June 21, 2024
The Importance of Proper Hydraulic Valve Adjustment in Industrial Systems
Industrial systems that use hydraulic equipment should have a hydraulic valve adjustment. This is to optimize the system, making it work perfectly and avoid future risks. This paper provides an in-depth understanding of hydraulic valve adjustment and what happens when one does not do it correctly, the best ways for doing hydraulic valve adjustments, benefits of proper adjustment including case study of some successful implementations.
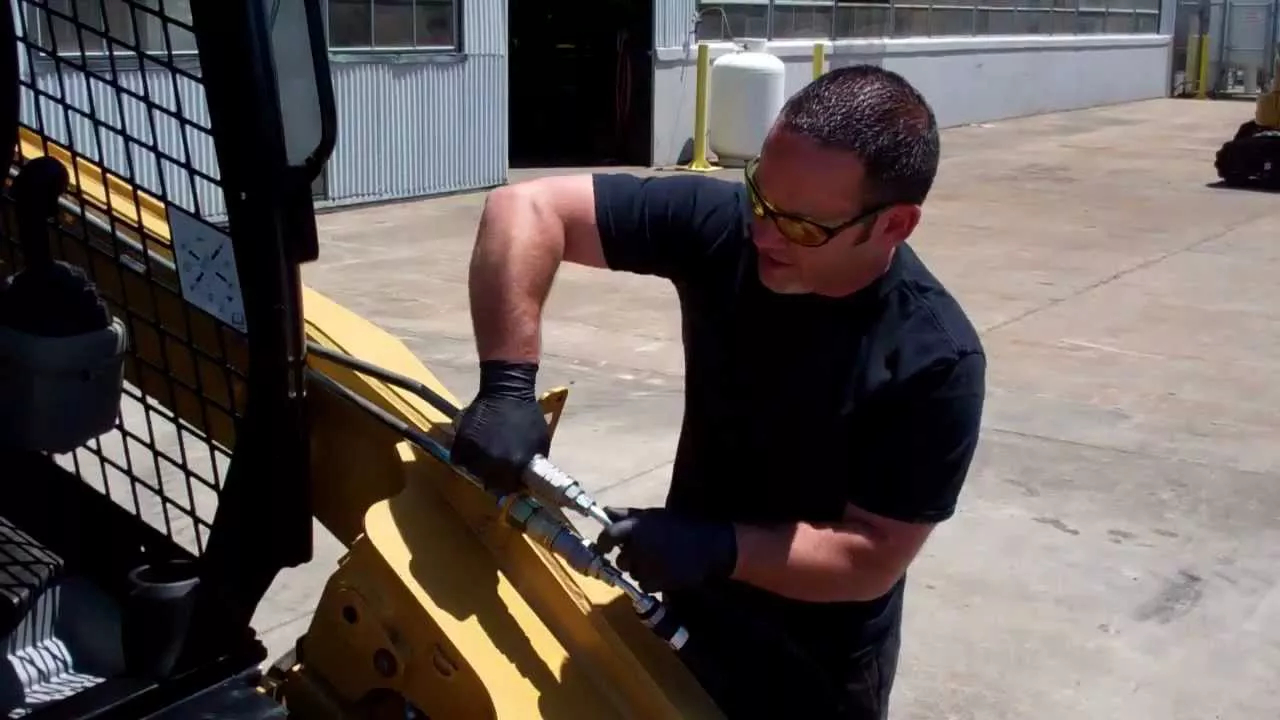
hydraulic valve adjustment
It is important to regulate the way hydraulic valves operate to maintain efficiency at optimal conditions. Various industries such as manufacturing, construction and transport rely on hydraulic systems. Consequently, breakdowns in this specific machine can lead downtime and production hitches due to financial losses. Thus, periodic check ups and maintenance are vital for optimum performance of the hydraulic system. The goal of this paper is to enlighten readers about why they should adjust their valves well if they want their systems performing optimally.
Understanding Hydraulic Valve Adjustment
Hydraulic valve adjustment is when the clearance between the valve and the rocker arm in a hydraulic system has to be adjusted. The hydraulic valve adjustment system comprises of parts like camshaft, lifters, pushrods, rocker arms and valves. By adjusting the clearance, this ensures that there is an optimal operation of the valve by establishing a proper contact between it and the rocker arm.
