June 21, 2024
Measuring and Managing Pump Load: Best Practices for Efficient Operation
When dealing with a fluid transfer system, pump load becomes a very sensitive aspect of almost all industrial establishments. Measuring pump loads correctly and managing them can cause considerable effects on energy usage, equipment life and overall operational costs. This article investigates the significance of managing pump load, and suggests tips for effective management of pump loads.
Pump load refers to the work done in moving fluid in a system. Many factors affect it, such as liquid properties, flow rate and system pressure. Accurate measurement of pump load is important for sizing the right size of pump that will allow safe operation within the design parameters.
Industrial operations may be affected negatively by poor management practices regarding inefficient pump loads. These include high energy consumption and running costs, additional wear on machines or gear plus safety issues and environmental concerns. By adopting best practices for managing pump loads facilities could reduce expenditures, become safer environmentally friendlier entities while equipment’s lifespan increases.
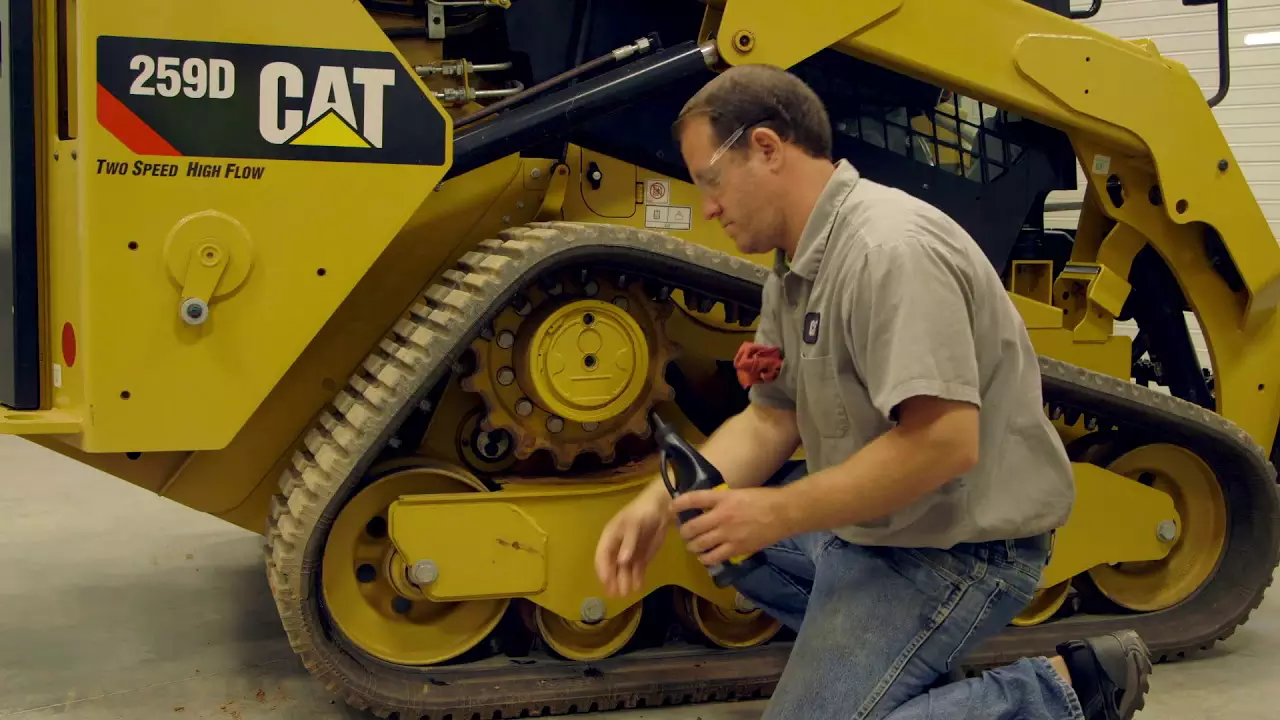
pump load
What follows are sections discussing parts of a machine that contribute to pump load such as; calculation methods on how to arrive at the figure then impacts when there is excessive loading on pumps. The next section will describe ways in which we can address this issue through best practices around efficient use of pumps. Finally, this paper will summarize some key points while stressing out why industries have to know how they should manage their allotted time periods concerning effort required for these machines.
Understanding Pump Load
For one to manage pump load effectively, comprehending its definition together with components is vital. Pump load refers to the work needed to move fluid through a system, and it is typically measured in power terms like kilowatts (kW) or horsepower (hp).
