulic pump. A high-performance pump with greater capacity can generate more pressure and flow rates allowing for enhanced efficiency as well as performance. The upgraded pump must be compatible with the existing hydraulic system; thus, adjustments have to be made in order to accommodate the new pump.
Valves are critical components which could also be upgraded to enhance pump pressure. High-performance valves ensuring better accuracy and flow control will boost system efficiency while increasing pump pressure. Proportional valve upgrades may also enhance overall system performance by enabling accurate control over flow and pressure of the hydraulic fluid.
Another component that can be replaced with a view of improving on the pumped pressures is hoses themselves. Hoses having larger diameters and much better anti-pressurized drop properties lead to increased flow rates besides pumping pressures. As such, replacing them with synthetic rubber or thermoplastic materials that are of higher quality will generally improve the overall effectiveness of this hydraulic system.
Upgrading hydraulic system components does not only result in a rise in pump pressure but also other benefits might occur. Furthermore these improved components can lead to enhanced maintenance cost savings as well as reduced costs for repair hence lengthening life expectancy of any given hydraulics. It is therefore crucial before undertaking any upgrades into this area that specific needs and requirements related to hydraulics should be carefully considered so that they do not contradict one another while enhancing maximum return on investment for an organization.
Calculating System Performance
There are different industrial applications in which hydraulic systems find use, and their performance is crucial for the general productivity and effectiveness of the system. Pump pressure is one of the key performance parameters of a hydraulic system. Being conversant with how to calculate hydraulic system flow rate, pump pressure and power output is vital for improving system performance or upgrading to higher pump pressure.
Mathematical equations exist that can be used to calculate the performance of a hydraulic system. One of such equation is Bernoulli’s equation which relates any two point along a streamline using the pressures, velocities and elevations at those points. It also helps in determining the pressure drop across valves or fittings in a hydraulic system.
Similarly important is Darcy-Weisbach equation that calculates friction loss due to pipe or hose. The formula takes into consideration parameters such as flow rate, pipe diameters’ viscosities density and length.
The second step in calculating pump head involves using pump curve. It shows graphically how flow rate varies with respect to pump head. Prospective engineers can simply look up at any position on this graph and determine what level of head will correspond to a given flow; implying that it will be useful when selecting pumps for designated applications where there already exists a current installed capacity.
In addition to determining pump pressure, it is also essential to calculate the flow rate within a hydraulic system. Flow rate refers to volume-based measurement of fluid passing through within time limits across entire systems whose dimensions depend on pipes diameter as well as its cross-sectional area.
Moreover, using this relation; Power (Watts) = Pressure (Pascal) x Flow Rate (m3/s), determines the total power output by dividing these values: Watts by Pressure (Pascal).
For backward compatibility purposes, accurate measurements are required throughout all calculations made like those involving mechanical energy transfer between individual components inside pumping stations while some parts were worn-out so they appear less efficient than would have been expected otherwise.
Adjusting System Parameters
Adjusting different system parameters like pressure relief valves, flow control valves and any other component may help to achieve higher pump pressures in hydraulic systems. Proper adjustment of these parameters is essential for optimizing system performance and preventing damage to system components.
One of the most common ways to adjust system parameters is by adjusting the valve. The relief valve acts as a safety device that ensures prevention of excess pressurization in hydraulic systems. By adjusting the valve, it is possible to increase the maximum pressure in the system leading to higher pump pressure. However, over-adjustment could be harmful to other parts such as hoses, fittings, and valves within the said system. Thus, reading and following manufacturer’s guidelines would be crucial before making adjustments on any part of this kind.

How to increase pump pressure ?
Another option for controlling these settings involves regulating flow through a flow control valve. The flow control valve controls fluid flow within a hydraulic system and can be adjusted to increase or reduce this rate. In summary increasing the liquid pressure will raise pump pressure too if we would adjust flow control valves properly since they are used in similar operation but with different results if improperly managed i.e., when there is much liquid it may make some things like pumps or evolution burn due to overheating.
In addition to adjusting the relief and flow control valves, adjustment of other components might also be necessary so as to get higher pump pressure rates. For example, pipes diameter in both tubes should be increased when there aim is high rate flow so that one can avoid falling off water column as well as pipe loses which result from high velocity fluid motion along inner walls . Additionally, upgrading your pump may require an improved rate of flow or even higher pressure capacity depending on how efficient you want it.