The correct and accurate hydraulic valve adjustment is vital for several reasons. First, It makes sure that valves open and close at the right times so that the system works efficiently. If not adjusted accurately, then it may lead to incomplete closing or opening of a valve hence poor systems efficiency. Secondarily, It reduces noise produced from treadle by providing silent operation of systems. Finally, these adjustments ensure that premature wearing does not occur on valves or other parts making it need costly replacement.
Determining whether there is a need for hydraulic valve adjustment involves different techniques. This includes listening to unusual sounds from your engine which are one of those common methods used till today. If you hear a taping sound from your engine then you should check up on your valve clearance as this might be an indicator for its adjustment requirement Lastly, it’s good to seek assistance from your mechanic who can give necessary instructions based on various specifications such as manufacturer’s recommendations regarding intervals for checking their adjustments against engine specifications . In case it hasn’t been done for quite some time since start-up then one has to adjust themselves properly with respect to optimum performance.
To sum up knowledge about hydraulic valve adjustment together with its components helps in optimizing system performance.Precision in terms of setting also comes with some advantages such as improved energy consumption tendencies.Therefore,taking good care of such a valuable part must be done regularly in order to avoid malfunctioning when needed most.
Impacts of Improper Hydraulic Valve Adjustment
Improper hydraulic valve adjustment can significantly affect system performance, efficiency and safety. Here are some of the consequences of an incorrectly adjusted hydraulic valve:
- Reduced System Performance and Efficiency: When the valve clearance is not properly adjusted, it may not open or close completely causing the engine to run inefficiently. This can result in decreased power output, lower fuel economy, and increased pollutants.
- Increased Risk of Equipment Failure and Downtime: Faulty valve adjustments could cause the valves or other parts to wear out faster than they normally would, requiring expensive replacements or repairs. Additionally this may lead to unscheduled equipment breakdowns resulting in time delays for production purposes as well losses on financial basis.
- Safety Considerations: Various risks are associated with wrong positioning of hydraulic valves. For instance, if a fluid passes through a partially closed port after sticking inside it due to overheat then it will cause engine overheating or oil leakage that might put on danger those workers near machinery.
- Environmental Impact: Incorrect adjustments to hydraulic valves can also increase emissions leading to air pollution which has adverse effects on the environment.
In summary, insufficient hydraulic-valve setting causes serious challenges in terms of system performance, efficiency levels as well as safety issues related to industrial systems. Henceforth there is need for regular checks in order to help maintain maximum productivity levels and ensure a safe working environment for every one inside the industry.
Best Practices for Hydraulic Valve Adjustment
To perform a proper hydraulic valve adjustment, an understanding of the system’s requirements and specifications is important. Below are some best practices for ensuring that hydraulic valve is adjusted in the right manner:
- Understanding System Requirements and Specifications:One needs to understand the requirements and specifications of the system including manufacturer recommendations regarding valve clearance and adjustment intervals. This information can be obtained from the system manual or directly contacting a manufacturer.
- Proper Use of Tools and Equipment:Adequate tools and equipment are important when performing proper hydraulic valve adjustment. Make sure that you use high quality tools designed specifically for adjusting hydraulic valves.
- Proper Adjustment Techniques:During this process, one has to loosen lock nut and adjust valve clearance via feeler gauge. Valve clearance should be set according to manufacture’s recommended specification. Before making any changes it is necessary to ensure that the appropriate value is completely closed.
- Regular Maintenance And Inspection:Hydraulic systems require regular maintenance and inspection for them to perform optimally. It is advisable as per manufacturer’s recommendations to do valve adjustments at certain intervals while still conducting regular inspections that may help detect problems earlier thus avoiding expensive repairs or replacements.
- Follow Safety Procedures:Safety procedures should always be followed when dealing with hydraulic systems due to their dangerous nature. This involves putting on appropriate personal protective equipment, turning off equipment before adjustments are made, as well as keeping safety guidelines laid down by manufacturers.
To sum up, observing best practices when adjusting hydraulic valves can guarantee optimal performance of a system hence minimizing chances of machine breakdowns and downtime.It means having knowledge about specifications of the system, using correct devices depending on tools used in work, adopting suitable approaches for varying valves’ settings during installation processes; carrying out timely preventive cares cum review checks; as well as adherence to security standards always observed throughout all operations done in this regard.
Benefits of Proper Hydraulic Valve Adjustment
The importance of proper hydraulic valve adjustment cannot be underestimated, as it brings numerous merits like better system operational and efficiency, long life of equipment, low maintenance costs, increased safety and environment. The following are some benefits that come with proper hydraulic valve adjustment.