The components of pump load include static head, friction head, and acceleration head. Static head corresponds to the height difference between the pump and the topmost point of the fluid system and represents potential energy that must be expended for lifting the fluid. Friction head accounts for energy necessary to overcome brakes as fluid moves through a system. Acceleration head indicates energy required to bring the fluid up to speed.
To compute this kind of power, an individual must determine flow rate from which he/she will measure velocity of movement of liquid, pressure difference between inlet and outlet of a device as well as physical properties of water being pumped. Flow rate refers to volume of liquid going through a device within a given time frame that can be either liters per minute (LPM) or gallons per minute (GPM). System pressure stands for dissimilarity in pressure levels existing from one side into another part within a pumping machine which may be expressed either in pounds per square inch (PSI) or bars. Density and viscosity are some features related to density; they influence amount of work done when fluids have been displaced.
Measurement accuracy plays an important role when choosing an optimal size and ensuring safe and efficient operation conditions for such systems. An oversized pump will lead to high costs associated with consumption of excessive amounts of electric power while an undersized unit affects performance negatively therefore requiring more maintenance activities than planned before. By accurately establishing pump’s load facilities can save money by buying pumps appropriate size thereby improving their system efficiency accordingly.
Impacts of High Pump Load
Industrial operations can be negatively affected by high pump load in many ways. It can result in more energy consumption and costs, shorter lifespan of equipment and the need for more maintenance. High pump load also pose safety and environmental problems.
One of the primary impacts of high pump load is increased energy consumption and costs. A pump running at high capacity will need more power to push fluid through a system that leads to higher energy consumption and costs. This can have significant impacts on facility operational costs especially if pumps are operating under high load conditions over long periods.
High pump load may also reduce equipment life and increase maintenance requirements. Pumps that operate at high loads incur extra wear and tear which contributes to premature failure and more maintenance charges. Consequently, this will lead to longer downtime, cost of repairs as well as lost productivity.
Apart from these operational effects, high pump load has both safety and environmental significance. An overpowered pump could cause increased vibration leading to hazardous noise levels for workers’ ears. Similarly, it would cause leaks or spills that would pollute the environment.
In conclusion, industrial operations can suffer greatly because of high pump load. If companies manage their pump loads effectively, they will reduce energy use hence cut costs, extend lifespan for equipment besides enhancing safety measures along with environmental performance.
Best Practices for Efficient Pump Load Management
To manage efficiently the load on pumps and reduce the effects of high pump load, it is necessary to adopt best practices for efficient pump load management. The most important ones are as follows:
- Use of Variable Frequency Drives (VFDs): VFDs enable precise control of the speed of the pump which reduces energy usage and costs. Facilities can avoid running the pump at high loads by adjusting its speed to match required flow rate and this will result in lower energy consumption.
- Proper Pump Selection and Sizing: For effective pump load management, it is important that pumps be sized correctly to correspond with system pressure and required capacity. If a pump is either oversized or undersized, system performance will suffer, leading to increased energy usage, maintenance requirements.
- Regular Maintenance and Inspection: It should be noted that frequent maintenance for pumps can help detect problems before they elevate into increased energy consumption rates as well as equipment breakdowns. Also regular maintenance ensures that any pumping done within safe operating limits.
- Monitoring and Analysis of Pump Load Data: To increase efficiency and decrease energy use, companies need to regularly monitor and analyze data concerning pumping loads. Taking note of load history together with overall system performance allows for determining trends so as to better improve system efficiency.
With the implementation of these best practices facilities can enhance their capability to manage pump loads more effectively thus reducing power consumption, extending life cycle costs of equipment while improving safety in terms of human beings involved or environment around them.
