June 21, 2024
Everything You Need to Know About Pompa Hydraulic Pumps
In various industrial applications, pompa hydraulic pumps are components that are essential to hydraulic systems. They provide mechanical power which is converted into hydraulic energy thereby making a flow of fluid and pressure that powers machines and equipment. In this article we will provide an introduction to pompa hydraulic pumps including the definition, importance, and types.
Definition of Pompa Hydraulic Pumps
These are mechanical devices operating under fluid flow that transforms mechanical energy into hydraulic energy by using pressures. Usually employed in hydraulic systems powering such as presses, lifts and cranes etc., these assemblies generate fluid movement by imparting certain energy on it from a single place to another. This is achieved by means of forcing that fluid via different channels or tubes throughout the body of the system until it reaches its output terminal.
Importance of Pompa Hydraulic Pumps in Industrial Applications
Pompa hydraulic pumps perform key functions in several industrial applications whereby they drive machines and equipment for such tasks. Manufacturing, construction, transportation industries among many others use them widely today. While compared with other types of pumps, pompa hydraulic pumps have some advantages over them such as being more efficient than others, having high power density as well as allowing for much accurate control over the rate at which fluids flow out.
Types of Pompa Hydraulic Pumps
The different types include:
- Gear Pumps Gear pumps that use two or more rotating gears for pumping fluid produce flow and pressure inside a system known as gear pump. They are simple and reliable in nature hence commonly used on low to medium-pressure configurations.
- Vane Pumps Vane pump employs vanes on rotor to create flow or build up pressure within its chambers while operating at low-to medium-pressure ranges.
- Piston Pumps Piston pump uses one ore more according to their sizes pistons for creating either liquid movement (flow) or compression (pressure). These kinds provide excellent performance when used under high pressure conditions.
To summarize then pompa hydraulic pumps are important elements of hydraulic systems used in various industrial applications. They convert mechanical energy into hydraulic energy thus leading to fluid flow and pressure that can be utilized in operating machines or equipment. To conclude, the definition, importance and types of pompa hydraulic pumps should assist enterprises in picking what pump model will fit their needs best thus ensuring the highest performance level as well as output efficiency.
Understanding Hydraulic Systems
Various industries rely on hydraulic systems to transmit power efficiently and with reliability. They employ fluid transmission to move forces from one place to another commonly using water or oil. In this part of the paper, we will provide a general overview of hydraulic systems focusing on its basics, importance in industry and components.
Basics for Hydraulic Systems
Hydraulic systems operate based on Pascal’s law that states that pressure exerted at any point within a confined liquid varies equally in all directions. The hydraulic systems are made up of a pump, control valve and actuator. The system is normally closed; meaning the fluid is retained within the system and pumped around by the pumping mechanism.
Significance of Hydraulic Systems in Industry
Hydraulic systems are integral parts of various industrial applications that involve transmitting power reliably and efficiently. These include manufacturing industries such as automotive, food processing among others as well as transport sectors like road construction etc… Hydraulics also has several advantages over other power transmission systems such as high power density, fine control and ease of maintenance.
Components for Hydraulic Systems
Hydraulic systems consist of several components, including:
- Pump: It creates fluid flow and pressure which supplies energy required to run the system. There exist different types of pumps used in hydraulic systems including gear pumps, vane pumps, piston pumps among others.
- Control Valve: It regulates flow rate/pressure directing fluid into or out of actuators as need be. Several types of control valves used in hydraulics include directional control valves, pressure control valves as well as flow control valves.
- Actuator: The actuator converts pressure from liquids into mechanical force allowing it to perform work. Different kinds include cylinders motors brakes etc.
- Reservoir: This stores fluid used by the system which can be pumped by the pump while also acting as heat sink for dissipating heat generated by it.
- Filter: It removes garbage from the fluid preventing damage to tools where possible ensuring smooth functioning of the entire set-up.
In conclusion hydraulic systems are essential for various industrial applications where power is transmitted efficiently and reliably. They employ fluid transmission of forces over a distance and have several components which include among others, pump, control valve, actuator, reservoir and filter. Understanding the basics and components of hydraulic systems can help businesses select the right system for their specific application, ensuring optimal performance and efficiency.
How Pompa Hydraulic Pumps Work
Pompa hydraulic pumps are mechanical elements of hydraulic systems that transform mechanical energy into hydraulic energy that may be utilized to run machinery and equipment. Let’s give an overview of the way in which pompa hydraulic pumps work, explaining what is their working principle, main components and types of supplied systems.