- Improved System Performance and Efficiency: To ensure that the valves operate at their best positions the hydraulic valve setting should always be okay. This leads to improved overall system performance while reducing fuel consumption hence saving money.
- Extended Equipment Lifespan: Hydraulic machines are expensive and can break down prematurely. Proper hydraulic valve adjustment keeps the machine in an optimal working condition hence preventing their early failure.
- Reduced Maintenance Needs: Good hydraulic valve adjustment minimizes repair expenses thus time and money involved in frequent breakdowns through costly repairs.
- Improved Safety and Environmental Performance: For example, by properly adjusting a hydraulic valve one will minimize the chances of accidents such as overheating or oil leakage which improves worker safety around operators who maintain this type of machinery. Additionally, this reduces emissions hence cleaner environment.

hydraulic valve adjustment
In conclusion, there are several advantages related to proper hydraulic valve adjustment such as enhanced efficiency of the system durability of devices used, reduced need for maintenance activities carried out on them, improved safety as well as environmental contribution. Best practices for hydraulic valve adjustment must be followed to ensure that systems run smoothly and without hitches so that they result into cost savings plus good performance.
Case Studies
Many instances have shown the advantages of proper adjustment of hydraulic valves. Here are some examples of successful case studies and their results.
- Case Study 1: A hydraulic system in a manufacturing company was observed to underperform with increased levels of noise. This resulted from clearance problems with their hydraulic valves upon examination. The performance and efficiency of the system improved after this was done, while its noise levels significantly dropped. The firm noted that there were reduced maintenance costs and less fuel consumption.
- Case Study 2: The cause of frequent equipment failures at a construction company was traced back to its hydraulic systems that required valve clearance adjustments. Upon inspection, it was determined that the valve clearances were incorrect and needed adjusting. Once adjusted, equipment downtime went down significantly in the company. The firm also reported reduced machinery breakdowns as well as maintenance needs.
- Case Study 3: In a transport company, higher emissions rates and lower fuel efficiencies were detected throughout their fleet operations. This arose from clearance problems with their hydraulic valves following inspection. As such, these improvements have led to decreased emissions for the fleet with improved fuel economy which have brought cost savings along with an enhanced environmental performance.
These case studies show what can be achieved through proper adjustment of hydraulic valves, including better system performance and efficiency, reduced maintenance costs, and savings on expenditures incurred by businesses. Regular maintenance including hydraulic valve adjustment has been associated with substantial cost savings together with improved system performance.
To sum up, various case studies have proven that adjusting hydraulic valves properly brings about better system performances as well as saving costs on operations carried out within these systems or devices concerned about their working abilities like how much energy they consume or produce per unit time . Best practices for adjusting hydraulic valves can lead to longer lifespans for equipment; fewer repairs; and greener operation policies concerning environmental management law compliance rnvironmental friendliness/lnvironmental efficacy/enforcement of environment protection regulations/actions regarding environment protection/and re-occurring actions done for environmental sustainability or pollution prevention efforts.
Conclusion
In conclusion, one of the most critical things about hydraulic equipment used in industrial systems is hydraulic valve adjustment. This ensures optimal system performance, prolonged lifespan of equipment, decreased need for maintenance, increased safety and improvement in environmental performance. Otherwise adjusted valves may reduce system efficiency and performance; increase risks of equipment failure and downtime; pose threats to safety measures and have an environmental impact.
Some of the best practices for adjusting a hydraulic valve are knowledge on system requirements/specifications, using appropriate tools and machinery as well as following the right way when it comes to adjustment techniques. Periodic inspection and maintenance should be carried out together with adherence to safety protocols. The above mentioned best practices will enable improved system performance; cuts in maintenance needs as well as cost savings.
Case studies show that proper hydraulic valve adjustments have numerous advantages including enhanced system performance and efficiencies, lower maintenance requirements and expense reduction. Thus it is very important for industrial systems utilizing hydraulic devices to make sure they give priority to proper hydraulic valve adjustment among their routine check-ups and inspections.

hydraulic valve adjustment
In conclusion, we cannot overemphasize enough how vital it is for someone to adjust their valves properly. Putting into action good practices while adjusting a hydraulic valve can boost a systems’ efficiency, elongate the useful life span of an equipment, reduce service demand rate levels as well as enhance safety while at the same time preserving environment. It’s therefore our plea that all industrial systems incorporating hydraulics take these factors into consideration so that optimal system performance prevails ensuring its users’ safety too.