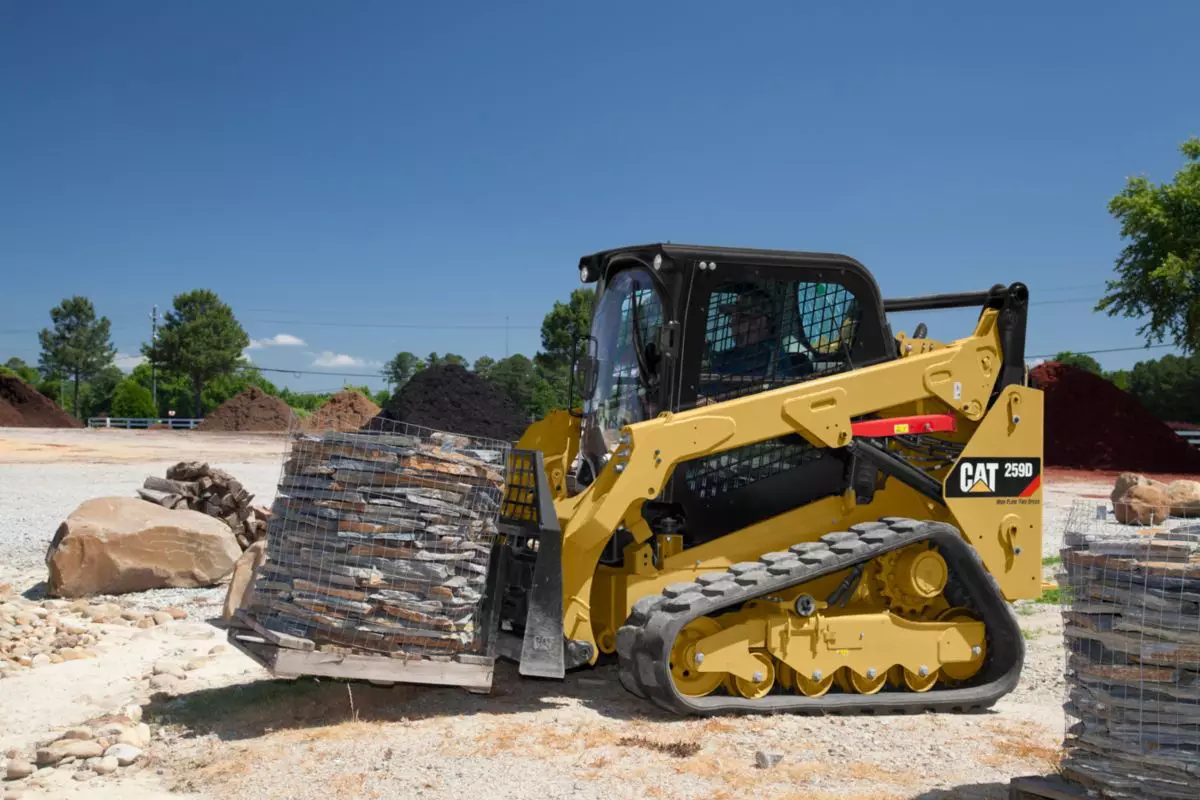
pump load
Benefits of Effective Pump Load Management
Industrial operations can benefit a lot from an effective management of pump load. Some key benefits may include:
- Reduced Energy Consumption and Costs: Efficient handling of pump loads can lead to reduced energy consumption and costs at the facilities. This can improve profitability and is a major determinant of operational cost for any factory.
- Longer Equipment Lifespan and Reduced Maintenance Requirements: Facilities that do not experience high levels of pump loads reduce wear and tear on equipment hence it increases its lifespan, thus this also reduces maintenance needs as well as reducing the down time for machines hence increase in productivity.
- Improved Safety and Environmental Performance: There is safety improvement through efficient pump load management because it cuts down the risk of machine failure and dangers which come with it. It also has ecological advantages as it curtails energy consumption, emission rates, prevents oil spillages etc.
- Better System Performance: By running pumps within their safe limits, facilities are able to improve system performance. As a result, system problems like cavitation that cause poor performance are eliminated.
In conclusion, when properly adopted in industrial activities, effective pump load control would have huge positive implications. It therefore helps in increasing profits via reduction of power usage and charges incurred; improving safety standards; environmental conservation; making systems work better without cavitation among others.
Case Studies
Let us see some case studies of some companies that have put in place some best practices for pump load management to further illustrate the advantages of efficient pump load management.
Case Study 1: Chemical Manufacturing Facility
For instance, a chemical manufacturing facility had high energy consumption and costs due to oversized pumps being in operation. In order to ensure that pumps are accurately sized according to system pressure and flow rate requirements, the facility implemented a pump sizing and selection program. Another measure taken by the facility was the installation of variable frequency drives (VFDs) for exacting control over pump speeds resulting in decreased power consumption.
The changes led to a 30% decrease in energy use by the facility as well as 40% less cost on maintenance associated with pumps. Furthermore, equipment lifespan got extended while safety along with environmental performance improved at site.
Case Study 2: Municipal Water Treatment Plant
In addition, a municipal water treatment plant faced challenges emanating from pump cavitation which affected system performance negatively hence increasing maintenance requirements. For example, it established a monitoring program for determining loads on pumps.
On examining data about pump loads used at the time; such information helped identify those parts where cavitation was taking place thus leading to reduced loads being exerted on these areas. Eventually there were lower needs for maintenance, improved system performance and prolonged machine life expectancy.
Case Study 3: Mining Operation
For example, an oversized-facility pupming operation had high energy consumption and costs. In order to ensure that pumps are accurately sized according to system pressure and flow rate requirements, the facility implemented a pump sizing and selection program. Another change made by this facility involved installing VFDs which increased precision of speed control thereby reducing energy usage in pumping operations.