Working Principle of Pompa Hydraulic Pumps
The principle behind pompa hydraulic pumps is based on displacement, where movement of a piston, vane or gear produces fluid flow and pressure. The pump is connected to a hydraulic system so as to allow fluid circulation within it under pressure for use in powering machines and equipments.
Components Of Pompa Hydraulic Pumps
The several components that make up Pompa Hydraulic Pumps are:
- Inlet And Outlet Ports The inlet port connects the pump with the hydraulic system for fluid intake while outlet ports connect the pump with the system to discharge the fluid.
- Pump Body This houses all internal parts of the pump and is designed in such a way as to withstand pressures created by pumping actions.
- Internal Components These include rotors, vanes gears or pistons depending on the type of pump being used. All these work together resulting in fluid flow and pressure creation.
- Shaft And Bearings Shaft is meant for supporting rotating internal parts while bearings are designed to facilitate free rotation between such parts.
Types Of Pompa Hydraulic Pump Systems
There are several types of pompa hydraulic pump systems each specializing for different applications including:
- Fixed Displacement Pump Systems Their motion causes them to deliver a fixed amount of liquid per revolution. They have versatile applicability but mostly useful when constant flow rate is needed such as in compressor lifts or presses.
- Variable Displacement Pump Systems These ones have variable amounts being delivered per revolution hence greater control over both fluid flow and pressure can be achieved. Typical applications include e.g., cranes or excavators where varying flow rates might be required at different times.
- Radial Piston Pump Systems This kind makes use of a set of radial pistons to create fluid flow and pressure. They are highly efficient and usually used in high pressure applications.
In conclusion, pompa hydraulic pumps are mechanical elements of hydraulic systems that convert mechanical energy into hydraulic energy which may be utilized for running machinery and equipment. Pompa hydraulic pumps function on the principle of displacement where movement of a piston, vane or gear produces fluid flow and pressure. With knowledge on working principle, components and types of pompa hydraulic pump systems; business organizations can select the appropriate pump for their specific needs hence maximizing performance efficiency.
Factors Affecting Pompa Hydraulic Pump Performance
There are various factors which can affect the performance of hydraulic pump of pompa including the type of pump, fluid viscosity, temperature and pressure. The discussion in this section will explore the factors affecting performance of pompa hydraulic pumps; importance of proper pump performance; and effects of low or high pump performance.
Factors That Affect Pompa Hydraulic Pump Performance
- Type of Pump The kind of a pump used can alter its operation. Types vary in terms of their efficiencies, flow rates as well as pressure capabilities hence some may be more suitable for certain applications than others.
- Fluid Viscosity The liquidity condition is essential to how a hydraulic system’s pump works. Pumping viscous fluids require energy that raises lower pumping efficiency.
- Temperature This could also have an influence on how a pump operates because high temperature thins out the fluid and decreases its efficiency. Furthermore, it is important to note that such conditions lead to damage on internal parts thus reducing durability period.
- Pressure Pressure needed by an application affects the operation of a pumping system. Failure of the required pressure by a specific system then implies reduced effectiveness while functioning may not be possible at all.
Importance Of Proper Pump Performance
Failure to properly perform leads to ineffective use and unreliability in all hydraulic systems. In case the pompa hydraulic pumps do not run with peak performances, their whole assembly gets affected thus reducing productivity and leading into increased maintenance costs and equipment damages that would have been easily avoided.
Effects Of Low Or High Pump Performance
The low flow rate will certainly result in decrease in pressure thereby increasing power consumption. Likewise if any other part like pumps or tanks are running slower than usual it might reduce their lifespan too through heavy tear and wear commencing from there.
High pump performance would cause an increase in energy consumption as well as shortening life span for pumps being used too frequently. When this happens there is also likelihood that such situations shall lead to higher electricity bills besides earlier breakdowns of pumping machines.
In conclusion, several factors can impact the performance of pompa hydraulic pumps, including the type of pump, fluid viscosity, temperature, and pressure. Proper pump performance is essential for the efficient and reliable operation of hydraulic systems. Low or high pump performance can result in decreased productivity, increased maintenance costs, and potential equipment damage. Understanding these factors will help businesses choose the right pump for their application that will ensure it performs optimally with highest efficiency possible.
Selecting the Right Pompa Hydraulic Pump
Selecting a right pompa hydraulic pump for a given purpose is very important in order to have optimum performance and efficiency. Among other things, we will be looking at what to take into consideration before buying a pompa hydraulic pump, different types of pumps for various applications and the essence of choosing the right pump.