It should however be noted that only qualified persons who have proper knowledge about such matters should make these changes on their own accord because they are very risky for untrained people who don’t know much about them; Therefore you should make sure that you read and apply manufacturers recommendations while adjusting system parameters so as to avoid any harm on your machine parts and thus achieve the best performance.
In order to ensure the effectiveness of the adjustments made in these parameters, it is important to maintain a hydraulic system regularly. This will include regular checking of systems components such as hoses, valves, pumps among others and replacement of any worn out or faulty component. In so doing, operators can make sure that their machines perform optimally and consequently achieve the desired pump pressure.
Installation and Maintenance
For a hydraulic system to work well and avoid failure, its upgraded components must be installed properly and maintained. This paper looks at some of the things that need to be considered during installation and maintenance of hydraulic system components:
- Proper installation procedures: To have proper installation of hydraulic system components, it is important for one to adhere to the manufacturer’s guidelines and instructions. The improper fitment can lead to system failure, poor performance or safety concerns. One should observe all the factors during installation such as proper alignment of all components, fixing them tightly in position and ensuring that there are no leaks on any point where fittings have been connected.
- Use of quality components: For an improved performance and durability, high quality parts that meet industry standards and specifications must be used in the hydraulic systems. Using sub-standard parts may result into early failure of these materials besides reducing their productivity and also causes accidents within this process.
- Regular maintenance: Regular servicing is very critical because it enables the operators of the system understand how well it is working as expected thus helping them identify problems earlier in advance before they lead to machine breakdowns. Maintenance practices ought to include periodic inspection of system elements like hoses, valves, pumps among others while replacing those which have deteriorated completely so far by means like wearing out or physical breakage. Additionally the fluid level plus its condition has always to be checked often with appropriate alterations being done when necessary.
- Proper fluid selection: How long this equipment will last depends on choosing a suitable fluid for its operation; therefore, this affects directly its functioning ability and duration. A compatible fluid with other system components should be put together by taking into account manufacturing recommendations at all times. Such erroneous fluids tend not only bring about low performances but also cause premature depletion.
- Training and education: Proper training offers an assurance that staff operating such facilities are safe enough while carrying out their duties as prescribed by law so as not put lives at risk anyhow. In order for operators and maintenance personnel to use the system correctly, identify problems that may occur over time within it as well as how they look like or should be done.
By taking these aspects into account regarding installing and maintaining hydraulic system components, operators can ensure that the desired pump pressure is achieved and the system is functioning optimally. System failure can only be prevented if proper installation and maintenance are put in place; performance is enhanced while safety remains paramount.

How to increase pump pressure ?
Industry Standards and Regulations
There are standards and regulations that apply to the hydraulic system when it is being upgraded. Ensuring safety, reliability and excellent performance of hydraulic system requires adherence to these standards and regulations.
A number of important industry standards and regulations that apply to hydraulic systems include:
- ISO standards: The International Organization for Standardization (ISO) has developed a range of standards which are applicable to hydraulic systems. These standards deal with different aspects such as design, performance, safety in a hydraulic system and conforming to them ensures that the required levels of safety and performance are met by the system.
- ASME standards: The American Society of Mechanical Engineers has developed several codes with respect to hydraulics including pressure vessels, piping, and fittings. These standards govern how the hydraulics should be designed so that they can be installed safely for an effective operation.
- OSHA regulations: Occupational Safety and Health Administration (OSHA) has enacted rules that apply to workplace hydraulic systems. Some areas covered by these regulations include personal protective equipment use, machine guarding requirements, hazard communication etc.
- Environmental regulations: Leaky or poorly maintained hydraulic systems can have significant effects on the environment. Therefore it is necessary to comply with environmental statutes that relate specifically with such systems like oil discharge regulation for example.
- Local codes and regulations: There may also exist local codes or statute laws pertaining to specific kind of machinery depending on where one resides or wants the particular machinery installed.