Consequently, its annual power consumption reduced by approximately 25%, while specific expenses spent on servicing pumps fell around 35%. Moreover, this organization succeeded in extending working life cycle of equipment and increased health, safety and environment performance.
These case studies show the benefits of effective pump load management as well as the significance of accurate pump sizing and selection, VFDs, regular inspection and maintenance, and monitoring and analyzing of pump load data. By using these best practices, companies can decrease energy usage and costs, prolong machine life expectancy, improve environmental safety.
Conclusion
Fluid transfer systems are important to many industrial operations. They should be constructed in such a way that allows effective pump load management. It is important to precisely measure and manage pump load as it helps reduce energy consumption, cutting costs, extending the equipment life span , improving safety and environmental performance and enhancing system efficiency.
It is essential to understand its components and calculate it accurately for effective pump load management . VFDs use, correct pump selection and sizing, regular maintenance / inspection of pumps, monitoring / analysis of loads on the pumps are all examples of best practices in efficient pump load management.
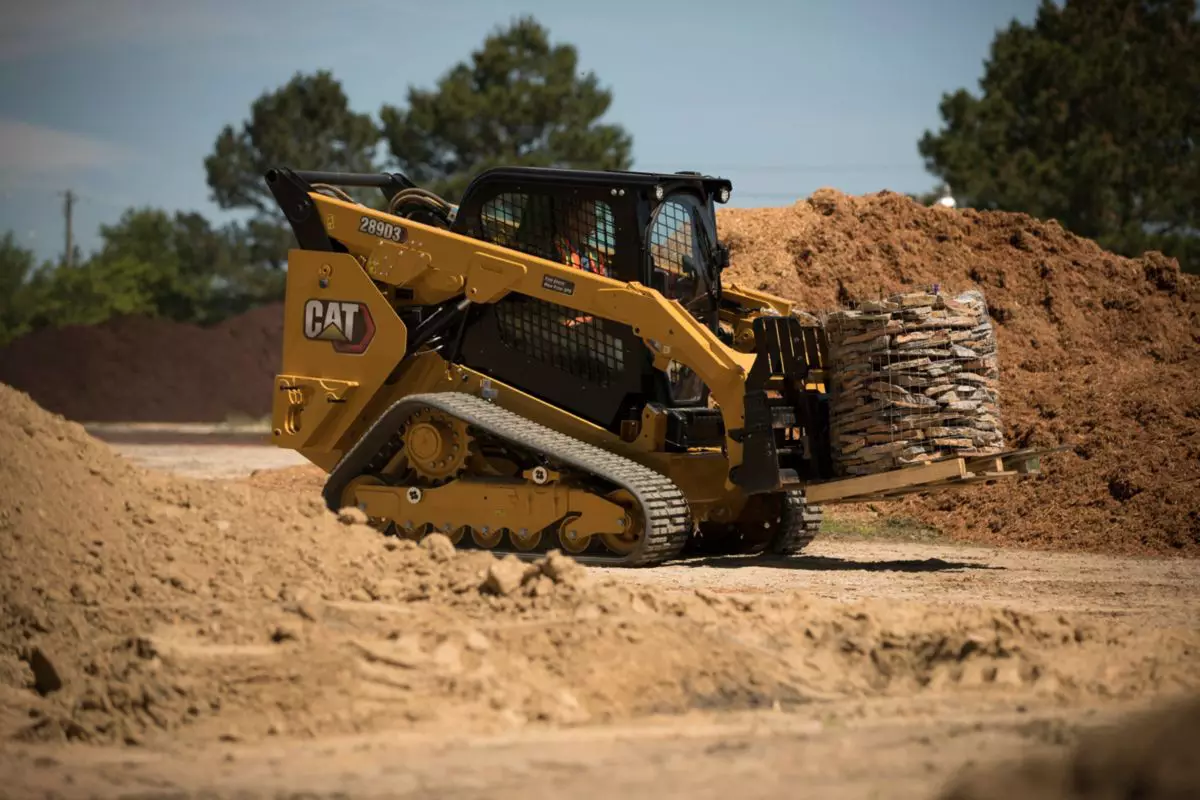
pump load
Studies have shown that proper pump load management practices can save a lot of energy and money for organizations while their equipment will last more thus contributing to improved safety and environmental performance.
To sum up, there are clear advantages that come with an efficient method of managing one’s loads. For instance, enterprises that adhere to some best practices for handling their loads well tend to gain much in terms of profit making hence higher sustainability plus safer work environment. Efficient operation and safety of fluid transport systems require facilities to give priority to managing pump loads through implementation of best practices.