Factors to Consider When Selecting a Pompa Hydraulic Pump
- Flow Rate One of the most significant factors to consider when selecting pompa hydraulic pump is required flow rate. Flow rate refers to liquid volume that can be pumped over time and is usually expressed in gallons per minute (GPM) or liters per minute (LPM).
- Pressure Another critical factor you should consider when selecting a pompa hydraulic pump is pressure needed. Pressure represents force per unit area and it is measured in pounds per square inch (PSI) or bar.
- Fluid Viscosity The viscosity of hydraulic fluid used determines how well pumps will function since more energy has to be provided if these fluids are thicker hence difficult to pass through their systems.
- Temperature Fluid temperature as well as environmental conditions under which your pump operates may affect its performance and lifespan.
- Type of Pump In specific applications, different pompa hydraulic pumps exhibit distinct efficiencies, flow rates and pressure capabilities; therefore this could affect their performances in those tasks.
Types of Pompa Hydraulic Pumps for Different Applications
- Gear Pumps Gear pumps are the most common type of pompa hydraulic pump used mostly in low – medium pressure application. They are known for simplicity as they always work properly in many instances.
- Vane Pumps Vane pumps are commonly used where no noise levels are allowed because they produce minimal sound while operating. These are suitable for use only where there is need for low noise levels.
- Piston Pumps Piston pumps have high effectiveness that makes them preferable if high-pressure application is done. They suit places where there must be high pressure and large volumes moved within shortest possible times.
Importance of Selecting the Right Pompa Hydraulic Pump
To achieve optimum performance and efficiency, it is necessary to select the right pompa hydraulic pump. Failure to do so will lead to reduced productivity, increased costs of maintenance and possible mechanical damages. It is thus vital that one looks at the factors mentioned above before selecting a pompa hydraulic pump in such way that it matches particularly the desired flow rate as well as pressure.
Conclusively, one needs to get a suitable pompa hydraulic pump for maximum performance and efficiency. The things you need to look out for include: flow rate, pressure, fluid viscosity, temperature and type of pump. Hydraulics systems have different pumps that are good in various operations and therefore getting the right one is key factor in their reliable operation. So when designing or buying pumps always take these factors into consideration.
Installation and Maintenance of Pompa Hydraulic Pumps
Proper fixing and maintenance of the pompa hydraulic pumps are important for an efficient performance and durability. In this section, we will discuss why proper installation and maintenance of pompa hydraulic pumps is important, how to install and maintain pompa hydraulic pumps, and what tools you need for installing and maintaining them.
Importance of Proper Installation and Maintenance of Pompa Hydraulic Pumps
Correct mounting and service of the pompa hydraulic pumps are necessary for effective functioning of any pump. When incorrectly installed, they may deliver poor performance; cause excessive wear on components in the system as well as damage to some equipment. This would lead to a decrease in performance while power consumption increases resulting in low lifespan.
Steps for Installing and Maintaining Pompa Hydraulic Pumps
- Installation The following steps should be followed for the installation of pompa hydraulic pumps:
- Make sure that the pump is compatible with both the hydraulic system as well as its application requirements.
- Place it in a cool, clean dry place away from heat sources.
- Ensure proper alignment with other parts before doing mounting.
- Connect pipes to pump’s ports properly such that there is no leak or loose connection at all.
- Make sure that your system has enough fluid (oil) up to normal level without air bubbles inside it before running tests on any pump.
- Finally make sure there are no leaks or abnormal noises when running the hydraulic system.
- Maintenance The following steps should be followed for the maintenance of pompa hydraulic pumps:
- Always check fluid levels ensuring clean free from contamination fluids.
- Check pressure rate regularly to ensure it complies with specifications required by manufacturer.
- Check pump condition regularly including its components seeking wear signs, breakage points or even leakage points.
- Repair or replace worn out constituents immediately after detection within your pump set-up at all times.
- Keep clear any dirt particles from blocking your pump vents during operation by cleaning them often.
Tools Required for Installation and Maintenance of Pompa Hydraulic Pumps
The following tools are required for the installation and maintenance of pompa hydraulic pumps:
- Spanners and sockets to tighten or loosen couplings
- Pressure gauge that is used to monitor pressure/flow rate of hydraulic fluid in system
- A device that checks fluid level in a reservoir
- Detergents, cloths, brushes etc. used in pump cleaning
- Replacement parts that are required when changing nonfunctional items.