The reason why compliance with industry standards and regulations is crucial is in ensuring safety, reliability as well as optimum functioning of the system itself. This means operators must be conversant with relevant directives which are mandatory in designing, installing, operating or maintaining a given hydraulic equipment. At times checks can facilitate conformity hence ability to identify possible challenge areas through tracking deviations from set guidelines within prescribed timeframes allowing course correction approaches when still viable.
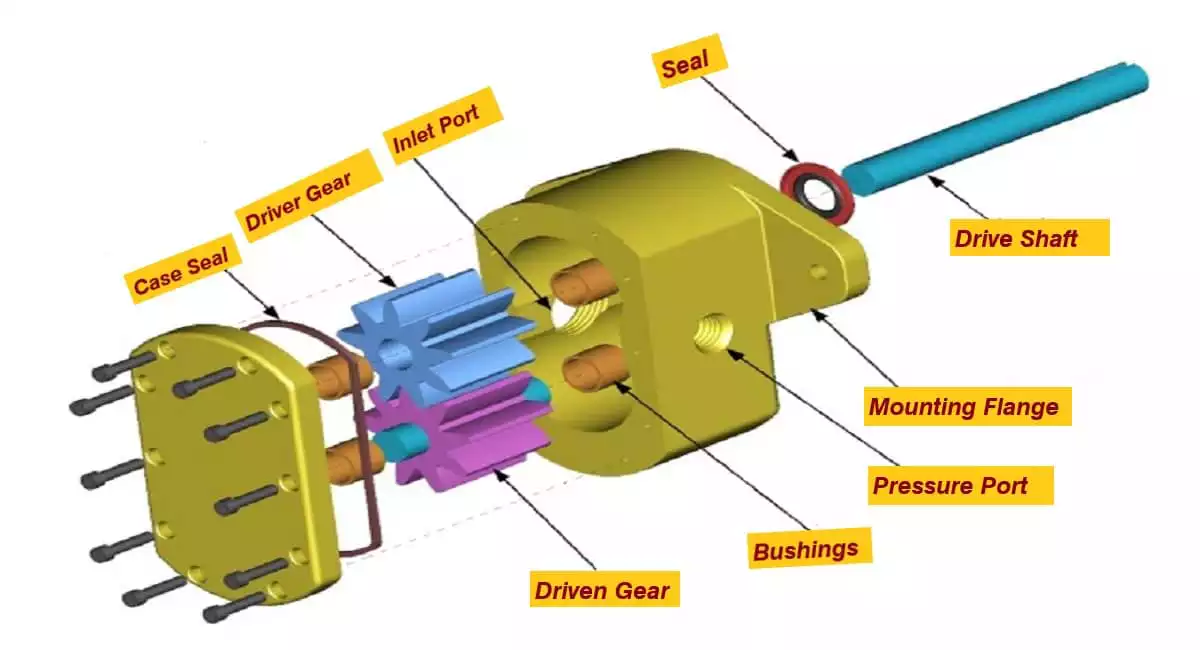
How to increase pump pressure ?
Conclusion
In order to enhance the pressure of a pump, upgrading a hydraulic system implies a higher output is produced, efficient utilization of resources and increased performance. These factors include flow rate, pressure drop and system efficiency which would have to be identified in order to achieve high pump pressures. Thus calculations can be done using mathematical formulas to determine how well or poor the system is as well as areas that could do with an upgrade.
Alternatively we can obtain high pump pressures by adjusting such parameters like flow control valves and pressure relief valves. However it is important to ensure that adjustments are made safely and correctly, while compliance with industry standards and regulations are maintained.
It is therefore important for proper fitting and maintenance of hydraulic system components so as to avert any breakdown in these systems. Therefore operators should use good quality units or maintenance personnel together with regular care procedures hence they can believe on its functioning without problems.
Finally, for safety, reliability and effectiveness of the hydraulic device; we must adhere to industry standards/regulations. Operators plus maintenance personnel should have knowledge about standards/ rules covering these aspects so that their design installation and safekeeping comes within such limits.
Thus upgrading a hydraulic system towards higher pump pressure involves considering factors such as; installation/maintenance activities, conformity to industrial norms set plus system performance parameters. If followed systematically these considerations would lead into improved operation efficiency of a hydraulic device leading ultimately into increased pump pressures.