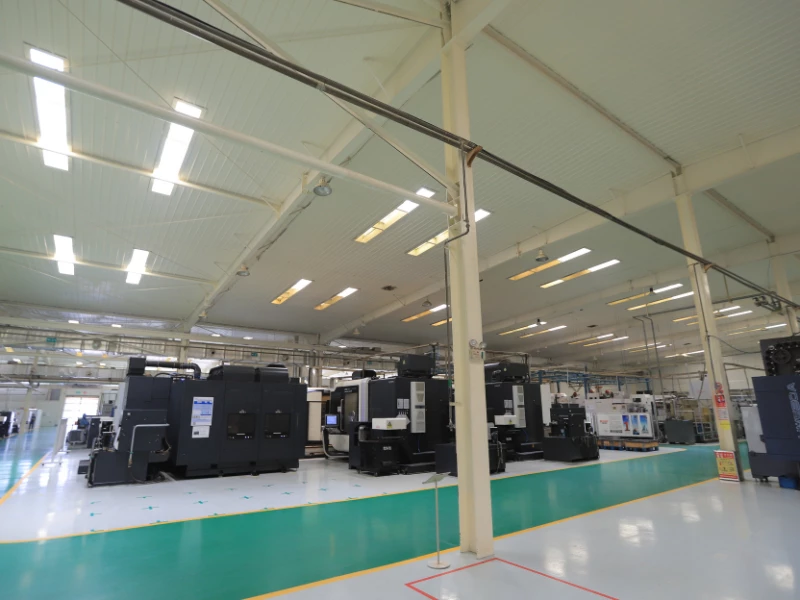
pompa hydraulic pump
In conclusion, proper installation and maintenance of pompa hydraulic pumps are essential for optimal performance and longevity. The steps for installing and maintaining pompa hydraulic pumps should be followed carefully, ensuring that the pump is installed correctly and maintained regularly. The tools required for installation and maintenance should be on hand, ensuring that any issues can be addressed quickly and efficiently.
Common Problems with Pompa Hydraulic Pumps
Issues of Mechanical System Like all other mechanical systems, pompa hydraulic pumps may have faults. In this part, we will look at the common problems with pompa hydraulic pumps, symptoms of pump problems and their remedies.
Common Problems with Pompa Hydraulic Pumps
- Overheating Overheating is also a common issue that occurs in pompa hydraulic pumps and it can be caused by several things such as low amounts of fluid, high viscosity and the temperature during that time period. Overheating may lead to damage on the pump’s internal parts or reduce its potential lifespan.
- Leaks Leaks in your hydraulic system can cause a loss of pressure, reduced performance and even damage equipment. Some common causes of leaks are damaged seals, cracked hoses and loose connections.
- Cavitation Cavitation occurred when air bubbles were formed in the hydraulic system thereby resulting to loss of pressure and poor performance by the pump. Low fluid levels, high viscosity fluids or plugged suction filter can cause cavitation.
- Noisy Operation There are various causes for a noisy operation including worn internal components such as bearings or loose components that require fixing.
Symptoms of Pompa Hydraulic Pump Problems
Below are some symptoms related to problems with pompa hydraulic pumps:
- Reduced flow rate
- Reduced pressure
- Overheating
- Noisy operation
- Vibration
- Leaks
- Cavitation
Solutions to Common Pompa Hydraulic Pump Problems
Some possible solutions for these common problems faced by pompa hydraulic pumps are as follows:
- Overheating In order to deal with overheating; one has to ensure right amount of fluid supply; keep appropriate type/ grade/viscosity quantities especially under application conditions; also know if ambient temperatures fall within defined range. If not solved you can use cooling mechanism or replace it with efficient pumps.
- Leaks Locate damaged seals, hoses or connections so as to rectify leaks. You should regularly check out your whole system looking for any signs concerning leakage so as to deal with it at an earlier stage.
- Cavitation In case of cavitations; ensure your fluid level is right, proper viscosity for this purpose and that the suction filter is clean. If it is not resolved, upgrade a pump that has a higher flow rate or pressure capacity.
- Noisy Operation Find out where the damaged bearings are, loose components or worn internal parts so as to address this issue. Check your components regularly for any signs indicating they are wearing out or if they are already damaged.
To sum up, pompa hydraulic pumps may occasionally encounter challenges such as overheating, leaks, cavitation and noisy operation. Prompt identification of these symptoms and fast solution will help in preventing equipment damage, thus ensuring optimal performance and efficiency. Regular maintenance including inspections and repairs can go a long way in preventing these issues from happening in the first instance.
Troubleshooting Pompa Hydraulic Pumps
Troubleshooting pompa hydraulic pumps is a must in order to ascertain the problems and tackle them at the earliest possible time. In this part of the paper, we shall discuss the importance of troubleshooting pompa hydraulic pumps, steps to troubleshoot pompa hydraulic pumps, and tools required for troubleshooting.
Importance of Troubleshooting Pompa Hydraulic Pumps
It’s critical that trouble shooting pompa hydraulic pumps be carried out early enough before they cause further damages on equipment thus minimizing down time as well as improving on performance and efficiency. Regular maintenance and troubleshooting can help you identify potential problems before they happen.
Steps to Troubleshoot Pompa Hydraulic Pumps
The following are steps which should be adhered to when trouble shooting pompa hydraulic pumps:
- Identify the Problem The first stage in trouble shooting pompa hydraulic pumps is identifying what the problem is. One can do this by observing what is happening ,such as reduced flow rate or noisy operation, performing diagnostic tests like checking fluid level and pressure.
- Gather Information Once you have identified the problem, gather information about the hydraulic system and pump including specifications, operating conditions, and maintenance history. This will help identify probable causes of problem thus guiding your trouble shooting process.
- Perform Diagnostic Tests Another option entails performing diagnostic test aimed at getting more detailed description concerning how it has occurred such as checking fluid level among others. It would determine if there are any worn out parts or damaged ones based on the flow or pressure levels.
- Identify Potential Causes Identify potential causes of the problem based on gathered information and performed diagnostic tests. Low fluid levels, damaged seals clogged filters are some common causes of problems with poma hydraulics while worn out parts or damaged components could also lead to malfunctioning issues.
- Address the Problem After knowing what exactly caused your pump not to function properly then address it through repairing/ replacing all those worn-out/damaged parts especially cleaning up your system maintaining proper alignment & mounting of the pump.
- Test the Pump After solving the problem, then test the pump to make sure it is working as expected and within given parameters. Continue monitoring both pump and hydraulic system for any further trouble shooting.
Tools Required for Troubleshooting Pompa Hydraulic Pumps
The following tools are needed when troubleshooting pompa hydraulic pumps:
- Wrenches and sockets for tightening and loosening connections
- Hydraulic pressure gauge for checking pressure and flow rate
- Fluid level gauge for checking fluid level
- Diagnostic tools such as stethoscope to identify noisy components among others
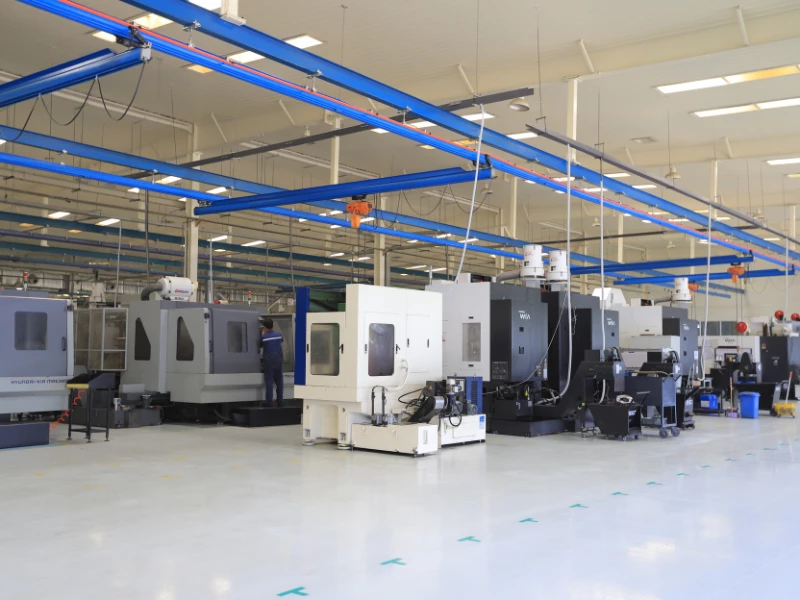
pompa hydraulic pump
In conclusion, troubleshooting pompa hydraulic pumps is critical for identifying and addressing problems as soon as possible. In troubleshooting pompa hydraulic pumps, you identify the problem, gather information, perform diagnostic tests, identify potential causes, address the problem, and test the pump. Finally, wrenches, sockets, hydraulic pressure gauges; fluid level gauges; diagnostic tools are essential tools needed in trouble shooting. Regular troubleshooting and maintenance helps prevent issues that can occur hence ensuring optimum performance efficiency of pompa hydraulics.